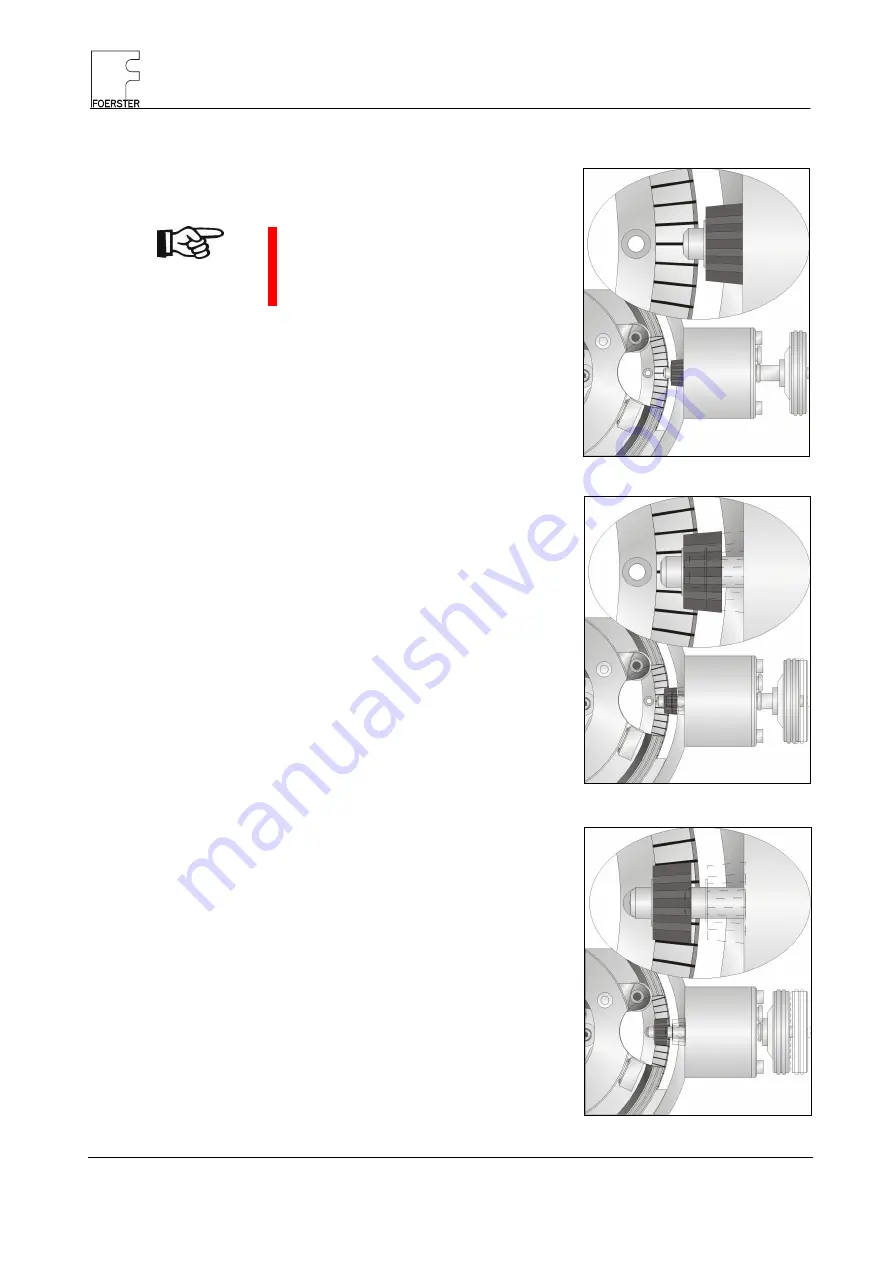
SENSOR SYSTEM Ro 35 L
4.3 Adjusting nominal diameter
OPERATION
4-12
6.461.21 - 2008/06
Changing adjustment value
NOTE
!
Brake the rotating head to
a standstill with the hand
brake before adjustment!
Push in the hand wheel
and turn until the actually
valid diameter has reached
the adjustment position.
Push in the hand wheel
completely in adjustment
position and set new nominal
diameter.
Pull the hand wheel back
into idle position.
Fig. 4.13 Idle position
Fig. 4.14 Finding adjustment position
Fig. 4.15 Adjustment position