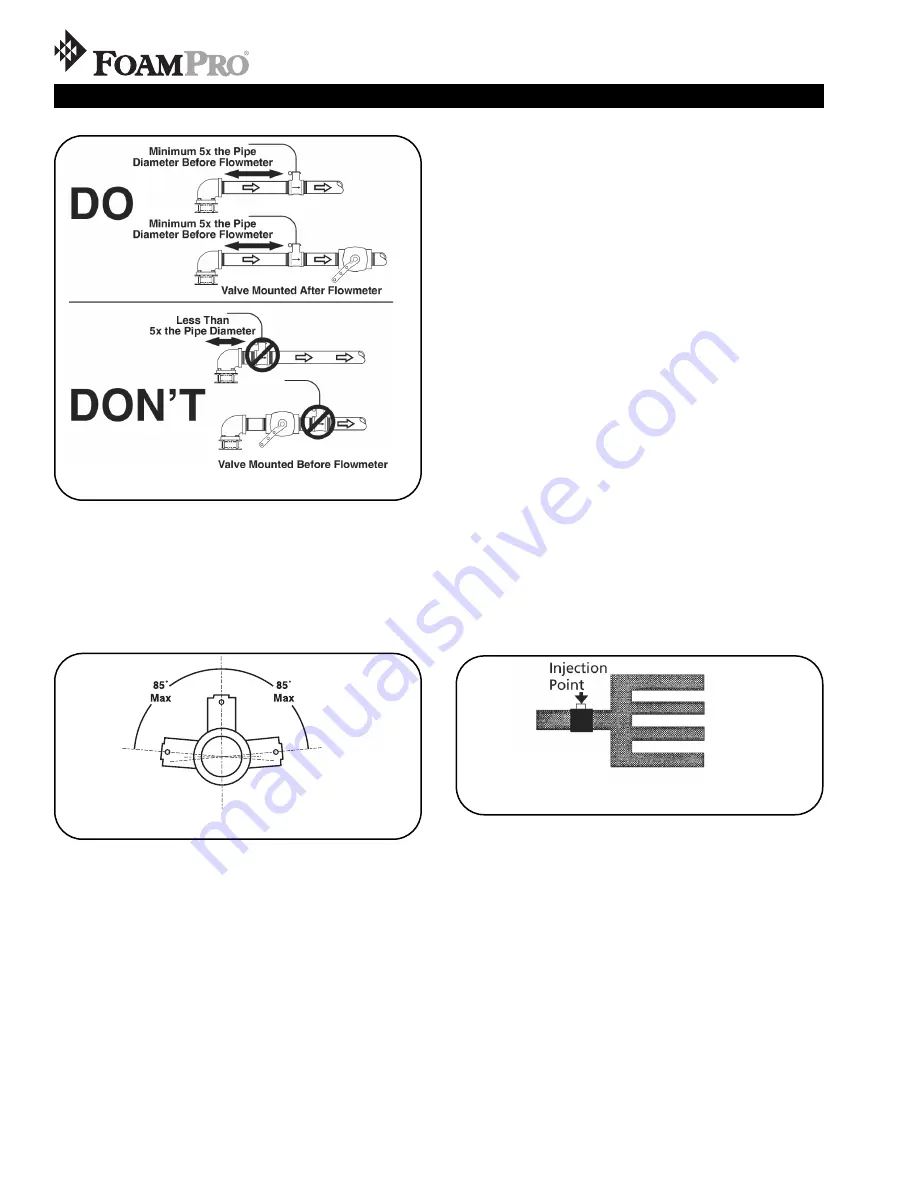
20
Installation and Operation Manual
Figure 8-2 Flowmeter Placement
Figure 8-3 Flowmeter Position Range
The FoamPro paddlewheel-style flowmeter fittings are
specially designed tees that make inspection and
maintenance of the flow sensor easy. The threads of
the tees are available in NPT with grooved victaulic
ends, or BSP with grooved victaulic ends. In horizontal
runs the tees should be mounted as close to upright as
possible within the range shown in Figure 8-3.
With the use of a MultiFlo interface, two to four
flowmeters may be monitored simultaneously. A single
injection point that will supply foam agent to all foam
discharge outlets is required. See Form 880, provided
with the MultiFlo System, for further information.
Foam Discharge Flowmeters
The foam flowmeters shipped with the unit are
designed to give maximum performance and accuracy
over the full range of operations for the system. The
foam flowmeters are to be mounted in a horizontal
position. A straight run of hard piping before and after
the flowmeter is required. The following chart specifies
the minimum straight run required:
Model
Pipe
Minimum Straight Run Pipe
Size
Before
After
Flowmeter
Flowmeter
3020& 3040 3/4” 8-1/4"(210 mm) 4-1/8"(105mm)
3060
1"
8-1/4"(210 mm) 4-1/8"(105mm)
3090
1-1/4" 8-1/4"(210 mm) 4-1/8"(105mm)
3150
1-1/2" 10-1/4"(260 mm) 5-1/4"(133 mm)
3300
2"
10-1/4"(260 mm) 5-1/4"(133 mm)
Injection Point
The position of the injection point MUST be in a place
that is common to all discharges which require foam
capability. This position may be before or after the
main water flowmeter, but not within the straight run
distance required for the flowmeter as previously
described. A separate injection point is not possible for
each discharge. If multiple flowmeters are used, the
injection point must be installed before the flowmeters
at the inlet to their common manifold (See Figure 8-4).
Most foam concentrates by nature mix with water very
quickly, so each discharge from a manifold will receive
equal amounts of foam concentrate if the manifold is
properly designed and installed. A static mixer or
special mixing considerations may need to be designed
into the system, especially when using thicker foam
concentrates and those that may not readly mix with
water.
Figure 8-4 Injector Fitting Placement
for Multiple Discharge
Foam Concentrate Check Valves
Check valves are provided to prevent foam concentrate
flow from the concentrate tank through the injection
point and into the main waterway when the system is
not in use. This is a NFPA requirement. A check valve
of the proper size is supplied for the standard systems.
See Figure 8-1 for component placement. The
concentrate check valves have a minimum cracking
pressure of 4 PSI (0.1 BAR) and are pressure rated to
400 PSI (28 BAR) minimum working pressure. It is a
good idea to inject foam concentrate at a horizontal or
higher angle to allow water and debris in the water line
to drain away from the check valve(s) as shown in
Figure 8-5. This will avoid sediment deposits or
formation of an ice plug in cold weather applications.
Injection
Point