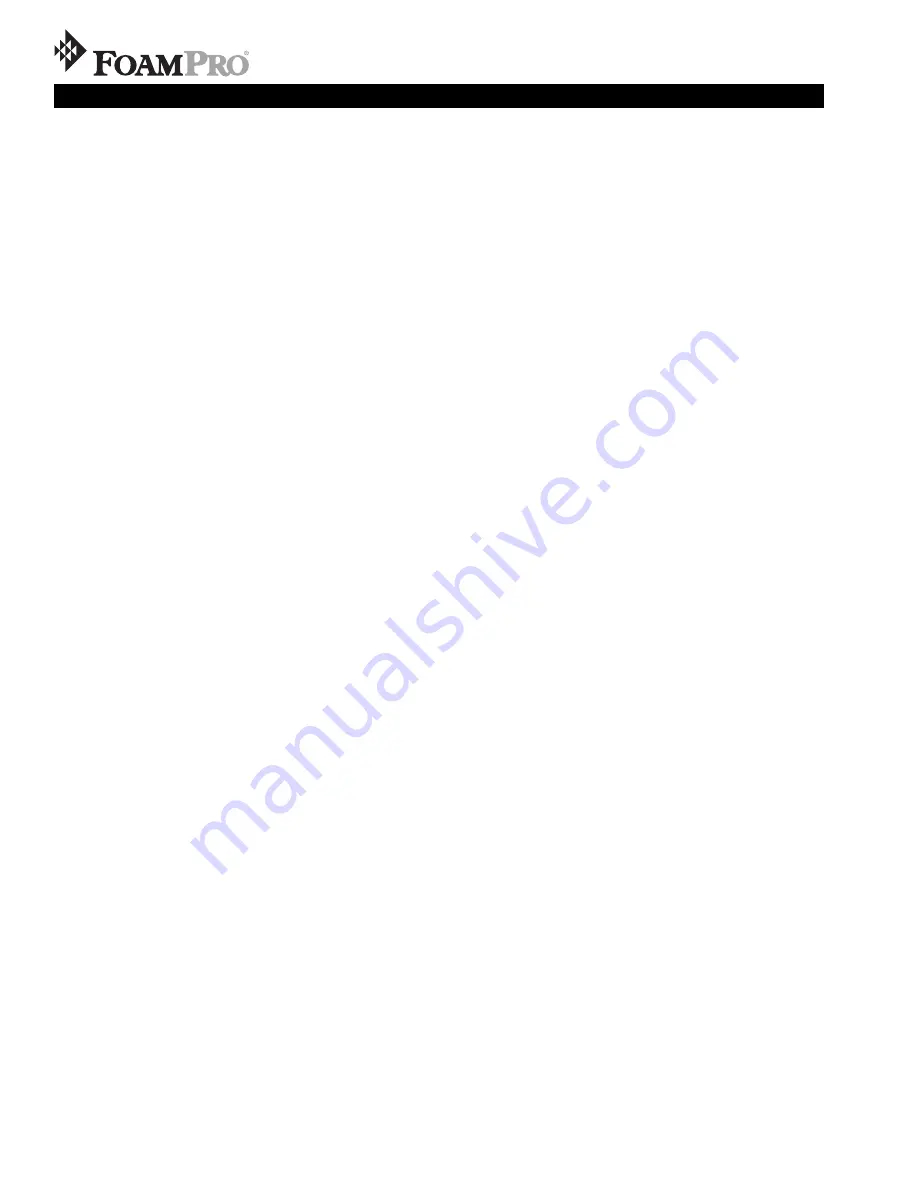
10
Oil Cooler
An oil cooler capable of maintaining the temperature of
the hydraulic oil at 140° to 180°F (60° to 82°C) is
required. Use of an air-to-oil radiator-type heat
exchanger mounted in front of the apparatus radiator
should provide adequate cooling for the hydraulic
system oil. An electric fan attached to the oil cooler
permits mounting of the oil cooler anywhere fresh air
circulation is available. A thermostat is required to be
included for quick warm-up of the oil in cold climates.
Check the system specifications page in Section 15 for
minimum heat load information to properly size the
cooler.
Oil-to-water heat exchangers can be installed, but they
present special problems such as sediment
accumulation, drainage and overheating when running in
standby mode for extended periods without discharging
water. If a hydraulic oil-to-water heat exchanger is to be
used, proper maintenance, monitoring, and pumping
procedures must be followed. The oil-to-water
exchangers must be installed per the manufacturer’s
recommendations and NFPA requirements.
Hydraulic Oil
Ratings and data for the FoamPro AccuMax SP system
are based on operating with premium hydraulic fluids
containing oxidation, rust, and foam inhibitors. These
premium fluids include premium turbine oils, API CD
engine oils per SAE J183, M2C33F or G automatic
transmission fluids (ATF), Dexron II, III, or IV (ATF)
meeting Allison C-3 or Caterpillar TO-2 requirements.
The recommended hydraulic fluid operating viscosities
are typically 70 to 278 SUS (12 to 60 cSt) for optimum
performance. The hydraulic oil should have an ISO rating
of between 32 to 68 depending on climatic conditions.
Hydraulic Hoses and Fittings
High pressure hydraulic hoses and fittings are to be rated
at least at the maximum working pressure of the system.
To reduce the potential for leaks at the hydraulic fittings,
use SAE 37° flare JIC-type fittings or SAE straight thread
O-ring fittings. See the table for required fitting sizes,
minimum hose size, and minimum hose pressure ratings
for the hydraulic components in Section 15.
Foam Concentrate Suction Lines
Fittings and hoses from the foam tank to the inlet of the
foam pump must be supplied. Use the minimum inside
diameter or larger clear suction hose shown below for
the corresponding system depending on the viscosity of
the foam concentrate. Many class B foams are more
viscous and will require one size larger inside diameter
hoses.
Model
Min. Hose ID
3020/3040
1-1/2”
3060
2”
3090
3”
3150
3”
3300
4”
Use fittings and components that are rated for 23” Hg
(584.2mm) vacuum and 50 PSI (3 BAR) pressure or
better. The components used must be compatible with
the foam concentrates used. Fittings used must be
made of brass or 300 series stainless steel. If a flushing
system is to be used, the pressure rating of those
components subjected to main water pump pressure
are to be rated to 400 PSI (28 BAR) or better.
A drain/air bleed valve should be provided to allow
draining of the tank and easier priming of the foam
pump.
Foam Concentrate Discharge Lines
Fittings and hoses from the discharge of the foam pump
to the foam injection point must be supplied by the
installer. Hoses and fittings are to be 3/4” (19mm) for
the 3020 and 3040; 1” (25.4mm) for the 3060; 1-1/4”
(31.8 mm) minimum for the 3090; 1-1/2” (38.1mm) for
the 3150; and 2” (50.8mm) for the 3300 systems inside
diameter, rated at or above 400 PSI (28 BAR) working
pressure. Fittings and hoses must be compatible with all
foam agents to be used with the system. Use fittings of
brass or 300 series stainless steel.
WARNING: Do not use air brake tubing for foam
systems as the tubing is not compatible with most
foam concentrates.
The foam flowmeter supplied with the system is to be
installed in the foam concentrate discharge line of the
foam pump. This requires a straight length of brass or
300 series stainless steel pipe 10” (254mm) minimum
before and 5” (127mm) minimum after the flowmeter.
This ensures laminar flow through the flowmeter. Failure
to comply with these minimum dimensions will affect the
accuracy of the entire foam system.
Foam Concentrate Tank(s)
Foam concentrate tanks must be supplied to suit the
capacity required for the apparatus application. The
tank(s) should meet NFPA minimum standards for the
design capacity, including filler size, vapor pressure
venting, and drain facilities.
Installation and Operation Manual