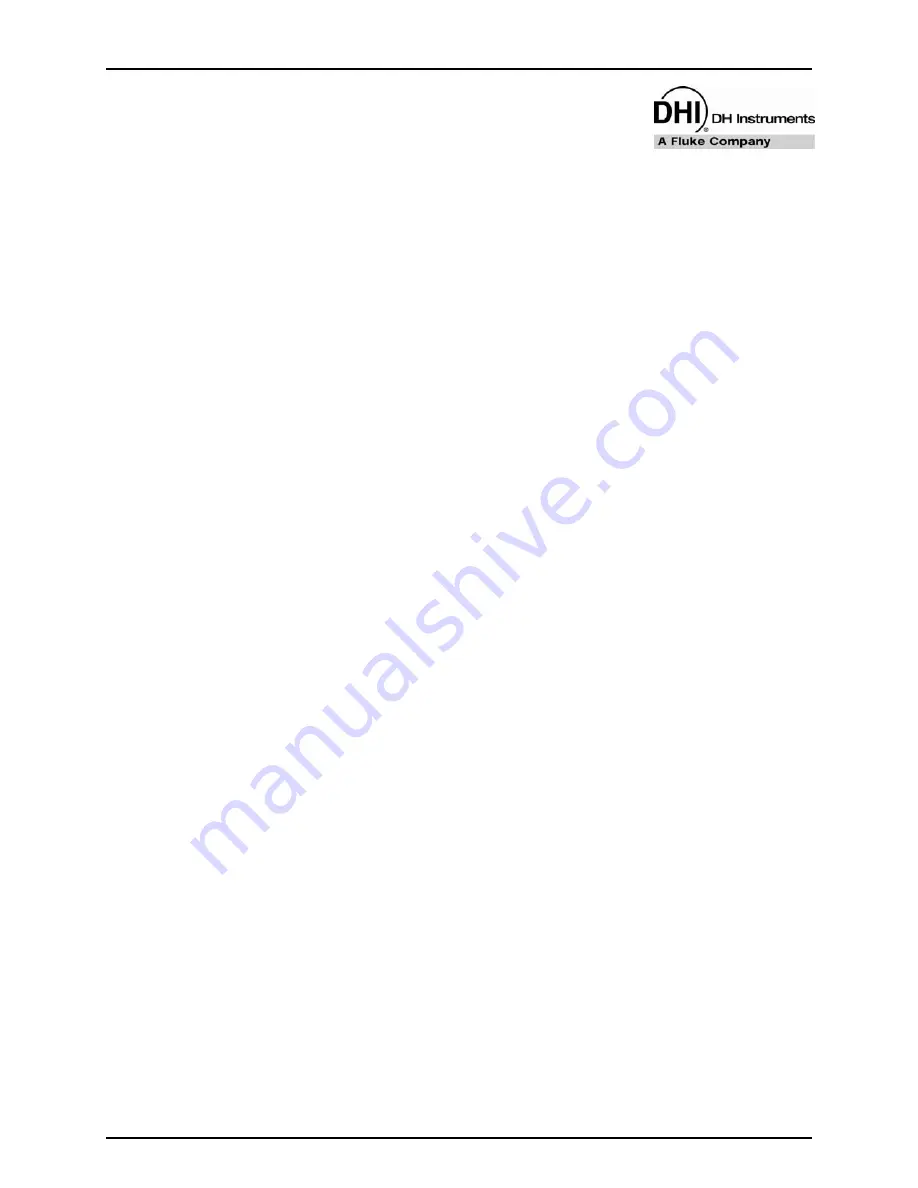
3. OPERATION
Page 13
© 2007 DH Instruments, a Fluke Company
3
3
.
.
O
O
P
P
E
E
R
R
A
A
T
T
I
I
O
O
N
N
3.1
GENERAL OPERATING PRINCIPLE AND INFORMATION
The purpose of the GB-152-AF booster is to automatically boost gas pressure to very high pressure. The
value of very high pressure that is generated depends on the drive air pressure setting. The unit generates
high pressure using a Pneumatically Operated Gas Booster Pump and a Drive Air Control Kit.
GAS BOOSTER PUMP
The booster pump is a Pascal press utilizing two pistons connected together on the same axis having a
normal area ratio of 152:1. The booster is a two-stroke, single stage reciprocating pump that generates
gas pressure 152 times greater than the shop drive air applied to the pump. The pump operates
automatically, provided drive air is supplied to the
DRIVE ADJUST
regulator and the regulator is set to at
least 140 kPa (20 psig). Operation is continuous until the outlet pressure is 152 times the shop drive air
pressure. Then, the opposing forces within the pump are in equilibrium and the pump stalls.
For example, using a GB-152-AF with the drive air pressure set to 45 psi (300 kPa), the pump will run
until the high pressure output reaches approximately 152 x 45 = 6840 psi.
The drive air (low pressure) section of the booster consists of a piston, cylinder, air cycling valve, pilot
valve and vent section. This section provides the reciprocating action and compression force needed to
operate the booster and generate the high pressure gas. Drive air is channeled to the appropriate side of
the piston (compression or suction stroke) by the air cycling valve. When the piston reaches full stroke, a
pilot valve is mechanically activated causing the air cycling valve to change position. Shop drive air is
routed to the opposite side of the piston reversing piston direction where a second pilot valve is activated
repeating the process.
The high pressure section of the booster consists of a small piston and an inlet/outlet check valve
assembly. The small piston moves forward and backward with the air drive piston. During the suction
stroke (backward movement), the outlet check valve closes and the inlet check valve opens letting supply
high pressure gas enter the compression chamber. During the compression stroke, the inlet check valve
closes and the outlet check valve opens letting boosted gas out of the pump.
The compression ratio of the high pressure piston is 25:1 (for both models). Maximum output pressure is
limited by the instrument gas supply pressure. For example, with 300 psi applied, maximum output
pressure cannot exceed 300 x 25 = 7 500 psi.