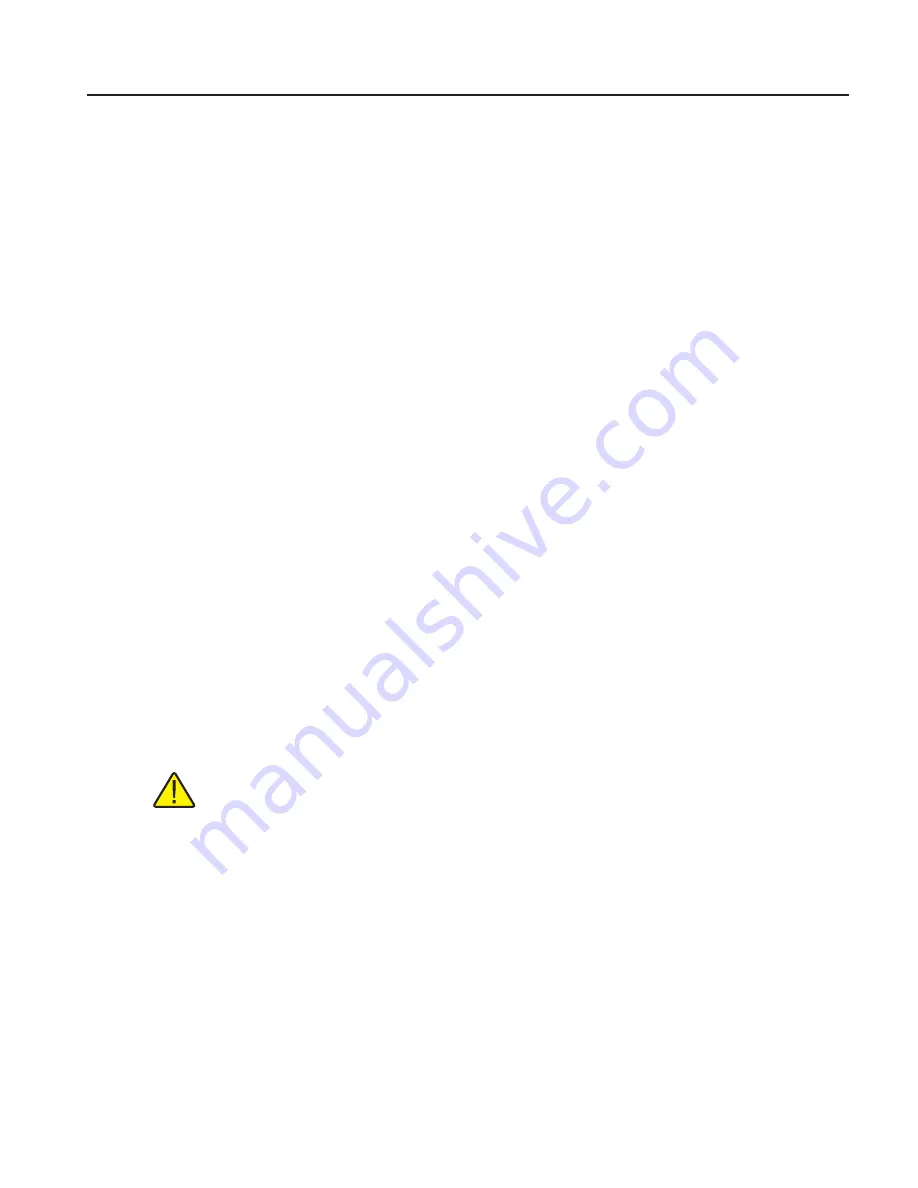
27
ControllerOperation
CalibrationParameters
HALF
New duplex mode setting
Press “SET” to accept the new setting or “EXIT” to abort the operation and skip to the
next parameter in the menu.
6.11.4 Linefeed
The final parameter in the serial interface menu is the linefeed mode. This parameter
enables (on) or disables (off) transmission of a linefeed character (LF, ASCII 10) after
transmission of any carriage-return. The linefeed parameter is indicated by,
LF
Flashes for one second and then the serial linefeed setting
is displayed
On
Current linefeed setting
The mode may be changed using the up or down arrows (u d).
OFF
New linefeed setting
Press “SET” to accept the new setting or “EXIT” to abort the operation and skip to the
next parameter in the menu.
6.12 Calibration Parameters
The operator of the instrument controller has access to a number of the calibration
constants namely the Hard Cutout, R0, ALPHA, and DELTA. These values are set at
the factory and must not be altered. The correct values are important to the accuracy
and proper and safe operation of the instrument. Access to these parameters is
available to the user so in the event the controller memory fails the user may restore
these values to the factory settings. The user should have a list of these constants and
their settings with the instrument manual.
CAUTION:
DO NOT change the values of the instrument calibration constants
from the factory set values. The correct setting of these parameters is important
to the safety, proper operation, and performance of the instrument.
The calibration parameters menu is indicated by,
CAL
Calibration parameters menu
Press “SET” five times to enter the menu. The calibration parameters menu contains
the parameters, Hard Cutout, R0, ALPHA, and DELTA, which characterize the
resistance-temperature relationship of the platinum control sensor. These parameters
may be adjusted to improve the accuracy of the calibrator.
The calibration parameters are accessed by pressing “SET” after the name of the
parameter is displayed. The value of the parameter may be changed using the up or
down arrow. After the desired value is reached, press “SET” to set the parameter to the
1.888.475.5235
Fluke-Direct
.com
Summary of Contents for 9100S
Page 8: ...1 888 475 5235 info Fluke Direct com Fluke Direct com...
Page 16: ...1 888 475 5235 info Fluke Direct com Fluke Direct com...
Page 18: ...1 888 475 5235 info Fluke Direct com Fluke Direct com...
Page 26: ...1 888 475 5235 info Fluke Direct com Fluke Direct com...
Page 38: ...1 888 475 5235 info Fluke Direct com Fluke Direct com...
Page 42: ...1 888 475 5235 info Fluke Direct com Fluke Direct com...
Page 44: ...1 888 475 5235 info Fluke Direct com Fluke Direct com...
Page 48: ...1 888 475 5235 info Fluke Direct com Fluke Direct com...
Page 50: ...1 888 475 5235 info Fluke Direct com Fluke Direct com...