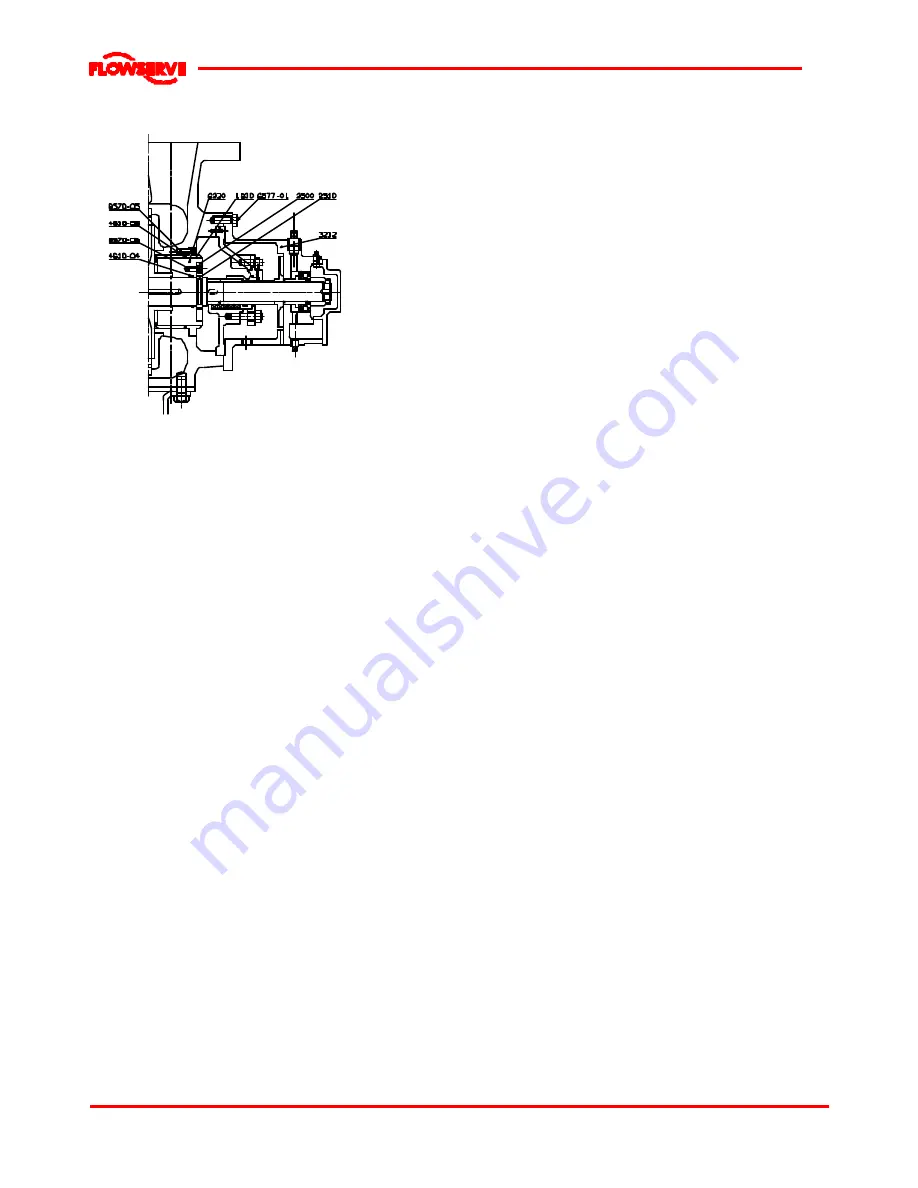
WDX USER INSTRUCTIONS ENGLISH 71576322 06-05
Page 36 of 46
®
6.8.5.2 Variant WDXC
Dismount the line bearing assembly; see section
6.8.3.
Remove the seal component.
Remove the drum screws [6570-06] and the drum
ring [2500].
Remove the split ring [2510].
Pull out the drum by means of threaded holes in the
drum.
Remove the bushing cap screws [6570-05].
Pull out the bushing [1600] by means of threaded
holes in the bush.
6.8.6 Disassembly of pump casings
After having dismounted bearings and shaft seals,
unscrew the four tie rod nuts. The rest of dismounting
is self explanatory when viewing the respective
sectional drawing.
For WDX pumps of construction M4 M5 M6 M7 (steel
or stainless steel), an intermediate bushing is
assembled at the middle of the pump. Take note of its
position and on reassembly, assemble it in the same
place.
6.9 Inspection of components
With pump dismantled, clean all parts and check for
worn and damaged areas. Clean and inspect gasket
and O-rings seals. Check wearing ring, interstage
seal and balancing drum surfaces. Casing and
impeller wearing ring and interstage seal surfaces
may be either be part of the individual casing diffuser
and impeller or separate parts. See sections 3.5.2
and 3.5.3 for standard clearances for impeller
wearing ring, interstage seal and balancing drum.
6.9.1 Precision surfaces
Check for damage to precision surfaces that locate
casings and bearing housings to preserve proper
internal alignment. Check for corrosion due to
leakage. Check axial impeller hub and sleeve
surfaces for damage to insure proper axial alignment
of rotor.
6.9.2 Stuffing box
Remove any dirt or scale from stuffing box cavity.
Replace O-ring seals. Replace gland studs if badly
corroded.
6.9.3 Mechanical seals
It is not recommended that mechanical seals be
reused. Using an old one leaves too much chance of
failure to make the risk worthwhile, considering the
usual cost of installing and removing a pump from its
system. Attempts to lap the mechanical seal faces
may be possible but require specialized technical
knowledge, skills and equipment beyond the scope of
these instructions. Complete mechanical seal rotors
and seats are available from your FLOWSERVE
representative as are any other repair parts.
6.9.4 Stuffing box sleev es
Check the stuffing box shaft sleeve outside surface
for scoring. If used with packing, any scoring will
shorten the life of the packing proportional to the
amount of scoring present. If used with a mechanical
seal, the outside surface must not be scored in the
area where the seal rotor bellows or sealing ring
touches.
6.9.5 Ball bearings
It is not recommended that the bearings be reused.
However, if reuse is intended, clean bearings with
petroleum solvent or kerosene and inspect for any
indications of damage or wear, such as metal
shavings, rust or surface galling. Further, judge the
condition of the bearings by rotating by hand.
Replace any bearing which shows any sign of
damage or that has been in service for an extended
period. Serviceable bearings should be spun in light
oil to completely remove the solvent after cleaning, or
coated by hand with an anti-corrosion agent if they
are not to be reassembled immediately and wrap at
once in clean oil proof paper while awaiting
reassembly. The use of chlorinated solvents of any
kind is not recommended in bearing cleaning
operations because of the rust hazard involved, nor is
the use of compressed air found desirable in cleaning
operations.