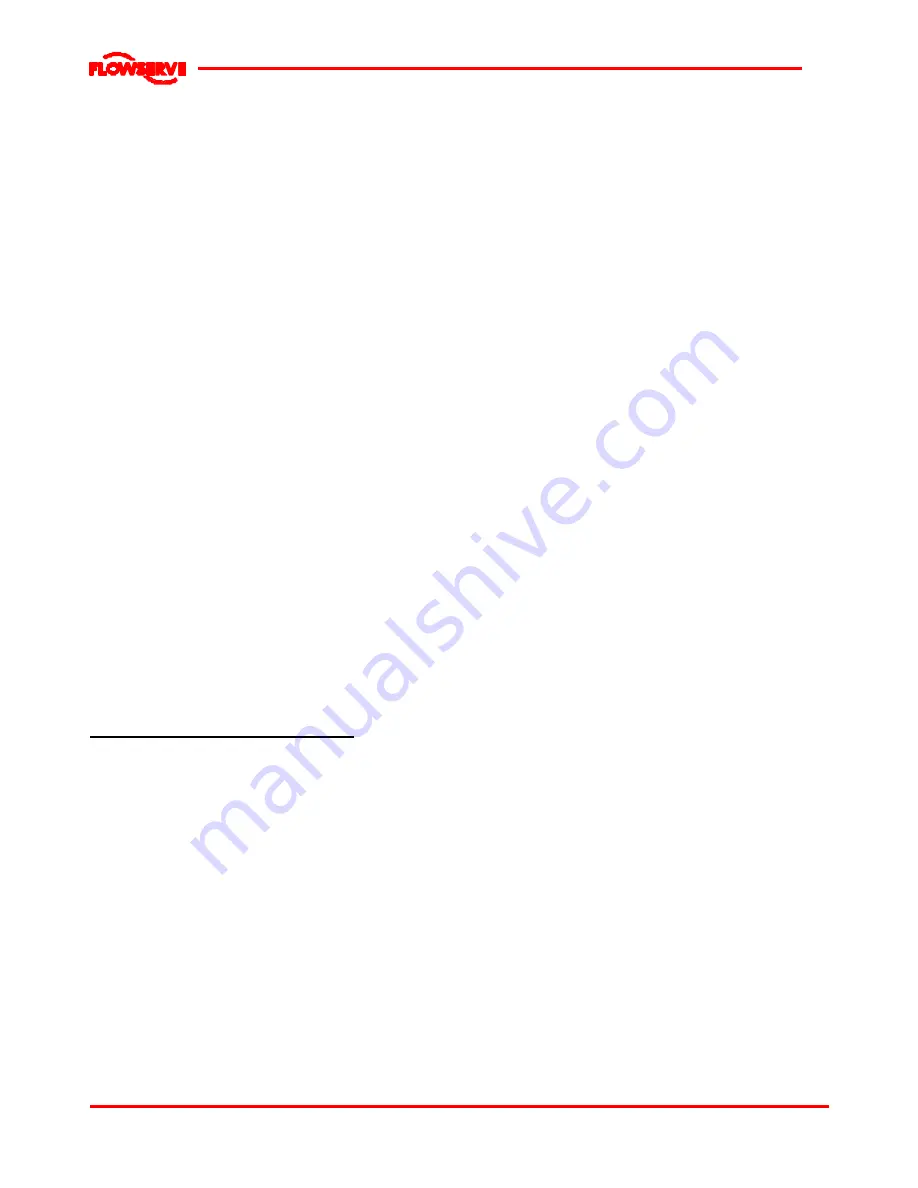
WDX USER INSTRUCTIONS ENGLISH 71576322 06-05
Page 10 of 46
®
In areas where the staff has to intervene, remember
that when the level of the sound pressure is:
Below 70 dBA :It is not necessary to take
special precautions.
Above 70 dBA :People working continuously in
the machine room must be
supplied with protective devices
against noise.
Below 85 dBA :No particular measures need to be
taken for casual visitors staying in
the room during a limited period.
Above 85 dBA :The room must be considered as a
dangerous area because of the
noise and a warning sign must be
fixed at each entry warning the
people coming into the room, even
for a short period, that they must
wear hearing protection.
Above 105 dBA:Special hearing protection adapted
to this noise level and to the
spectral noise components must
be installed and a warning sign to
this effect erected at each entry.
The staff in the room must wear
ear protection.
Make sure that the noise, which travels through the
walls and windows, does not generate too high noise
levels in the machine room's surroundings.
2 TRANSPORT AND STORAGE
2.1 Consignment receipt and unpacking
Immediately after receipt of the equipment it must be
checked against the delivery and shipping documents
for its completeness and that there has been no
damage in transportation.
Any shortage and or damage must be reported
immediately to Flowserve Pump Division and
received in writing within one month of receipt of the
equipment. Later claims cannot be accepted.
Check any crate, boxes and wrappings for any
accessories or spare parts that may be packed
separately with the equipment or attached to side
walls of the box or equipment.
Each product has a unique serial number. Check that
this number corresponds with that advised and
always quote this number in correspondence as well
as when ordering spare parts or further accessories.
2.2 Handling
2.2.1 General instructions concerning handling
Boxes, crates, pallets or cartons may be unloaded
using fork-lift vehicles or slings dependent on their
size and construction. See 2.3.1 for positioning of
slings.
To lift heavy pieces above 55 lb (25 kg), use a crane
corresponding to the mass and in accordance with
the current local regulations.
To lift machines or pieces with one or several lifting
rings, only use hooks and chains in compliance with
the local regulations concerning safety. Never put
cables, chains or ropes directly on or in the lifting
rings. Cables, chains or lifting ropes must never
present excessive bending.
Never bend the lifting hooks, lifting rings, chains,
etc... They are only made to endure stresse s within
calculated limits. Remember that the capacity of a
lifting device decreases when the direction of the
lifting force direction makes an angle with the device
axis.
To increase the safety and efficiency of the lifting
device, all the lifting elements must be as
perpendicular as possible. If necessary a lifting beam
can be placed between the crane and the load.
When heavy pieces are lifted up, never stay or work
under the load or in the area which could be in the
path of the load if it were to swing or fall away. Never
leave a load hanging from a crane. The acceleration
or the deceleration of lifting equipment must stay in
the safety limits for the staff.
A crane must be positioned in such a way that the
load will be raised perpendicularly. Where possible
necessary precautions must be taken to avoid the
swing of the load. For example use two winches
making approximately the same angle, less than 30°,
with the vertical.