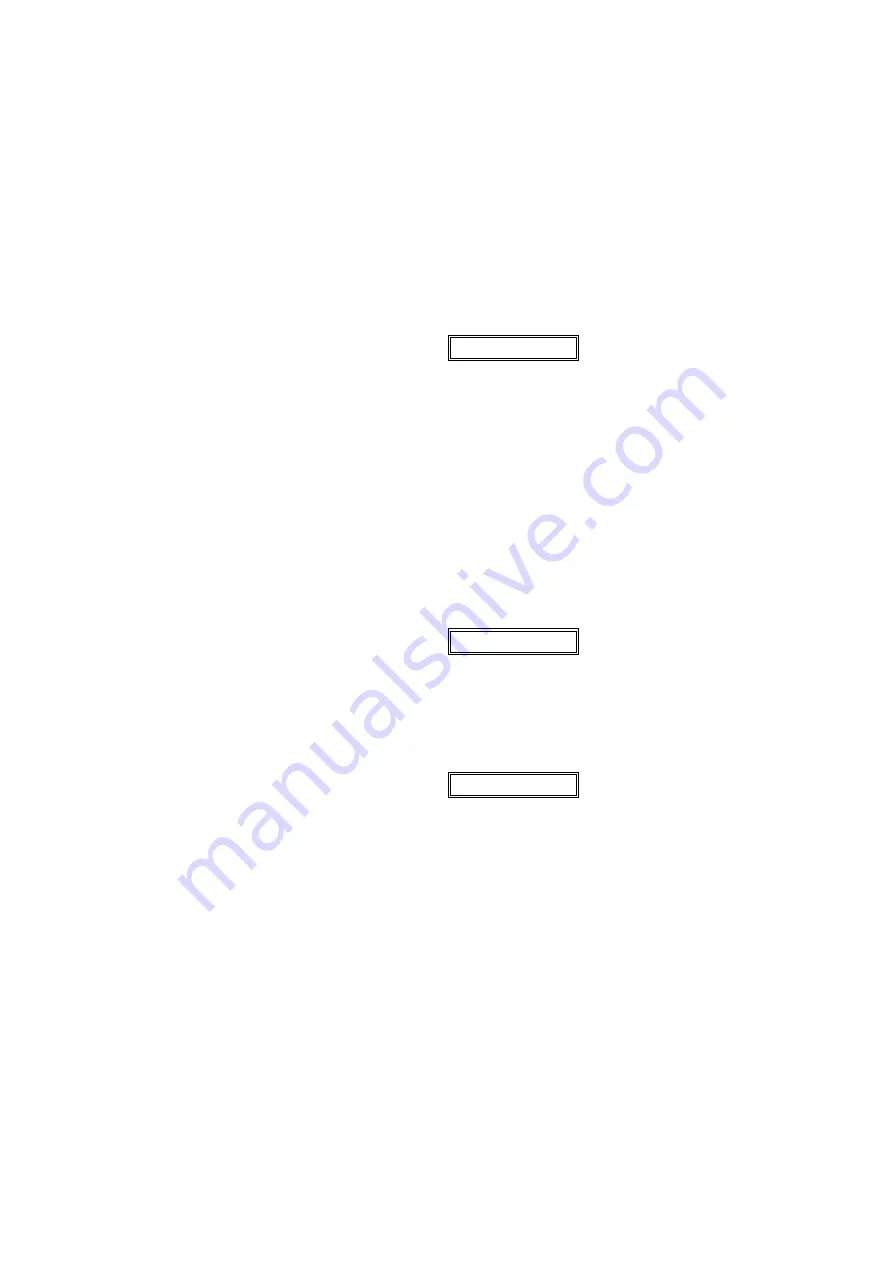
30
2.14
Piping
2.14.1 Suction and Discharge Piping
These units are furnished for a particular service condition. Changes in the hydraulic system may
affect performance adversely. This is especially true if the changes reduce the pressure at the
suction or if the liquid temperature is increased. In case of doubt contact FLOWSERVE
Suction and discharge piping should be of ample size, be installed in direct runs, and have a
minimum of bends. Double bends must be avoided in suction line and a straight run of pipe, equal
8 to 10 times the pipe diameter is desired directly upstream of the suction nozzle.
NOTE
Provision must be made to support piping external to the pump to prevent excessive nozzle loads,
maintain pump/driver alignment and avoid pipe induced vibrations.
Install a check valve and a gate valve in the discharge pipe of the pump. When the pump is
stopped, the check valve will protect the pump against excessive pressure and will prevent the
pump from running backward. The check valve should be installed between the gate valve and the
pump nozzle in order to permit its inspection.
Keep the suction pipe from the source short and direct. Use a suction pipe equal to or one size
larger than the pump suction nozzle. Keep the suction pipe free of all air pockets. (Vent as
required).
IMPORTANT
A spool piece should be installed in suction line so that the suction strainer may be
installed and removed with a pressure gauge between the strainer and pump
2.14.2 Bypass Line
CAUTION
Operation at low flows results in pump horsepower heating the liquid. A bypass may be
required to prevent vaporization and subsequent pump damage. Refer to local
FLOWSERVE branch to determine if a bypass is required. Mechanical damage may result
from continuous operation at flows less than specified.