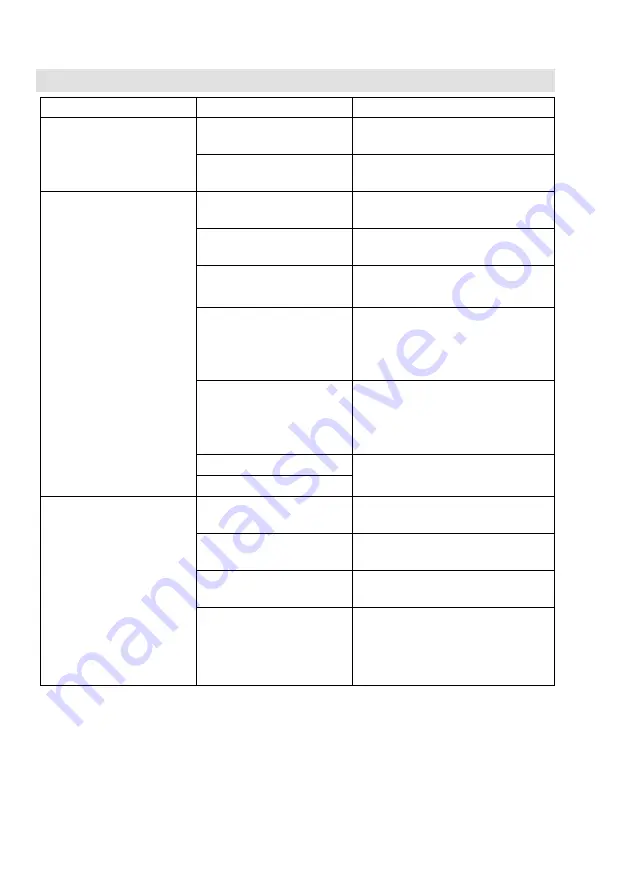
Troubleshooting
Problem Cause Remedy
Insufficient flowrate
The equipment is not
completely open.
Completely open the equipment
The sealing plugs have not
been removed.
Remove the equipment. Take off the
sealing plugs. Mount the equipment.
Fluid escapes (equipment is
leaking).
The end connections are not
tight.
Insulate the connections.
A gasket on the body is
defective.
Replace the equipment with a new one.
Leakage occurs at the stem,
the bellows is damaged.
Re-tighten the stuffing box packing.
Replace the equipment with a new one.
The body has been damaged
by corrosion or erosion.
Check the resistance of the material for
the fluid used.
Use a device made from a material that
is suitable for the fluid used.
The equipment has been
damaged by frost.
Replace the equipment with a new one.
When shutting down the installation
make sure that all lines and the
equipment are completely drained.
The plug or seat is damaged.
Replace the equipment with a new one.
The seat is leaking.
Excessive force is needed to
turn the handwheel.
The locking screw has been
tightened.
Loosen the locking screw.
The position of the stroke
limiter is fixed by a locknut.
Loosen the locknut of the stroke limiter.
The stem is insufficiently
lubricated.
Apply lubricant to the stem.
Limit stop has been reached.
You can only turn the handwheel up to
the stop.
Turn the handwheel into the other
direction.
If faults occur that are not listed above or cannot
be corrected, please contact our Technical
Service or authorized agency in your country.
16