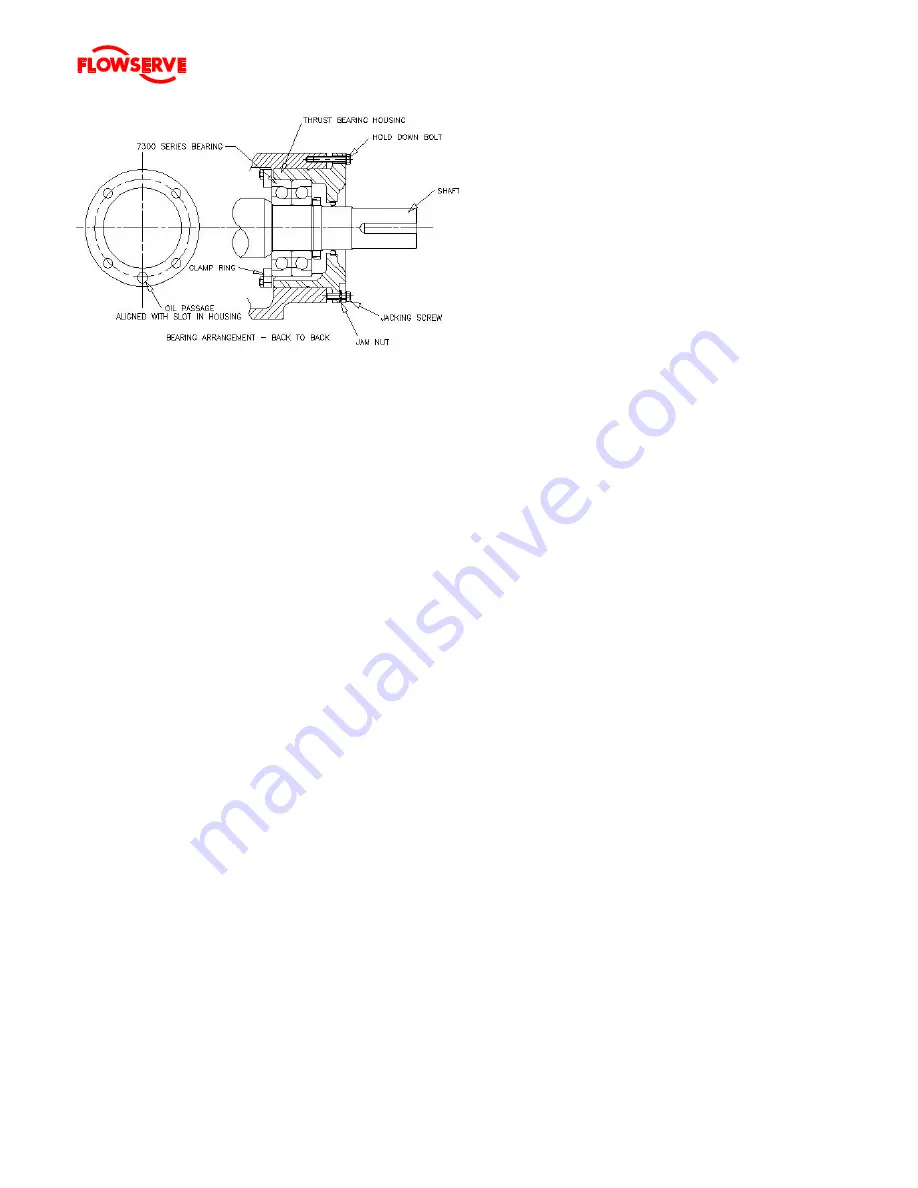
FRBH, FRBHX AND FRBHS USER INSTRUCTIONS ENGLISH 71569178 20-08
Page 48 of 60
Flowserve.com
®
If the coupling has limited axial adjustment capability,
the pump and driver must be uncoupled prior to
adjusting the clearance in order to permit free
movement.
a) Loosen the two set screws retaining the deflector
[2540] and check that the deflector is free to move
axially on the shaft.
b) Loosen the thrust bearing housing jam nuts and
back off the three jacking screws at least 1.5 mm
(0.060 inch).
c) Move the rotor towards the wear plate [1915] by
tightening the three hold-down capscrews evenly
and uniformly until the impeller [2200] just touches
the wear plate. This can be best established by
rotating the shaft and stopping the forward motion
at the first sign of rubbing. If the shaft cannot be
rotated, back off the bearing housing with the
jacking screws until a just detectable rub is
obtained. Check that the gap between the two
machined faces of the thrust bearing housing
[3230] and the bearing frame [3130] are parallel
within 0.08 mm (0.003 in.). Adjust the jack screws
and hold down capscrews as required to achieve
this parallelism. When the impeller [2200] just
touches the wear plate [1915] and the thrust
bearing housing [3230] is parallel to the bearing
cover [3130] the axial clearance between the
impeller and wear plate is zero.
6.11.1.1 Option1
a) Place a dial indicator, set to end of pump shaft
[2110] or on housing [3230] face.
b) Set indicator reading to zero (0).
c) Note required impeller clearance.
6.11.1.2 Option 2
a) Measure and record the axial gap between the
thrust bearing housing flange and bearing frame
end face. Determine the required impeller axial
running clearance from Section I and add this to
the above measurement to establish the required
gap setting.
6.11.1.3
a) Loosen the thrust bearing housing hold down
capscrews slightly and tighten the jack screws.
Until the required dial indicator reading (6.11.1.1)
or housing gap reading (6.11.1.2) is achieved.
b) Alternately and gradually tighten the hold down
capscrews and jack screws until the required gap
setting is achieved at each hold down capscrew
location. Note that the gap at each jack screw will
be slightly larger as a result of minor elastic
distortion of the thrust bearing housing flange
caused by the high pre-load forces. The gap
setting at any set of screws must be the same
within 0.08 mm (0.003 in.). Careful attention to
this procedure will help ensure long thrust bearing
life.
c) While preventing the jack screws from rotating,
tighten the jam nuts to lock them in position.
d) Adjust the axial position of the deflector [2540] so
that it is clear of the line bearing cover [3260] by
approximately 0.75mm [0.03 in.) and tighten the
setscrews firmly. Excessive tightening may mar
the shaft.
e) Manually rotate the shaft to ensure that there is no
rubbing or binding.
f) On belt driven units, adjust the pump or driver
sheave to maintain belt alignment. (Refer to
Section 4.5.2.2).
g) Check the alignment on direct driven units (refer
to Section 4) and reassemble the coupling
components.
h) Replace any safety guards that may have been
removed.
6.11.2
FRBHS Units
End Clearance adjustment is performed in a similar
manner to the FRBH pump except that impeller
clearance is set from the back. Instead of adjusting
the impeller from the wearplate it is necessary to set it
from the stuffing box head [4100].