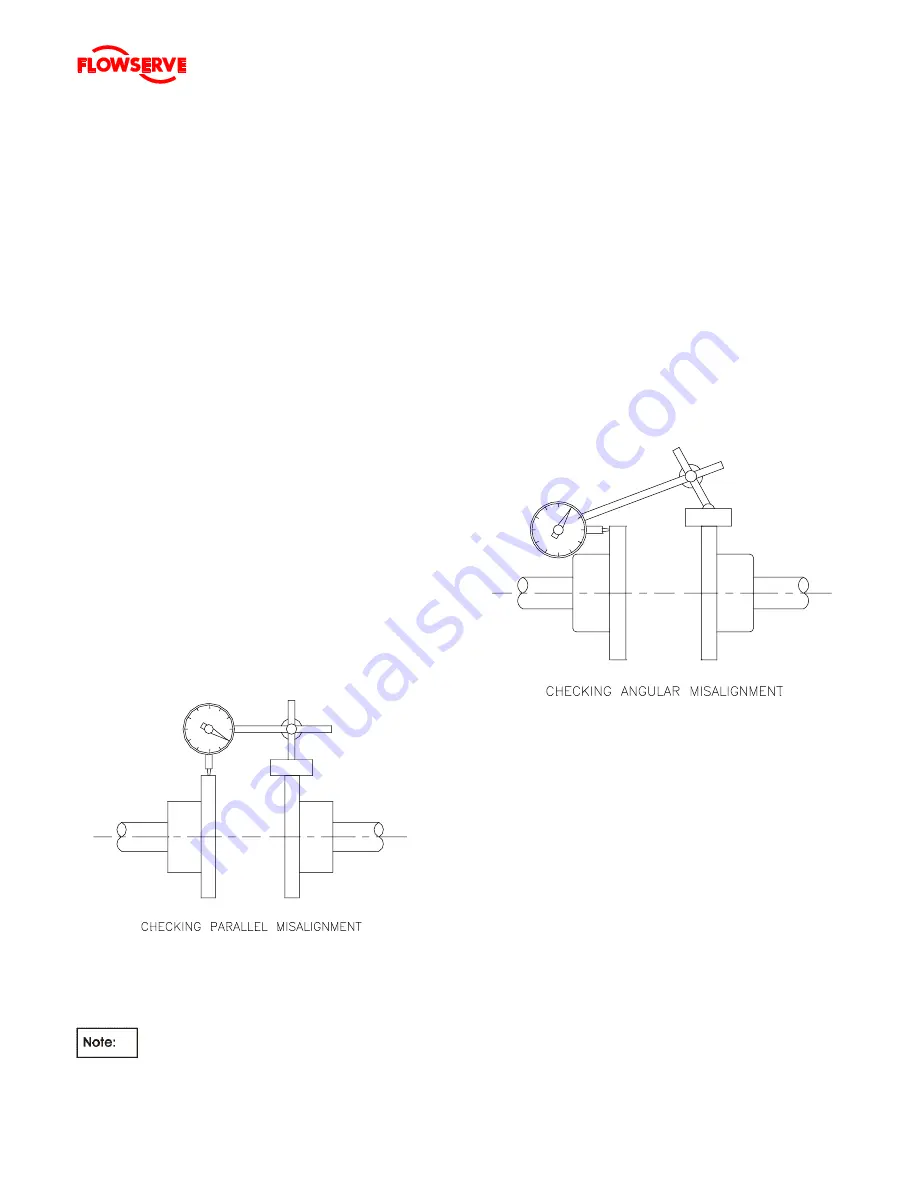
FRBH, FRBHX AND FRBHS USER INSTRUCTIONS ENGLISH 71569178 20-08
Page 26 of 60
Flowserve.com
®
run the motor to establish the rotor magnetic center.
Consult the manufacturer's instruction manual for
details.
The purpose of the alignment procedure is to ensure
that the pump and driver shafts are in parallel and
angular alignment under the normal operating
conditions of load and temperature.
When the pump coupling and driver are assembled
at the factory, the units are aligned prior to shipment.
However, baseplates can be sprung or distorted
during shipment or installation and the alignment
must be checked before the unit is put in service. The
coupling spacer must be removed to make this
check.
For pumps and drivers that operate at different
temperatures compensation must be made at the initial
alignment stage (when the units are at the same
temperature) to allow for thermal expansion during
operation. Consult the instruction manual supplied with
the driver for the manufacturer's recommendations.
Shaft alignment is greatly simplified by the use of a dial
indicator, or with extension rods and a magnetic base.
Before taking readings, ensure that the pump and driver
mounting bolts are secure, and that the thrust bearing
housing is properly aligned in the bearing frame or
cartridge. (See Section VII- Maintenance).
4.5.3
Parallel Alignment:
Mount the magnetic base on the pump half coupling
hub, either the face or O.D. as shown in the sketch.
Place the dial indicator button on the outside diameter
of the driver half coupling hub.
T
he length of extension rods should be kept at
a minimum to reduce deflection.
Rotate the pump shaft and record the dial reading at the
top, bottom and each side. Correct the parallel
alignment by adding or removing shims under the driver
and/or moving the driver horizontally. Repeat this
procedure until the maximum total indicator reading
(T.I.R.) is within 0.08 mm (0.003 inch.)
4.5.4
Angular Alignment:
Mount the magnetic base mounted on the pump half
coupling hub, either face or O.D. as shown. Move the
dial indicator button to indicate on the face of the driver
half coupling hub as close to the outside diameter as
possible. When convenient the indicator can be placed
on the inside face to keep spans short. Turn both shafts
360
and record the dial readings at 90
intervals.
Adjust the shims under the motor as required and
repeat the procedure until the angular alignment is
within 0.0005 mm (T.I.R.) per mm (0.0005 inch per inch)
of maximum hub diameter.
Repeat the checks on parallel and angular alignment,
ensuring the mounting bolts are secure, until the unit is
properly aligned. Note that correction in one direction
may affect the alignment in another direction. Re-check
the gap between the coupling hubs.
If any difficulty is encountered in achieving the
recommended alignment tolerances, the run-out of the
pump and driver shafts and each coupling hub diameter
and face should be checked. Occasionally, due to
practical and unavoidable manufacturing tolerance
build-up associate with the pump, coupling and driver, it
may be necessary to match up the two coupling hubs in
the most advantageous relative angular position in order
to achieve an acceptable alignment.
Do not install the coupling spacer or sleeve until
grouting is complete and cured and the alignment is re-
checked.
When the electric motor has sleeve bearings it is
necessary to ensure that the motor is aligned to run