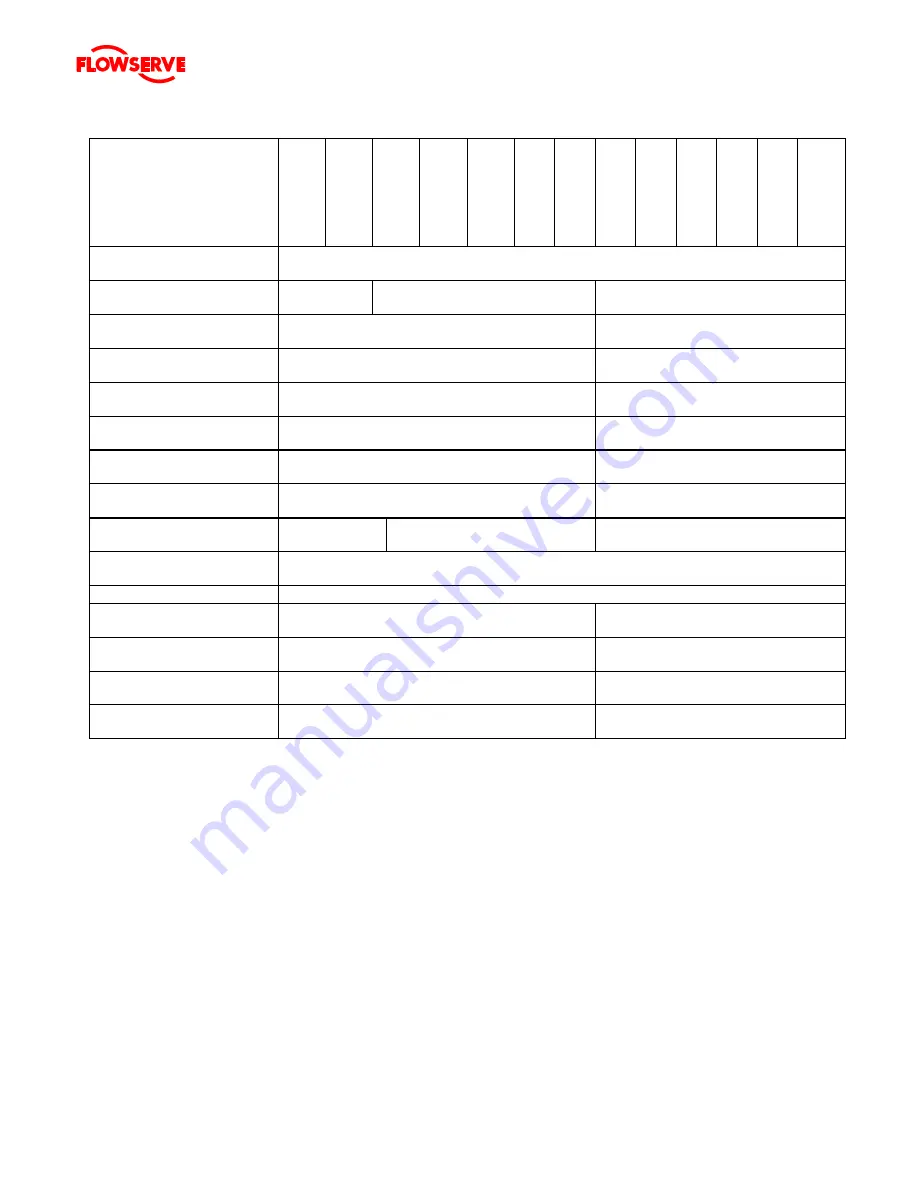
FRBH, FRBHX AND FRBHS USER INSTRUCTIONS ENGLISH 71569178 20-08
Page 16 of 60
Flowserve.com
®
3.5.2
FRAMES 1 & 2 - FRAME DETAILS
ENGINEERING
DATA
2F
R
B
H
12
1
3F
R
B
H
12
1
3F
R
B
H
10
1
4F
R
B
H
11
1
6F
R
B
H
11
1
3F
R
B
H
14
1
4F
R
B
H
14
1
6F
R
B
H
14
2
8F
R
B
H
15
2
3F
R
B
H
18
2
4F
R
B
H
18
2
8F
R
B
H
18
2
10
F
R
B
H
1
8
2
SHAFT AND BEARING
DATA
DIA. AT IMPELLER mm
(in.)
28.58
(1.125)
34.93
(1.375)
50.80
(2.000)
DIA. UNDER SLEEVE mm
(in.)
41.27
(1.625)
66.68
(2.625)
DIA. BETWEEN mm
BEARINGS (in.)
63.5
(2.50)
91.9
(3.62)
DIA. AT COUPLING mm
(in.)
41.27
(1.625)
63.50
(2.500)
LINE BEARING
6311
6316
THRUST BEARING
7309 BUA
7314 BUA
BEARING SPAN mm
(in.)
193.8
(7.63)
279.4
(11.00)
NOM. IMPELLER mm
OVERHANG (in.)
207.8
(8.18)
204.7
(8.06)
245.4
(9.66)
B10 BEARING LIFE
MINIMUM 3 YEARS
BEARING SEALS
THRUST BEARING LIP
SEAL
C / R 16246 NAT. 473010
C / R 24982 NAT. 417449
LINE BEARING LIP SEAL
C / R 19832 NAT. 472492
NAT. 417350
THRUST BEARING
O-RING
#249
#263
LINE BEARING O-RING
#246
#259