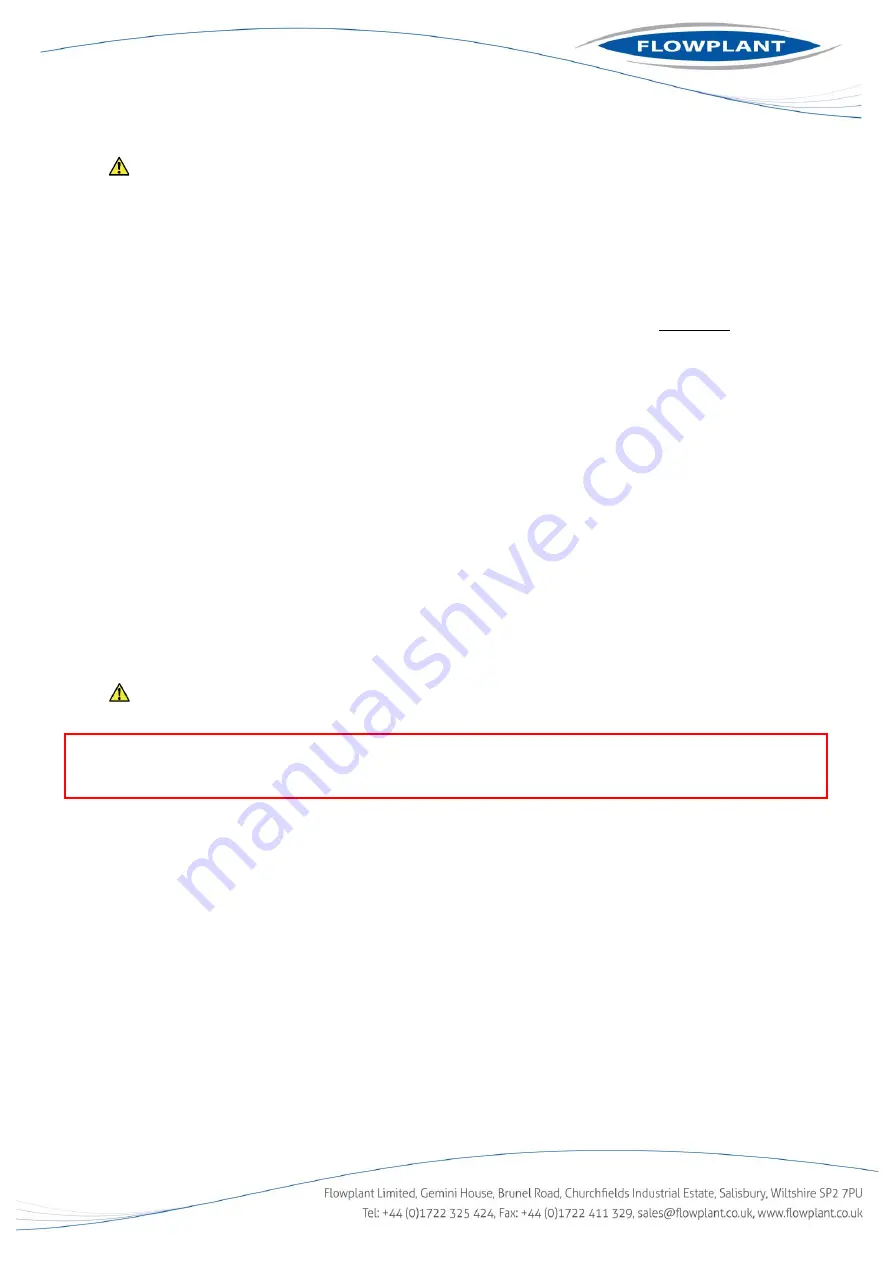
28
4.7. Rapid Shutdown
Should any unforeseen circumstances arise, including any signs of a leak, the jetting
operation should be terminated immediately, the equipment shut down and the relevant
managers informed.
4.8. Automatic Shutdown
The engine will shut down automatically if the monitoring and control system detects a
malfunction. Possible reasons for an automatic shutdown are detailed in Section 6 - Fault
Finding.
4.9. Harben Jump Jet
The Harben Jump Jet system is a unique and exceptionally effective addition to the Harben
high pressure pump which increases the effective duct cleaning distance up to and often
beyond 300m. When required the operator can switch on the Jump Jet to create a cyclic
vibration in the jetting hose. The vibration travels along the entire length of the hose reducing
friction between itself and the duct wall and allowing the de-silting nozzle to continue moving
into the duct, cleaning as it goes.
Critically the Jump Jet allows ducts to be de-silted with pressures as low as 140 bar and only
40 l/min meaning that even with fibre optic cable in-situ there is negligible risk of causing any
damage.
To operate the jump jet, open the jump jet valve on the control panel of the unit.
4.10. Hose reel winding and unwinding
The high-pressure hose is manually unwound and hydraulically wound by an OMR315
hydraulic motor, which is driven by a gear pump from the engine P.T.O.
The motor is fitted to the hub of the hose reel. The motor speed and direction is controlled via
a manually actuated spool valve. (018-
005 “Hydraulic Directional Control Valve” CV1185 c/w
90- 100psi relief and flow control)
The hose reel motor speed can be adjusted up and down by a flow control knob. Pushing the
lever inwards towards the pump set will wind the hose reel in.
NOTE: Operating the machine with the Jump Jet system turned off can increase the water pressure at the de-
silter nozzle by up to 100%. Only do this when you know there is no risk of damage to in-situ fibre optic cables
.
Summary of Contents for 003301
Page 11: ...11 Hydraulic Diverter Valve 069 581 ...
Page 12: ...12 Hawk Safety Relief Valve 035 401 ...
Page 13: ...13 Speck Unloader Valve UL221 035 185 ...
Page 25: ...25 Fig 4 Operating with the Radio Remote ...
Page 43: ...43 9 Circuit and Wiring Diagrams ...
Page 45: ...45 ...
Page 46: ...46 ...
Page 59: ...59 ...
Page 61: ...61 ...
Page 62: ...62 11 Service Documents 11 1 Service Checklist ...
Page 63: ...63 11 2 Service Logbook ...
Page 64: ...64 ...