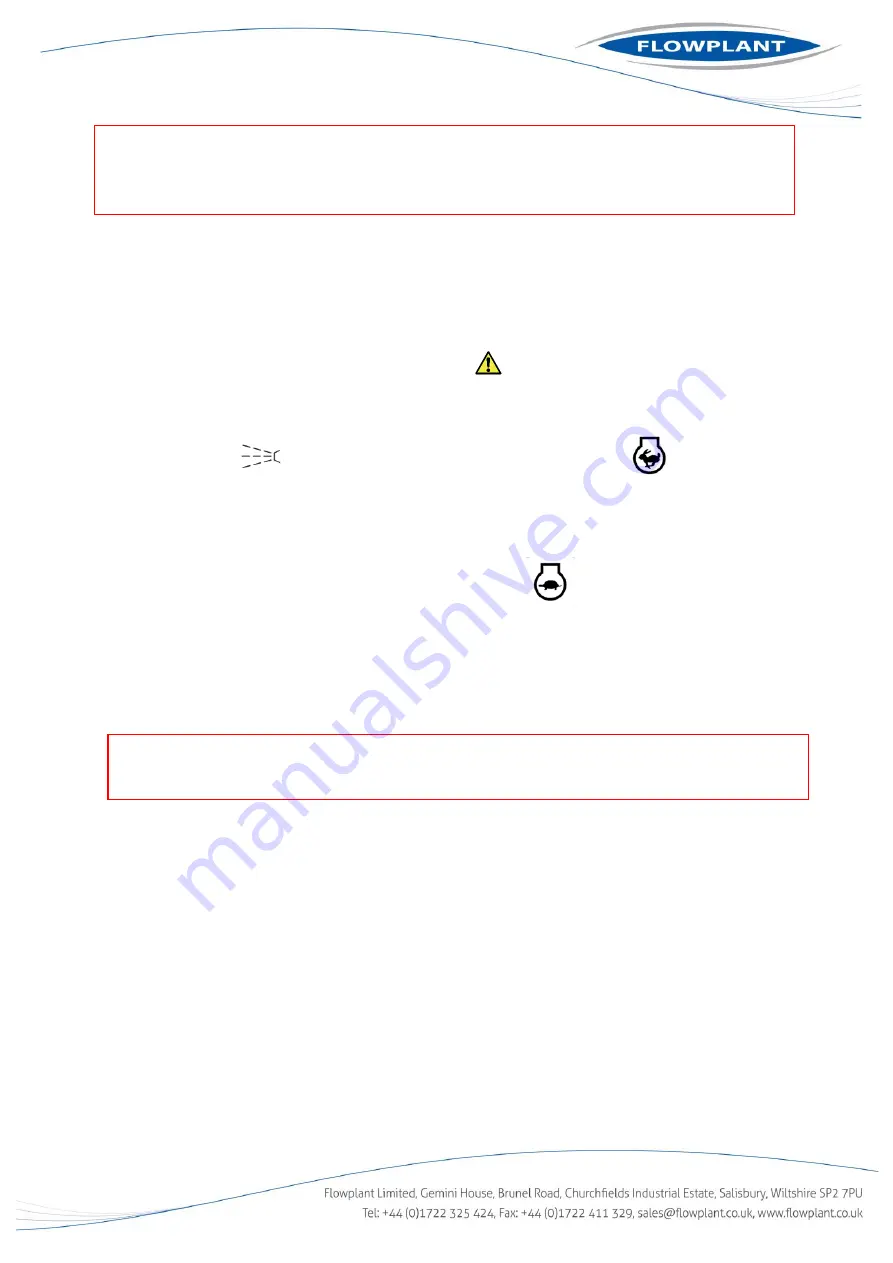
24
4.5.3. Checking the operating pressure with a gun fitted
1. Fit the gun (with the appropriately sized H.V. (pencil) or Fan Jet), to the high-pressure
hose.
2. Ensure the gun is held firmly in the hand.
3. Start the engine
4. Press the
button to divert the water to the gun. Use the
button to raise
the engine speed.
5. Pull the gun trigger and observe the pressure gauge mounted on the instrument panel,
note the pressure reading (See fig. 3). Press the
button until engine tick over
speed is reached, then press the
‘water off’ button and return the unit to the idle position
Note: If the pressure is significantly lower than expected, turn the unit off and replace
the worn nozzle in the gun with a new one!
Do not exceed the maximum operating pressure of 200Bar by fitting a smaller nozzle than is
recommended, as this will cause the Pressure relief valve & or Safety relief valve to dump the
excess pressure. The maximum engine speed is mechanically governed to 3150 rpm.
When using the RCU the operator is required to remove the key form the Local/Remote
selection whenever the trailer/van pack is unattended
Summary of Contents for 003301
Page 11: ...11 Hydraulic Diverter Valve 069 581 ...
Page 12: ...12 Hawk Safety Relief Valve 035 401 ...
Page 13: ...13 Speck Unloader Valve UL221 035 185 ...
Page 25: ...25 Fig 4 Operating with the Radio Remote ...
Page 43: ...43 9 Circuit and Wiring Diagrams ...
Page 45: ...45 ...
Page 46: ...46 ...
Page 59: ...59 ...
Page 61: ...61 ...
Page 62: ...62 11 Service Documents 11 1 Service Checklist ...
Page 63: ...63 11 2 Service Logbook ...
Page 64: ...64 ...