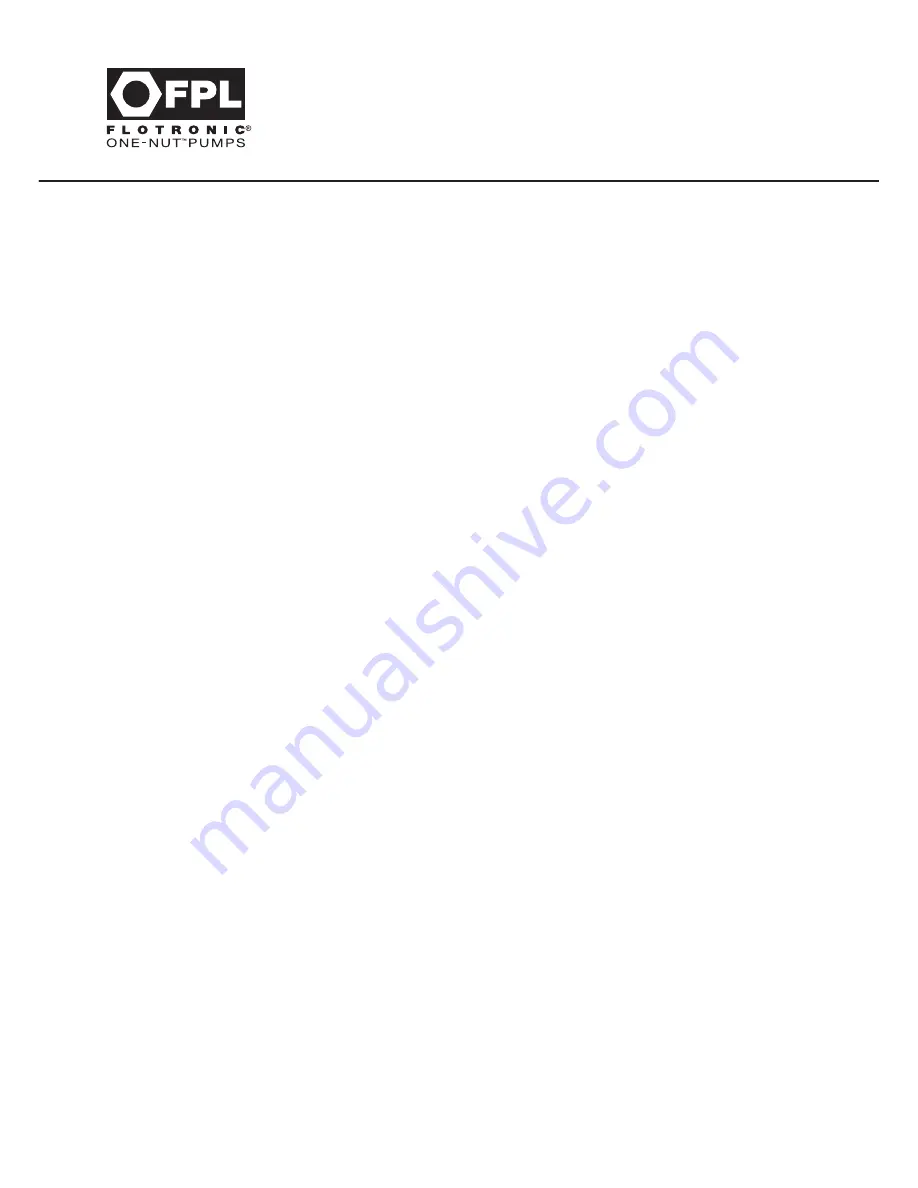
55
Rupture Protection Barriers
& Alarm Systems
Attach first primary diaphragm on opposite side, followed by separator disc, retainer, seal, separator
ring and finally, backing diaphragm (PTFE face inward). Tighten diaphragms by hand to achieve
positive seal. Do not use sharp edged tools. You cannot over-tighten diaphragms, a positive seal can
be achieved by hand tightening only.
Pumps with 12” and 14” Diameter diaphragms
Place the entire twin-pack assembly into the pump body and then lay the complete assembly, with
diaphragms, underneath onto tool No: B0009A.
Tighten down the fixing bars onto the slot in the body where the manifold normally fits. The diaphragms
will compress enough for you to now attach the opposite side diaphragms onto the top.
Complete the entire diaphragm tightening procedure on both sides and then insert the manifolds and
place the whole body/manifold/diaphragm assembly into the pump casing.
TIPS
1. After reassembly always ensure the diaphragm/thrust tube assembly is centralised in the pump body.
2. To rotate separation rings for a key-way alignment, pull away from wet diaphragm, thus transferring
friction forces from rubber to PTFE.
3. To remove last diaphragm from thrust tube, wrap a 12” long strip of 1” wide medium emery cloth
around the PTFE thrust tube mid-way along (to avoid divider seal region) with abrasive against the
PTFE. Grip in place tightly, using a jubilee clip with it’s screw knuckle on the lapped area of the
emery (for protection). Assemble the jubilee clip into a vice so that the screw knuckle acts as a stop
and so limits the necessary tightening of the vice.
Note:
This special tooling assembly is only necessary because of the special nature of environmentally
protected air driven double diaphragm pump. Normal 2 diaphragm Flotronic Pumps do not
require any special tooling to fit diaphragms.
Summary of Contents for F 500 series
Page 15: ...7 Your Notes...
Page 30: ......
Page 35: ......
Page 36: ...30 F Series Good Food Style Pump Section 13 F Series Good Food Style Pump...
Page 38: ......
Page 40: ...35 F Series Slim Style Metallic Pumps Section 14 F Series Slim Style Metallic Pumps...
Page 43: ......
Page 44: ...40 F Series K Style Chemflo All PTFE Section 15 F Series K Style Chemflo All PTFE...
Page 46: ......
Page 48: ...45 Air Valves Section 16 Air Valves...
Page 50: ...47 Pulsation Dampers Section 17 Pulsation Dampers...
Page 54: ...51 Your Notes...
Page 59: ...56 Your Notes...
Page 61: ......
Page 62: ...60 Count Stop Pumps All Series Section 19 Count Stop Pumps All Series...
Page 65: ...63 Your Notes...
Page 67: ...65 Your Notes...
Page 68: ...66 Your Notes...