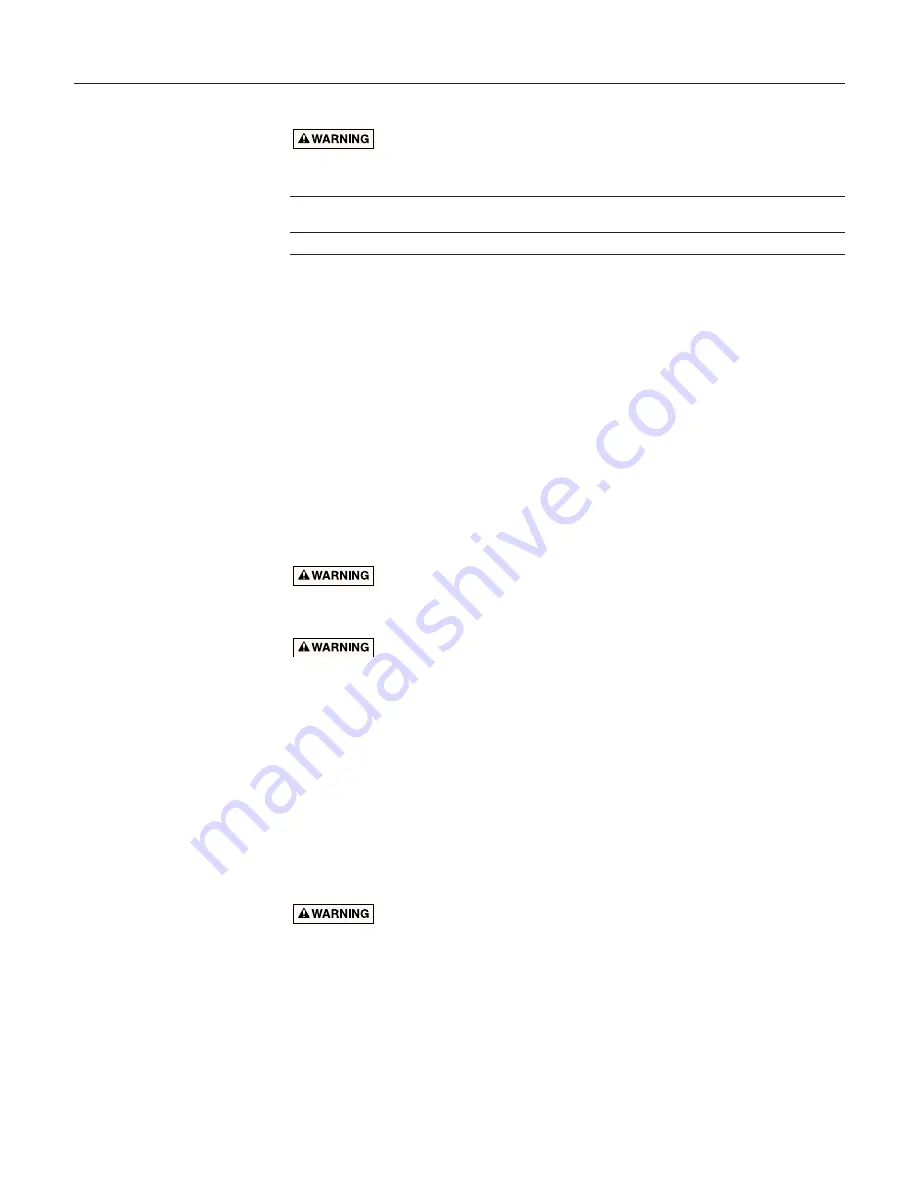
Electrical / Operation / Service
4
Risk of electrical shock and fire. Be sure that power supply informa-
tion (Voltage/ Hertz/Phase) on pump motor nameplate matches incoming power
supply exactly. Install pump according to all electrical codes that apply.
FPSE
Fuse or Circuit
Dual Element Time
Model
H.P.
Voltage
Breaker Amps
Delay Fuse Amps
4202A
1/2
220
20
10
OPERATION
NOTICE: Do not allow pump to run in a dry sump. It will void the warranty and may
damage the pump.
An automatic overload protector in the motor will protect motor from burning out
due to overheating/overloading. When motor cools down, overload protector will
automatically reset and start motor.
If overload trips frequently, check for cause. It could be a stuck impeller, wrong/low
voltage, or electrical failure in motor. If an electrical failure in the motor is suspected,
have it serviced by a competent repairman.
Pump is permanently lubricated. No oiling or greasing is required.
SERVICE
Pump is permanently lubricated. No oiling or greasing is required in normal service.
Hazardous voltage. Can shock, burn, or cause death. Before servicing
pump, disconnect electrical power to pump and control switch.
After removing basin cover and necessary discharge piping, lift pump out of basin.
Risk of electrical shock. Can burn or kill. Do not lift pump by power
cord. (See “Cord Lift Warning”).
Place pump in an area where it can be cleaned thoroughly. Remove all scale and
deposits on pump.
Submerge pump in disinfectant (chlorox or chlorine) for at least one hour before dis-
assembling pump.
The pump motor housing contains a special lubricating oil. Keep oil clean and free
of water at all times.
NOTICE: Whenever motor housing is being removed for service, remove oil and
replace with new oil at reassembly. Use only oil listed in parts list (Part No. U197-
8A). When filling with new oil, DO NOT overfill. To allow room for expansion, oil
level with cold motor should be about 6 mm (1/4") above top of motor assembly.
Impeller, Seal, and Capacitor Replacement
Risk of electrical shock. Disconnect electrical power from pump
before doing any service work on it!
Numbers refer to assembly drawing, Page 7.
Disassembly
Step 1. Unscrew hex-head cap screws (Key No. 6), remove motor assembly from
volute and set it on its side in a clean area.
Step 2. Remove oil fill plug (Key No. 2). Turn pump upside down to drain oil.
Step 3. Hold impeller (Key No. 10); remove impeller nut and washer (Key Nos. 11
and 12).
Step 4. Unscrew impeller (turn counter-clockwise) for cleaning.