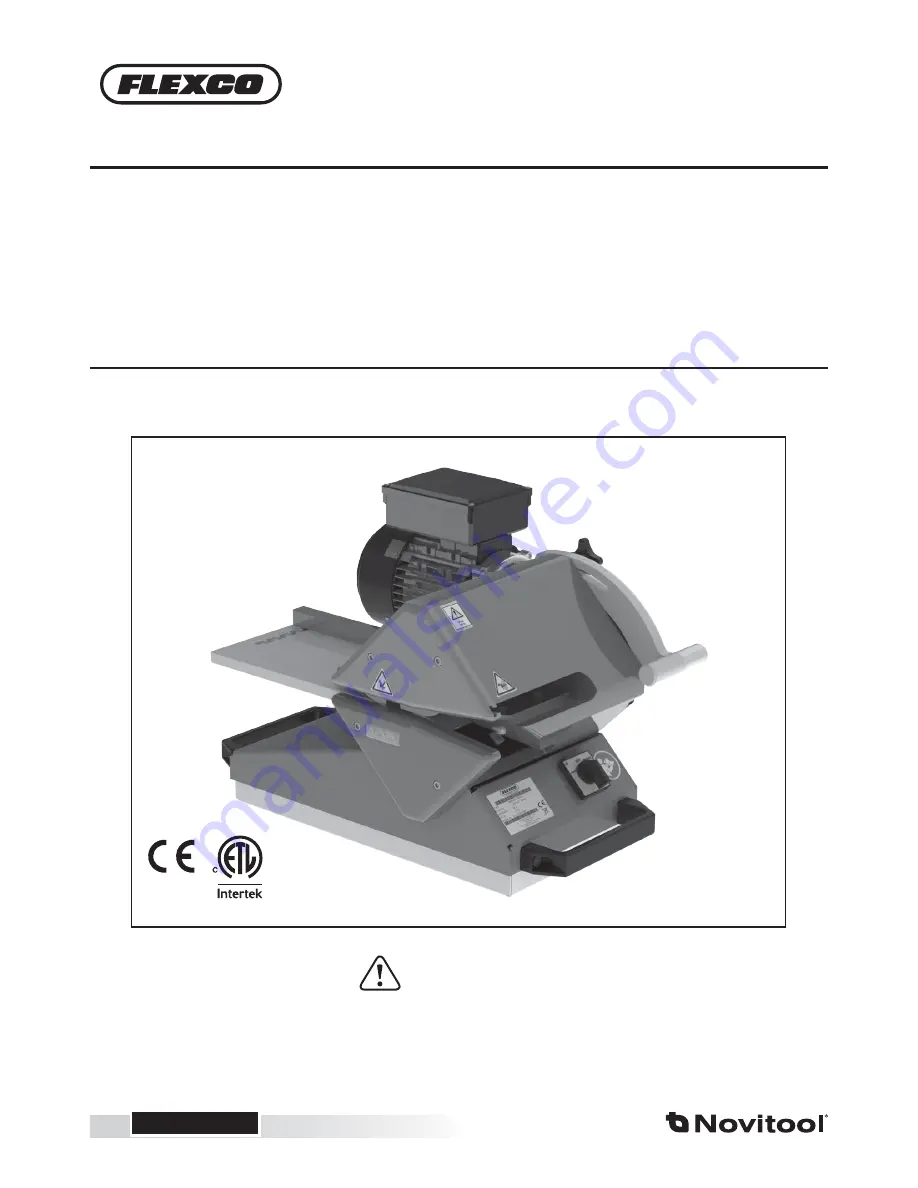
LISTED
CM
Cert. to CSA
Std. C22.2 No. 68
5011455
www.flexco.com
www.flexco.com
Separate between the plies of a conveyor belt.
IMPROPER OR UNSAFE use of this tool can result in serious bodily injury! This manual contains important information
about product function and safety. Please read and understand this manual BEFORE operating the tool. Please keep this
manual available for other users and owners before they use the tool. This manual should be stored in a safe place.
WARNING
Novitool
®
Ply 130
™
Separator
Workbench & Optional Workshop Cart
Safety and Operation Manual
Summary of Contents for Novitool Ply 130
Page 35: ...35 H Electrical Schematics 08802...
Page 36: ...www flexco com 36 www flexco com Electrical Schematics 08803 08...
Page 37: ...37 Electrical Schematics 08809 12 08834...
Page 38: ...www flexco com 38 www flexco com Electrical Schematics 08800 08832 33...
Page 39: ...39 Electrical Schematics 08801...
Page 42: ...www flexco com 42 www flexco com K Declarations...
Page 43: ......