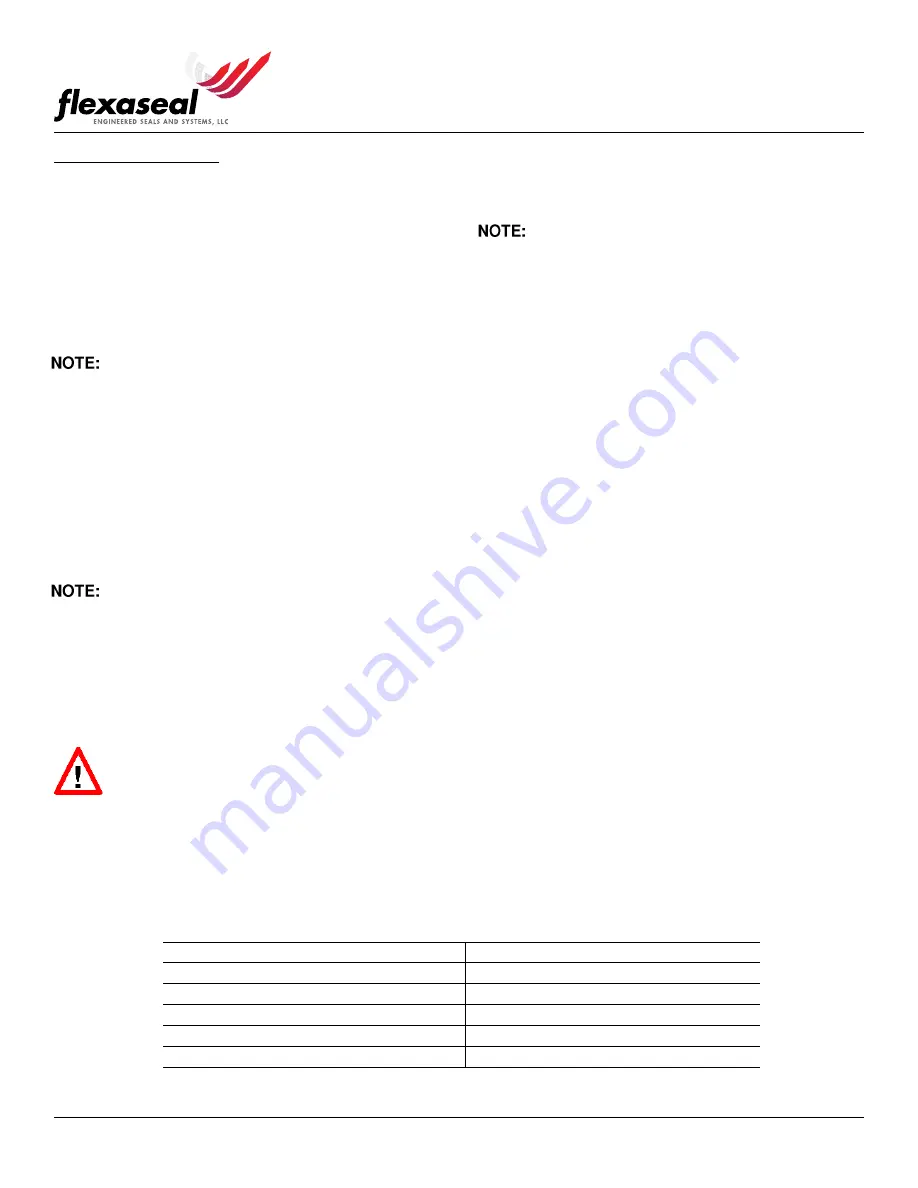
Installation, Operation, & Maintenance Guide
Style 78HT
SEAL INSTALLATION
Style 78HT High Temperature Dual/Tandem Rotating
Welded Metal Bellows Cartridge Seals require a
similar installation procedure as other Flexaseal
cartridge seals with the addition of a few minor steps.
Ensure alignment verification of equipment has been
completed prior to starting the installation procedure.
Reveiw engineering prints for special notes and/or
instructions.
•
It is essential to use a suitable lubricant
when installing a seal, as different
lubricants will work better with different
elastomers.
1
. Disassemble the pump until the seal chamber
and shaft are accessible.
2
. Remove the seal from its packaging and
inspect for damage to any components and
seal faces.
With the exception of the sleeve packing,
high-temperature cartridge seals are
shipped from Flexaseal fully assembled and
should not be disassembled without cause.
If a seal appears damaged prior to
installation, contact a Flexaseal
representative.
Grease, scratches, or nicks on the seal
faces may cause leakage.
3
. Ensure the shaft and seal housing have been
properly cleaned as described in the
preparation section.
4
. Remove the drive collar cap screws and collar
from the seal assembly.
The seal will be shipped from Flexaseal
with the drive collar cap screws finger-tight.
5
. Lightly lubricate the sleeve packing with a
suitable and compatible lubricant. Slide the
drive collar and the sleeve packing along the
shaft ahead of the seal. Ensure the wedge and
drive collar are oriented properly (
6
. Gently slide the seal on the shaft with the gland
gasket facing, but clear of the seal chamber.
7
. Reassemble the pump as described by the
pump OEM.
8
. Bolt the gland to the seal chamber using the
Legacy Method (Star Pattern) according to
standard torque-tension specifications for bolts
and studs. Be sure not to overtighten the gland
bolts as this may distort the gland and internal
components resulting in seal leakage.
9
. Slide the sleeve packing into position under the
outboard edge of the sleeve.
10
. Tighten drive collar cap screws evenly to
achieve the specified 0.050 in. gap (
11
. Alternately tighten the provided set screws to
the specified torque value according to the
table below.
12
. Remove the setting clips from the seal. Save
these for future use in seal removal or impeller
adjustment (
Cup Point Set Screw Torque Specifications
Screw Size
Alloy Steel
Stainless
Screw Size
Alloy Steel
Stainless
#10
36 in.-lbs.
26 in.-lbs.
M4
2.0 N-m
1.5 N-m
1/4
87 in.-lbs.
70 in.-lbs.
M6
7.9 N-m
6.1 N-m
5/16
165 in.-lbs.
130 in.-lbs.
M8
19.6 N-m
15.4 N-m
3/8
290 in.-lbs.
230 in.-lbs.
M10
37.0 N-m
29.5 N-m
1/2
620 in.-lbs.
500 in.-lbs.
M12
60.3 N-m
48.3 N-m
Page 4 of 9