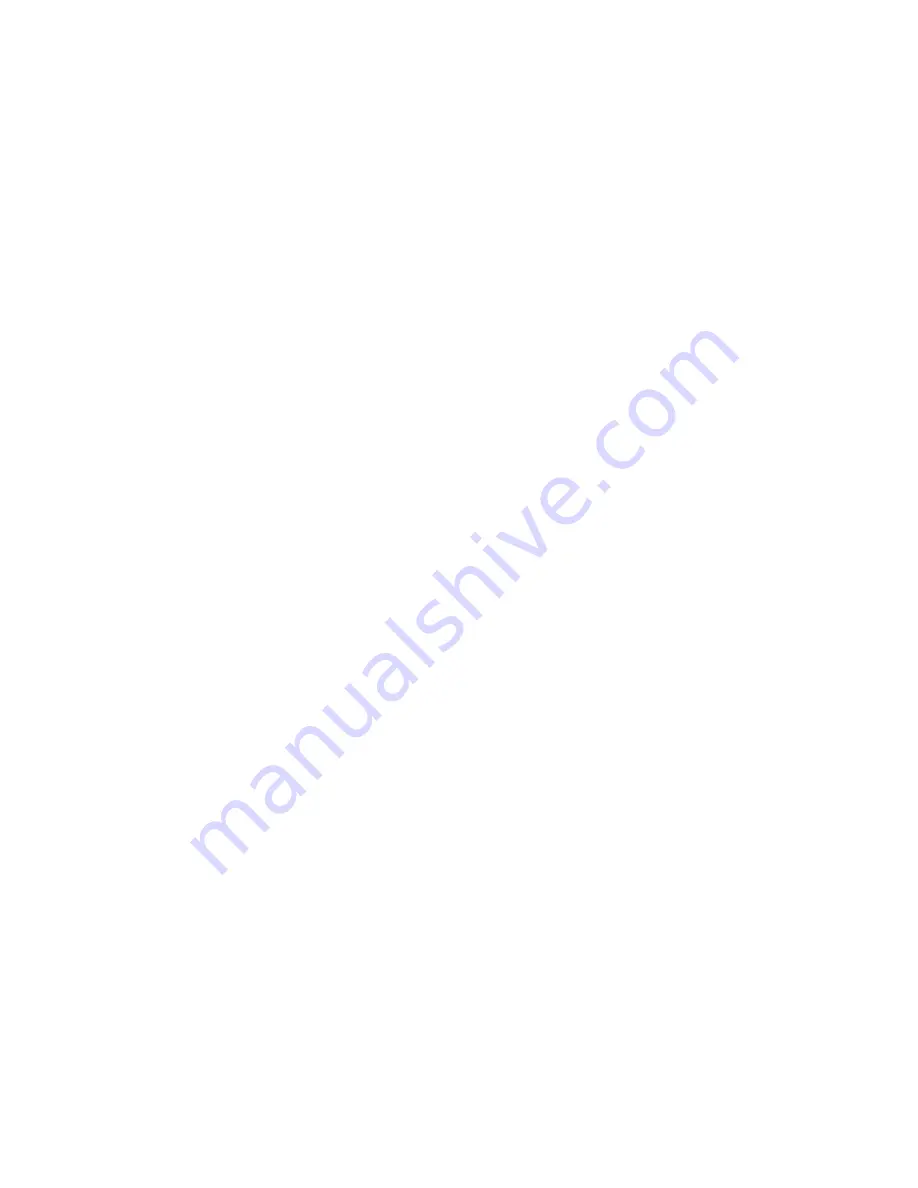
g)
Making the gas connection
The gas connection should be made to the appliance inlet elbow using
rigid 8mm piping.
h)
Lift the firebase in to position and secure the base of the fire opening
with the two screws provided, ensure when fitted that the fire tray sits
level.
i)
Before making the final gas connection, thoroughly purge the gas
supply pipework to remove all foreign matter, otherwise serious damage
may be caused to the gas control valve on the fire.
NOTE :- Failure to correctly purge the pipework will invalidate the
guarantee
2.3
GAS TIGHTNESS AND INLET PRESSURE
a)
Remove the pressure test point screw from the inlet elbow and fit a
manometer.
b)
Turn on the main gas supply and carry out a gas tightness test.
c)
Depress the control knob and turn anti-clockwise to the position marked
ignition / low. Hold in the control knob for a few seconds to purge the
pipe work then press the igniter button. The burner should light,
continue to hold the control knob for a few seconds then turn to the full-
on position.
d)
Check that the gas pressure is
20.0 mbar (+/- 1.0mbar) 8.0 in w.g.(+/-
0.4 in w.g.) for Natural Gas Models
e)
After removing the manometer, ensure that the pressure test point
screw is checked for gas tightness with suitable leak detection
spray or fluid.
11