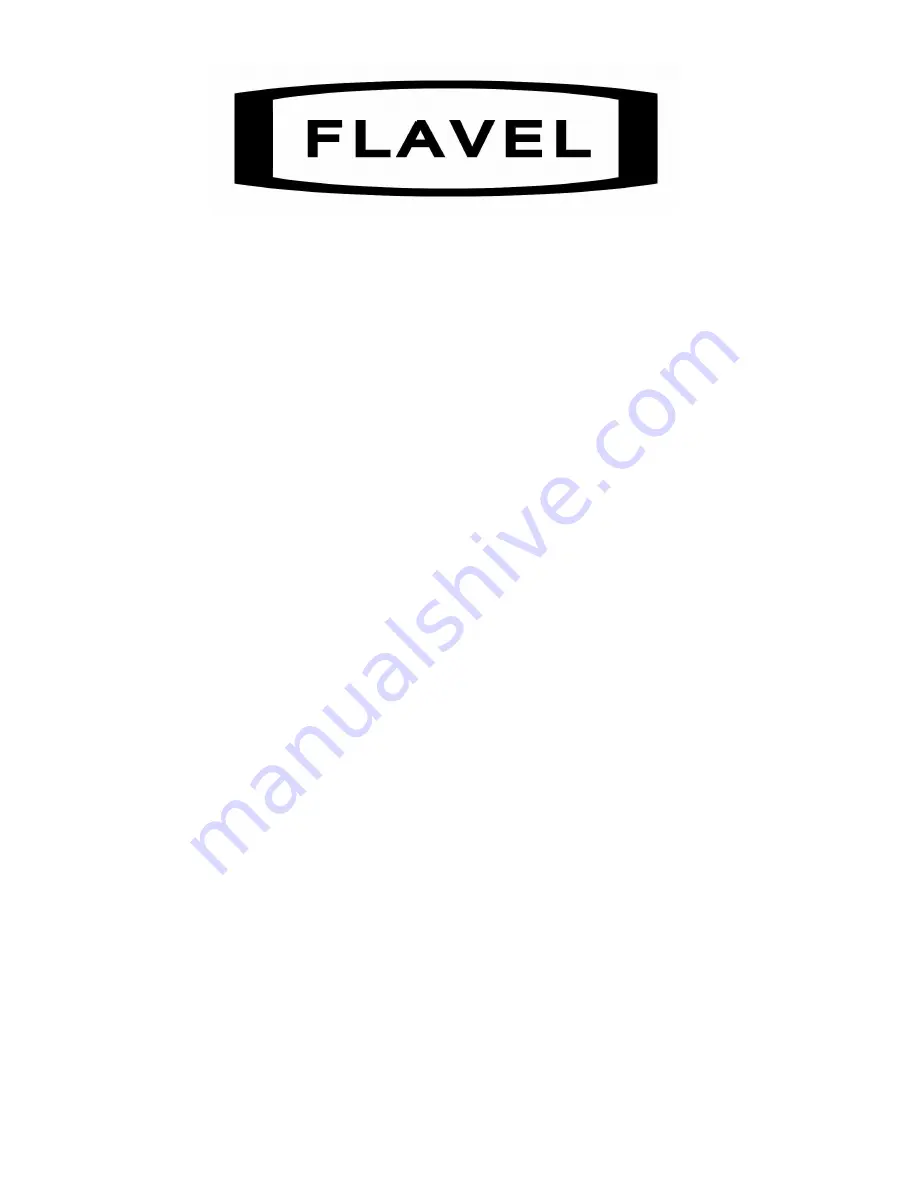
Richmond Plus
INSET LIVE FUEL-EFFECT GAS FIRES
Installation, Maintenance & User Instructions.
Hand these instructions to the user after installation.
Model No’s FOPC**MN, FOPC**SN & FOPC**RN are for use on
Natural Gas (G20) at a supply pressure of 20 mbar in G.B. / I.E.
** denotes variant of trim / fascia where applicable