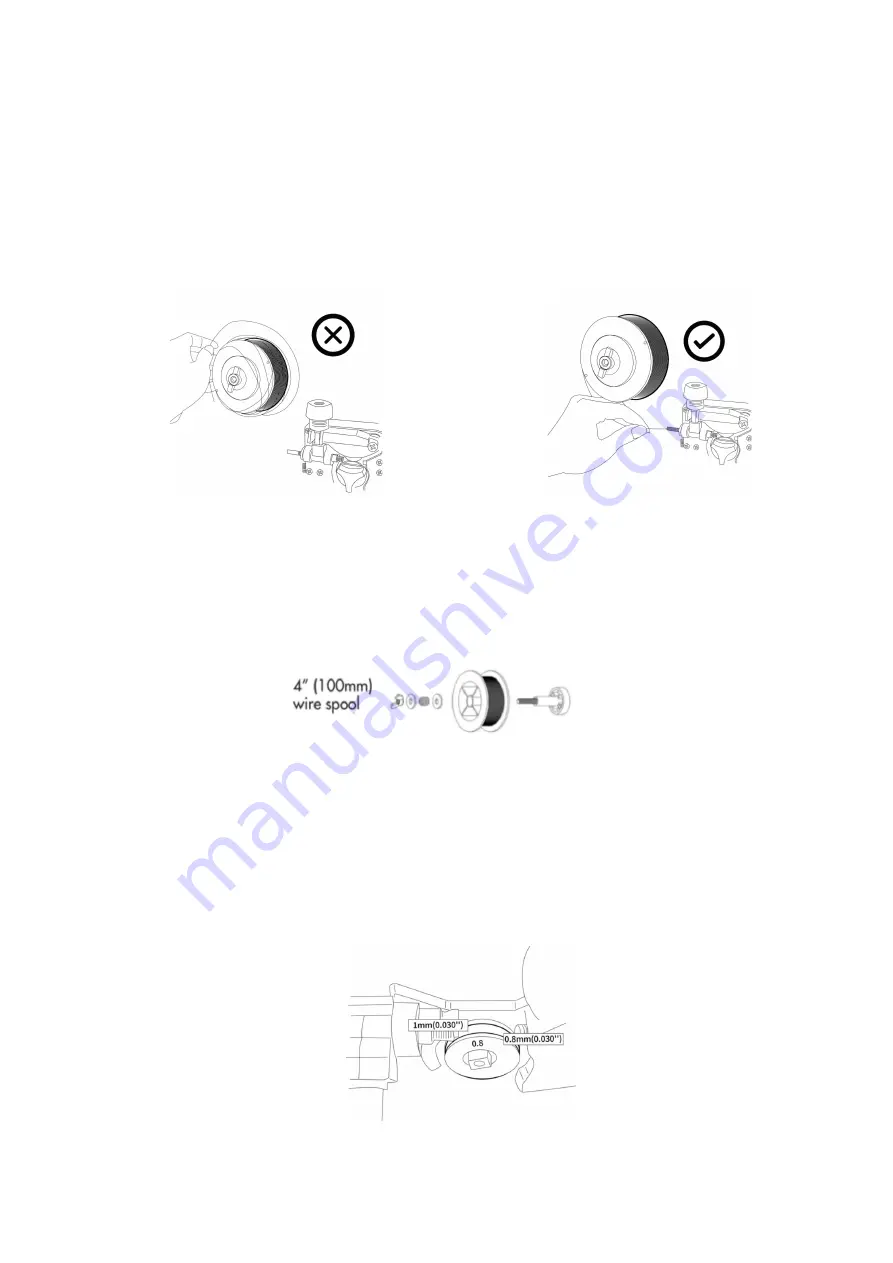
- 6 -
2 Installation instruction
2.1 Welding wire Installation steps:
The wire holder filled with wire installed on the wire feeder. The hole position of the wire plate
should be aligned with the fixed plug on the shaft.
The wire coil should be rotated and loosen the wire, to prevent the wire from loosening, the
new wire disk head is usually inserted into the fixed hole at the edge of the wire. In normal
use, to prevent the bending of the wire to be stuck, please cut this part of wire.
0.030”(0.8mm)/0.040”(1.0mm)diameter
4”(100mm 1kg)wire spool
According to the diameter of the wire, choose different wire feed roller.V roller for stainless
steel and carbon steel. Knurled roller for flux cored wire. Please match diameter notes on the
roller with the welding wire diameter.
Roller size: external diameter
∮
25mm/ internal diameter
∮
7mm/ height 7.5mm
Summary of Contents for FM 155E
Page 1: ...1 Operation Manual FM155E MIG Welding Machine...
Page 9: ...9...