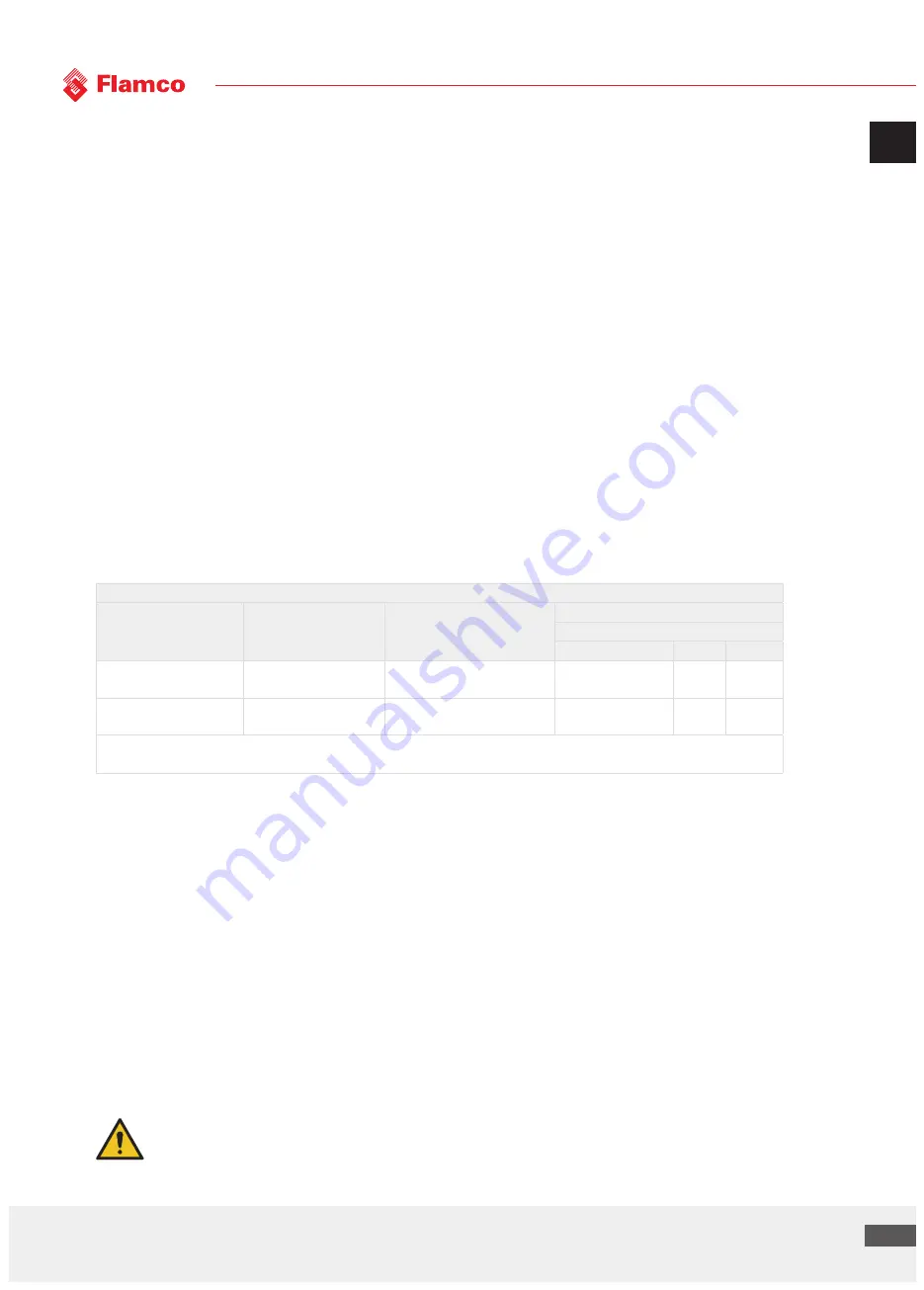
Manual Flamcomat MK-U G4
We reserve the right to change designs and technical specifications of our products.
10
ENG
Electrical hazards:
The protection class of electrically operated components prevents personal injury by electrocution, which can be fatal. The
protection class is usually IP23. The control unit cover, the cover of the pump feed, the threaded cable glands and the valve
connector plugs must be inspected for effectiveness prior to commissioning. The installed pressure and volume sensors are
operated with protective extra-low voltage.
Avoid welding work on additional equipment which is electrically connected to the control unit. Stray welding current or an
improper earth connection could lead to the danger of fire and damage to parts of the unit (e.g. the control unit).
4.15 External forces
Avoid any additional forces (e.g.: forces caused by heat expansion, flow oscillations or dead weights on the flow and return
lines). These can lead to damage / leaks in water-bearing pipework, loss of stability of the appliance and furthermore to
failure connected with substantial material damage and personal injury.
4.16 Inspection prior to commissioning, maintenance and re-inspection
They guarantee operational safety and its observance in line with applicable European regulations, European and
harmonised standards and additional national regulations of the EU member states for this field of application. The required
inspections must be arranged by the owner or operator; an inspection and maintenance log book for scheduling and
traceability of measures taken must be kept.
Tests in line with the German ordinance on operational safety (BetrSichV, June 2015):
Pressure device, Vessel
Category [Appendix II The
Directive 2014/68/EC,
Diagram 2]
Vessel Nominal Volume (l.) Inspection prior to commissioning
[§14]
Inspector
Routine Inspection [§15 (5)]
Timeframe, maximum period [a] / inspector
External
Internal* Strength*
III
400 / 6 bar 5000-10000/
3 bar
Qualified Person (QP)
Not applicable [§15 (6)] 5 / QP
10 / QP
IV
600-3500/
6 and 10 bar
Qualified Person (QP)
Not applicable [§15 (6)] 5 / QP
10 / QP
* [§15 (10)] In the case of internal inspections the visual inspection may be replaced by similar procedures and in the case of strength
tests the static pressure test may be replaced by similar, non-destructive procedures if said tests would not otherwise be possible due
to system design or not significant due to the system mode of operation.
In other Member States of the EC, the required tests for the pressure equipment in line with directive 2014/68/EU as defined
in the national rules must be performed.
4.17 Electrical equipment inspections, routine inspection
Without prejudice to the considerations of the insurer/Operator, it is recommended that the electrical equipment of the
Flamcomat be inspected and documented together with the heating/cooling unit no less than every 18 months (see also DIN
EN 60204-1 2007).
4.18 Maintenance and repairs
These services may only be carried out when the system is shut down or if the expansion automat is not required. The
pressurisation equipment must be taken out of service and guarded against unintentional re-starting until the maintenance
work is finished. Note that the safety circuits and data transmissions made whilst shutting down could trigger the safety
chain or lead to false information. Existing instructions for the heating or cooling unit as a whole must be observed. To stop
hydraulic components, block the relevant sections and drain them using the safe system water drains through the available
drain connections, and relieve the pressure.
Caution:
The maximum system water temperature in conducting components (vessel, casings, hoses, pipelines,
peripheral equipment) may reach 70 °C and, in the case of improper operation, may exceed that. This presents a
danger of burns and/or scalding.