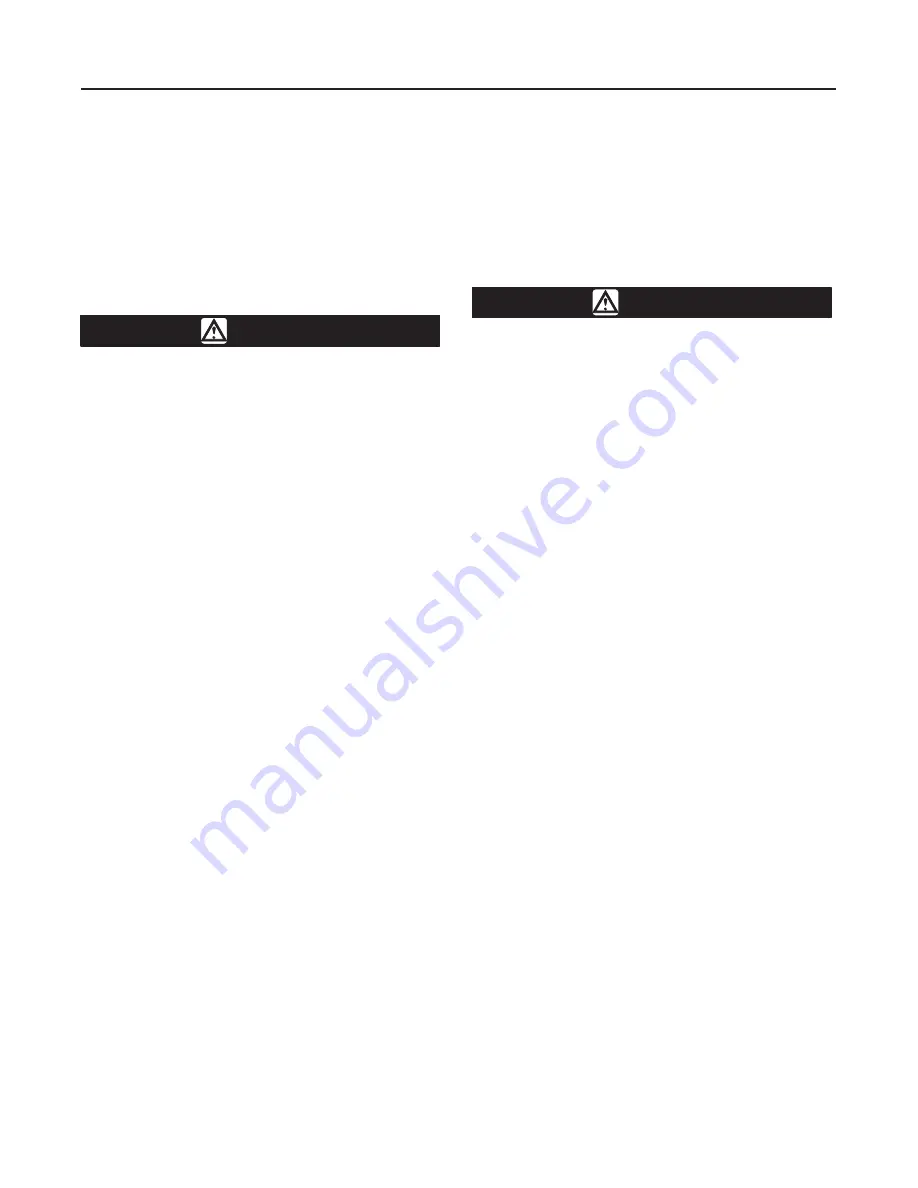
Type 9500
5
Adjust the seals if there is leakage through the valve
body around the valve shaft. A small amount of leak-
age downstream (between the bushings and disk
hubs) may also indicate a need for hub seal adjust-
ment.
To adjust the hub seals:
1. Tighten both thrust-plate cap screws (key 10) 1/4
turn on one side (the side where shaft leakage is oc-
curring).
CAUTION
To avoid excessive side thrust on the
disk and possible liner damage, tighten
cap screws on both sides of the valve
alternately and in 1/4-turn increments.
Do not over-tighten by continuous turn-
ing or by tightening one side only. Over-
tightening the cap screws will cause the
liner to fail.
2. Tighten both thrust-plate cap screws 1/4 turn on
the other side of the valve.
3. Repeat steps 1 and 2 until leakage stops.
Note
If this adjustment is being performed to
stop minor leakage past the disk, check
the leakage after turning the cap screws
enough to move the thrust plates 1/32
inch (0.8 mm) closer to the valve body. If
leakage has not stopped or diminished,
the leakage is probably due to incorrect
linkage adjustment or damaged valve
parts. Refer to the
Linkage section to
check linkage adjustment; refer to the
Maintenance section to inspect and re-
place parts.
4. If leakage around the shaft cannot be stopped by
adjusting hub seals, refer to the
Maintenance section
to inspect and replace damaged parts.
Linkage
If the linkage between the power actuator and valve is
improperly adjusted, the actuator may reach the end
of travel before (or after) the disk reaches the fully
closed position. This could result in leakage past the
disk. The linkage adjustment is set at the factory, and
it should not be necessary to adjust linkage unless the
actuator and valve have been separated and the ad-
justment altered.
To check the linkage adjustment on Fishtail disks, the
flat is on the same side of the shaft as the nose or
leading edge of the valve disk (as shown in figure 2).
When the valve disk is at the fully closed position, the
flat will be either top-dead-center or bottom-dead-cen-
ter in relation to the valve body. The top-dead-center
position is shown in figure 2. A more accurate check of
the fully closed disk position is obtained by removing
the valve from the pipeline.
WARNING
To avoid personal injury and damage to
the process system caused by the sud-
den release of pressure, isolate the con-
trol valve from all pressure and relieve
pressure from the valve body before re-
moving the valve from the line. Be sure
the disk is closed so that it will not hit
the mating flanges when being removed
from the line.
With the valve removed from the line, position the ac-
tuator to the valve-closed end of the travel. Measure
the distance between the valve face and the top and
bottom edges of the disk as shown in figure 2. The
disk is at the fully closed position if the two measure-
ments are equal.
To adjust linkage, refer to the actuator instruction
manual.
Three-Way Valve Tandem Linkage
If the valve is used as part of a three-way valve as-
sembly, adjustment of the tandem linkage (see figure
5) may be necessary to ensure proper rotation of the
slave valve disk.
If the adjustment is being performed with the three-
way valve assembly out of the line, temporarily bolt
the valve bodies to the tee to compress the liner faces
until there is metal-to-metal contact between the valve
bodies and the tee.
Check the rotation of the power valve disk per instruc-
tions in the
Linkage section. If necessary, adjust the
linkage between the actuator and the power valve.
To check the fully closed position of the slave valve
disk, use the partial keyway on the slave valve shaft or
measure equal distances between the slave valve face
and the top and bottom of the slave valve disk as de-
scribed in the
Linkage section. Tighten locknuts on
tandem linkage when adjustment is complete.