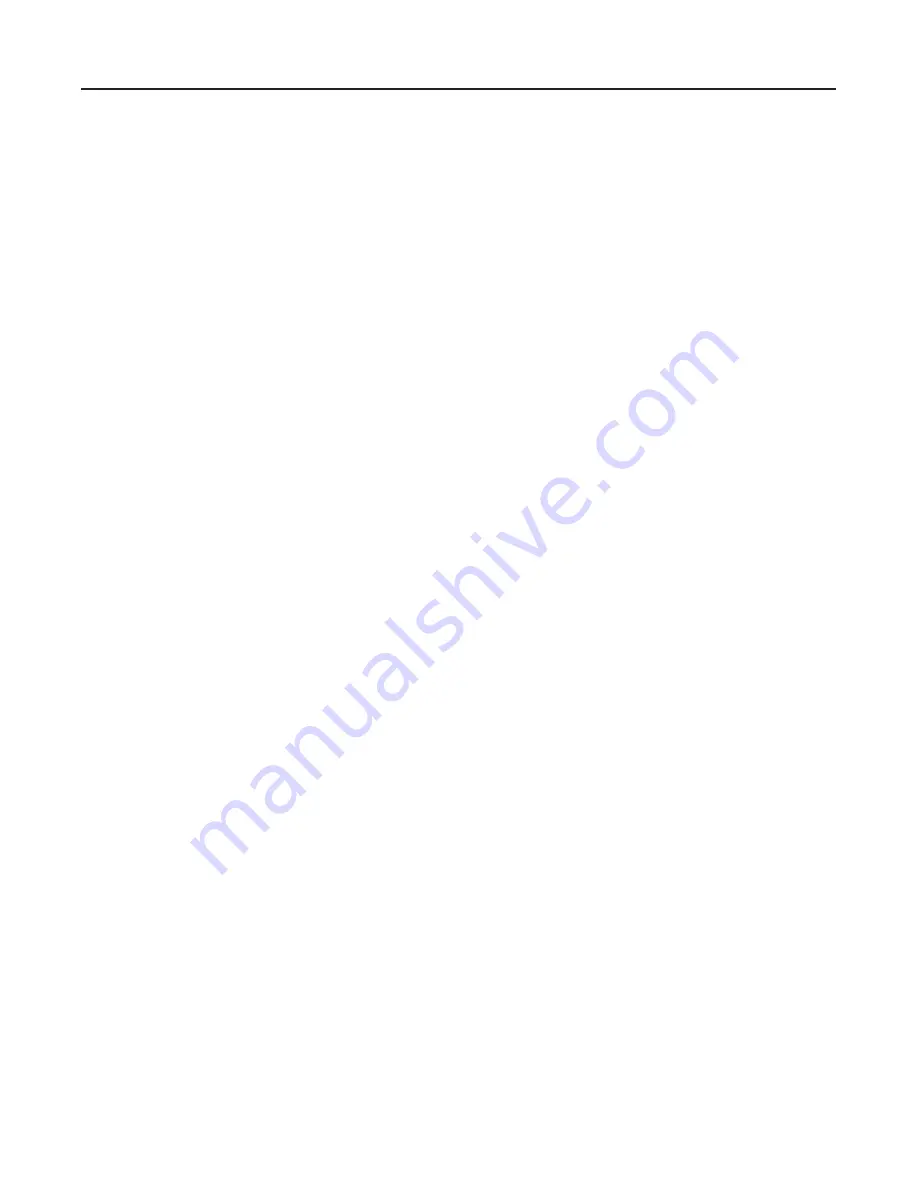
4194A, B, and C Series
5–27
5. Remove the screw (key 122), washer (key 123)
and nut (key 124) that attach the guide flexure (key
119) to the top of the pivot assembly.
6. Remove the pivot screw and spring washer (keys
109 and 112) and the mounting screw (key 102) at-
taching the pivot assembly to the mounting plate (key
111). Lift out pivot assembly A.
7. Loosen the adjustment screw (key 118) on the ad-
justment arm of the replacement pivot assembly, and
set the arm to the same length as the arm on the pivot
assembly being replaced. Tighten the screw.
8. To replace the pivot assembly, first put the spring
washer (key 112) on the screw (key 109). Then, insert
the screw through the replacement pivot assembly and
into the mounting plate and tighten. Install the mount-
ing screw (key 102) and tighten.
9. Connect the guide flexure (key 119) to the top of
the replacement pivot assembly with the screw (key
122), washer (key 123), and nut (key 124) as it was
before. The guide flexure should be straight and hori-
zontal as shown in figure 5-20. If not, loosen the
screws (key 122) and retighten to eliminate any bow-
ing. Loosen the screws (key 139) and raise or lower
the pedestal assembly (key 105) to get the link hori-
zontal. Retighten the screws (key 139) and ensure the
diaphragm assembly extension (key 134) is centered
in the upper travel stop (key 83) hole.
10. Apply remote set point pressure equal to 50 per-
cent of the remote set point input range.
Note
See figure 5-18. The adjustment arm of
the remote set point pivot assembly A
turns on a bushing at each end of the
shaft supporting the adjustment arm. In
the next step, position the shaft so both
bushings ‘‘float’’ inside the bearings
and do not rest against the end of either
bearing.
11. Connect the drive flexure (key 79) to the arm on
the replacement pivot assembly, making sure it stays
straight and vertical. Adjust the length of the pivot arm,
if necessary, until the flexure is vertical. Before tighten-
ing the drive flexure screws, hold the pivot assembly
shaft in the middle of the bushing end play. Be sure
neither bushing is resting against the inside end of ei-
ther bearing. Tighten the drive flexure screws to hold
pivot assembly A in this position. Do not bend or twist
the flexure when tightening the screws.
12. Decrease the remote set point pressure to 0 psig.
13. Connect the end of link A (key 116) to the pivot
lever arm in the same holes noted in step 3.
14. Replace the tie bar (key 106).
15. Perform the remote set point maintenance calibra-
tion procedures. Perform the appropriate process indi-
cator zero and span calibration and flapper alignment
procedures in section 3 or 4.
Replacing Pivot Assembly B (Key 115)
1. Decrease the remote set point pressure to 0 psig.
2. Note the holes where links A and B are connected.
Disconnect links A and B (keys 116 and 126) from the
arms of pivot assembly B (key 115).
3. Remove the two screws (key 102) that attach pivot
assembly B to the mounting plate (key 111). Remove
the pivot assembly.
4. Loosen the linearity adjustment screw on the re-
placement pivot assembly, and set it in the same posi-
tion as the adjustment on the original pivot assembly.
Tighten the screw.
5. Set the replacement pivot assembly on the mount-
ing plate, and attach it with the two machine screws.
6. Attach links A and B (keys 116 and 126) to the
arms of the replacement pivot assembly in the same
holes noted in step 2.
7. Perform the remote set point maintenance calibra-
tion procedure. Perform the appropriate process indi-
cator zero and span calibration and flapper alignment
procedures in section 3 or 4.
Replacing the Drive Flexure
1. Using an Allen wrench, remove the cap screws
(key 12) and washers (key 13) to disconnect the drive
flexure (key 79) from the drive bracket (key 121) and
from the adjustment arm of pivot assembly A. Remove
the drive flexure.
2. Set the remote set point pressure to 50 percent of
the remote set point input range.
Note
See figure 5-18. The adjustment arm of
the remote set point pivot assembly A
turns on a bushing at each end of the
shaft supporting the adjustment arm. In
the next step, position the shaft so both
bushings ‘‘float’’ inside the bearings
and do not rest against the end of either
bearing.
3. Connect the new drive flexure making sure it stays
straight and vertical. Adjust the length of the pivot arm,
if necessary, until the drive flexure is straight. Before
tightening the drive flexure screws, hold the pivot as-
sembly A shaft in the middle of the bushing end play.
Be sure neither bushing is resting against the inside
end of either bearing. Tighten the drive flexure screws
to hold the pivot shaft in this position. Do not bend or
twist the flexure when tightening the screws.