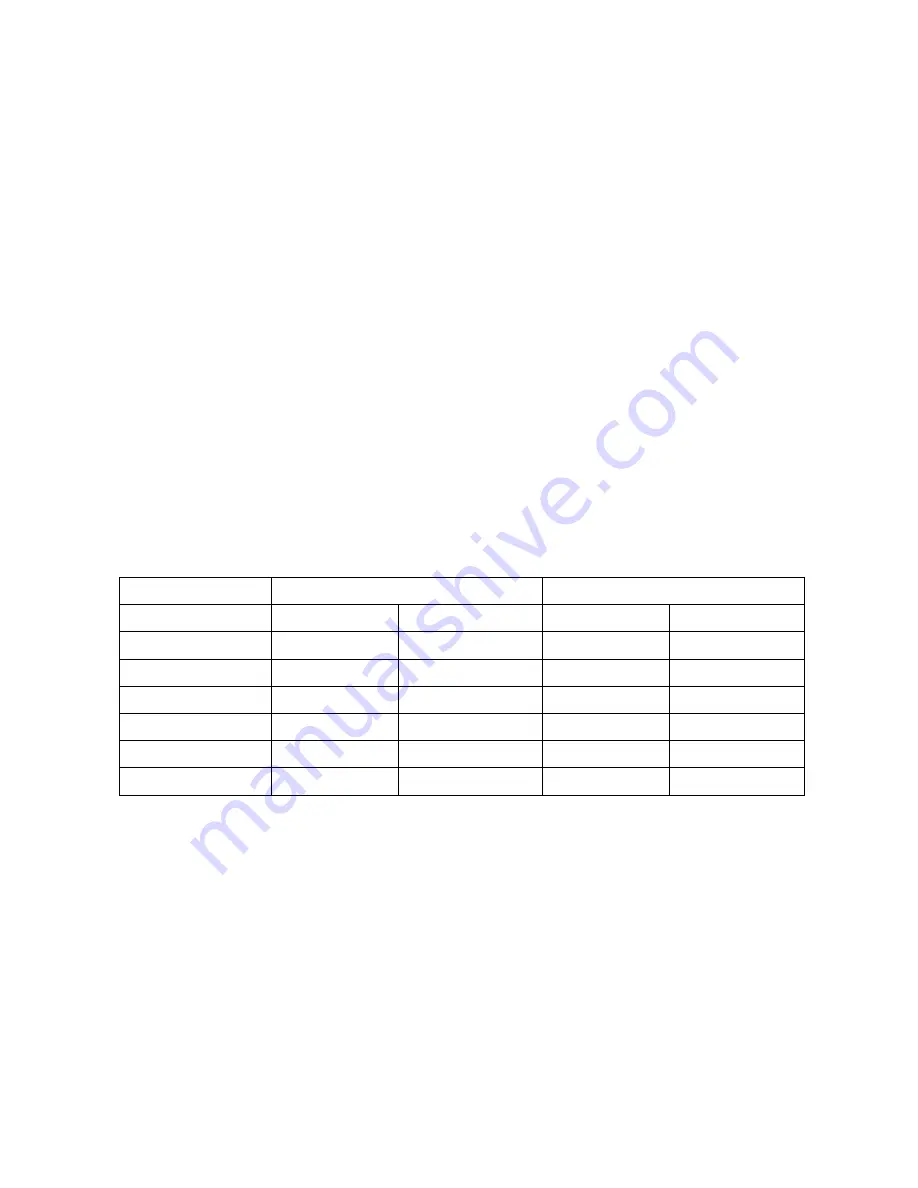
FIRST STOP SAFETY
9
Environment
The location of equipment will have a bearing on the frequency of testing.
For example an item that is used in a low-risk environment such as an office
will have a much lower risk of damage than an item used on a construction
site. Please see below for various examples.
Low risk: Offices, shops, hotels and nursing homes
Medium risk: Schools
High risk: Factories, commercial kitchens and equipment used by the public.
Very high risk: Construction sites
Frequency of visual inspection and testing
It is not essential to carry out inspecting and testing every year. Table 1 below
gives some intervals that are recommended in low risk environments, such as
offices, shops, hotels, and nursing homes. (Timescales for other environments
can be found in Appendix I)
Class I
Class II
Type
Inspection
Insp. & test
Inspection
Insp. & test
Stationary
24 months
60 months
24 months
none
IT
24 months
60 months
24 months
none
Movable
12 months
24 months
24 months
none
Portable
12 months
24 months
24 months
none
Hand-held
12 months
24 months
12 months
none
Table 1: Frequency of inspection and testing in low risk environments
Equipment Register
This form is used to list all the electrical equipment in the business.
Information, such as Class I or II, type of equipment and frequency of test is
recorded. A blank form is supplied, and this can be photocopied and used if
additional sheets are required. As new equipment is purchased, this needs to be
added to the register.
BattPAT
Issue 2.