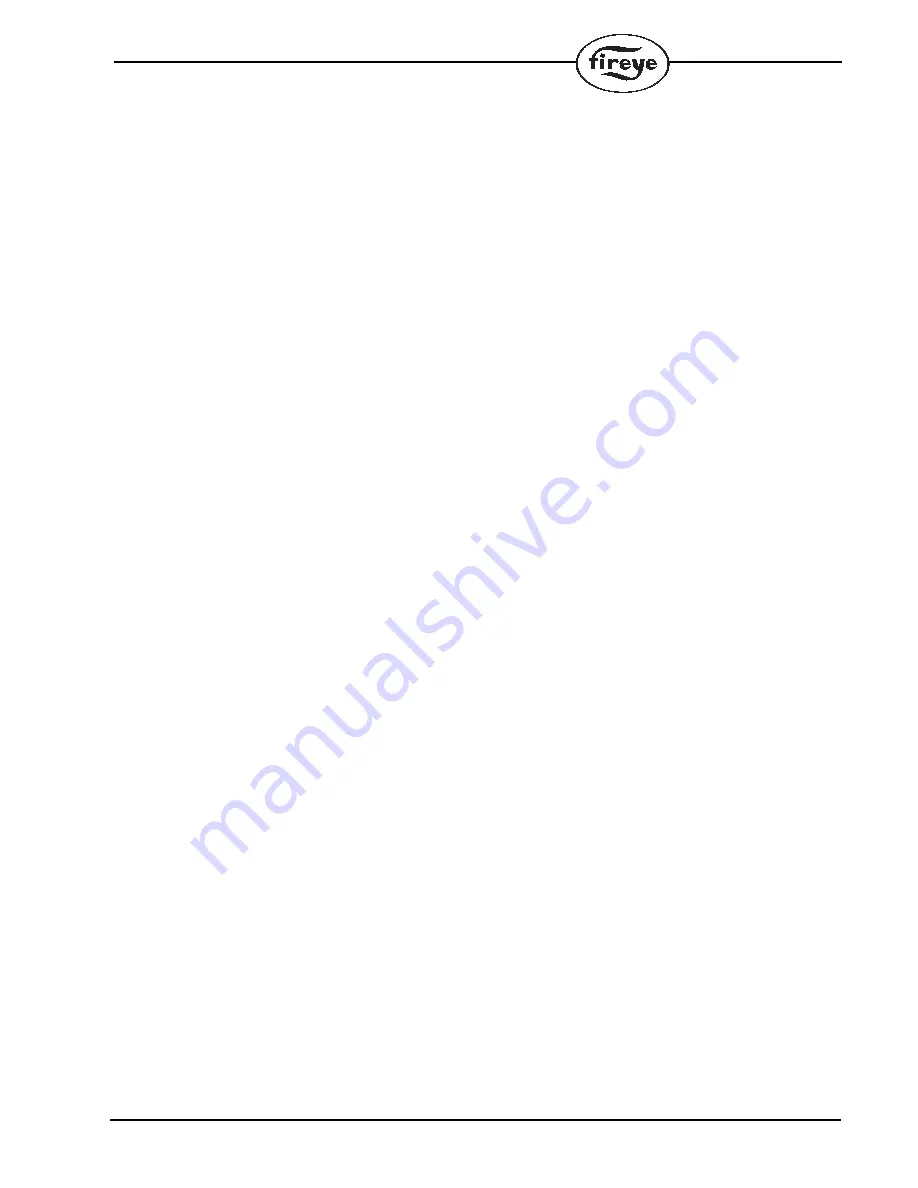
17
®
NOTES:
1)Presence of flame at this point results in a lockout.
2)When CAST (terminal 13) is open and POC (terminal 12) is open at this point, control locks out after 10 min-
utes. When CAST is open and POC is closed, control remains in same state indefinitely.
3)Control locks out if FEEDBACK (terminal 8) is not present after 10 minutes.
4)CAP (terminal 14) input is required to proceed. Otherwise, control locks out, after 10 minutes.
5)FEEDBACK (terminal 8) must remain present. Otherwise, control locks out, after 10 minutes.
6)Presence of real flame is mandatory. Otherwise, control locks out. Flame failure results in Post-Purge at
lockout.
7)The control locks out if POC (FVES) cannot be proven closed upon call for heat.
EXPLANATION OF SEQUENCE STATES
1) POWER ON
This is the application of power to the control. It's important that a single phase (110/230 VAC 50/
60 Hz) is applied to the control and the inputs to the control are sourced from the same phase.
2) INITIAL SYSTEM CHECK
During this state, the control undergoes an internal Power-On Self-Test (POST) to verify that the
hardware and software are operating properly. The non-volatile lockout feature forces the control
to move to lockout if the last lockout condition was not cleared prior to power off. The control fur-
ther checks the critical input and output terminals to make sure they are in the proper state. The
control expects the flame to be completely extinguished at this point.
3) PRECONDITIONS FOR BURNER STARTUP
The control verifies that the air-flow switch is in the Normally Closed position via the Combus-
tion Air Switch Test (CAST) input and a verification of the main fuel shutoff valve (POC/FVES)
is performed as well. Flame must not be present at this point. Failure to prove POC or CAST input
will lead to a halt in the state sequence or the control will proceed to lockout.
4) CALL FOR HEAT
The recycle limit (terminal 5) is energized to alert the control to start a burner cycle.
5) PREPARE FOR PURGE CYCLE
The control turns on the combustion blower (terminals 6 & 7).
6) MOVE TO PURGE
The control commands the damper actuator to move to the OPEN (high fire) position. It expects
the actuator to report a successful transition to the OPEN position by energizing the FEEDBACK
input (terminal 8). The control also checks to make sure that the airflow switch is operating by
monitoring the CAP input.
7) PURGE
The control purges the combustion vessel for a period of time (length of purge is based on the
control series installed).
8) MOVE TO IGNITION
Upon successful purging, the control moves to ignition by energizing the MINIMUM output (ter-
minal 10). It expects the actuator to report a successful transition to the MINIMUM (LOW FIRE)
position by energizing the FEEDBACK input (terminal 8). Flame must not be present at this
point.
9) IGNITION
The control energizes the ignition transformer by activating terminal 16. It's critical that the
damper actuator remain at the MINIMUM (LOW FIRE) position during this state. Flame must not
be present at this point.