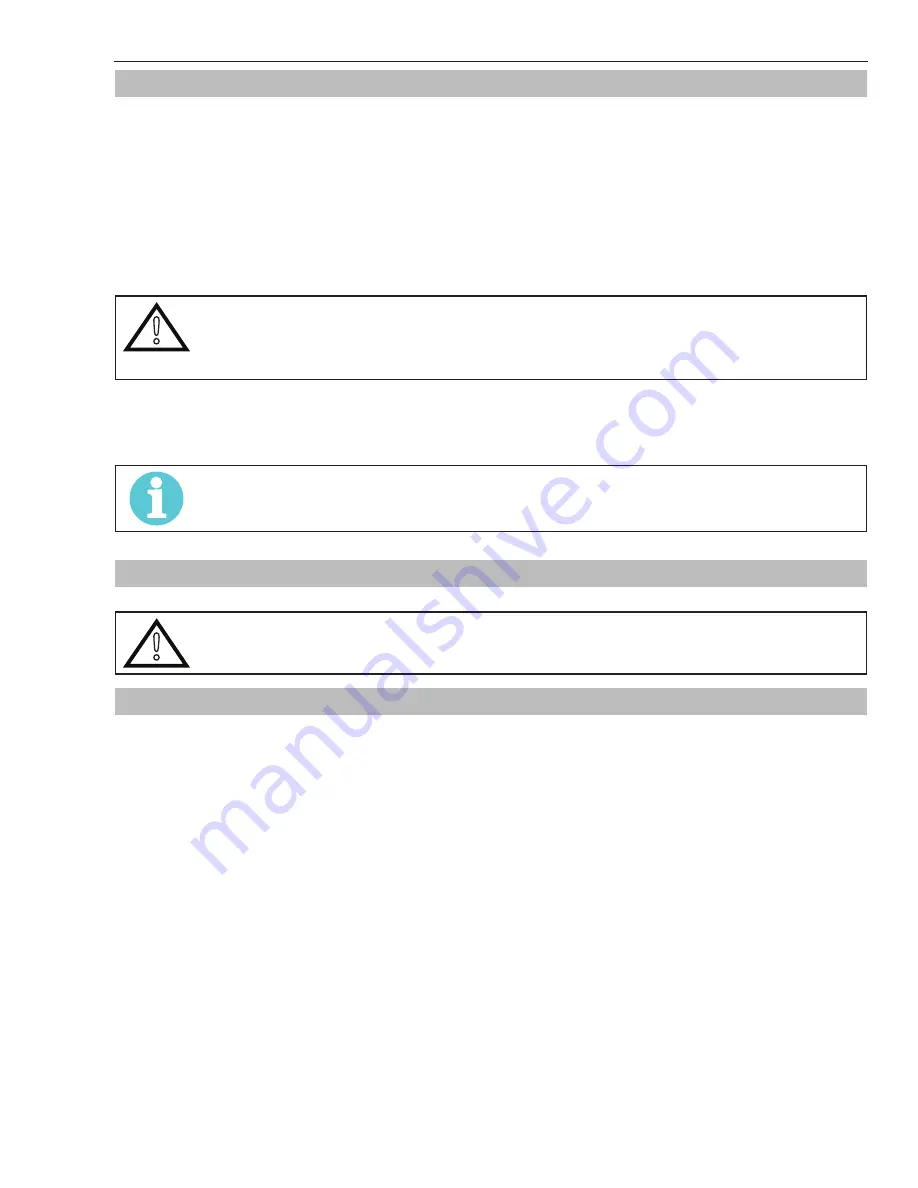
OPERATION
FIREPOWER FP 95 FC
Operation 4-3
Manual 0-5122
4.03 Flux Cored Arc Welding (FCAW)
See Welding Guidelines included in this manual.
1. Make all necessary connections as instructed in the INSTALLATION chapter.
2. Place the WELDING OUTPUT VOLTAGE SELECTOR at the desired setting.
3. Rotate the WIRE SPEED FEED control to the desired setting.
4. Plug the supply cord into a 120 VAC 20 Ampere receptacle.
5. Connect the WORK CLAMP to the workpiece (material to be welded).
6. Extend wire from the gun, and cut to proper stick-out for that type of wire (when welding always maintain this distance).
7. Position gun to where it is at approximately right angles to the workpiece with proper wire stick-out. Lower your welding
helmet and pull the gun trigger switch.
!
WARNING
Be sure to put on proper protective clothing and eye safeguards (welding coat, apron, gloves, and welding
helmet with proper lenses installed). See Safety Instructions and Warnings chapter included in this manual.
Neglect of these precautions may result in personal injury.
Travel at a speed necessary to maintain a bead width from 1/8" to ¼" (3mm to 6mm) depending on the thickness of the material. For
material that may require larger weldments, either change to a larger diameter filler wire or use multi pass beads. On some applica-
tions, it may be necessary to adjust the voltage range to stabilize the arc.
Upon completion of the weld, release the gun trigger switch, raise the welding helmet, and visually examine the weld.
NOTE!
To help you overcome any problems that might arise, you will find useful information in section 4.05 Basic
Welding Techniques.
4.04 Shutdown Procedures
Place the POWER ON/OFF SWITCH in the OFF position.
!
WARNING
After releasing the gun switch, the electrode wire will remain electrically “hot” for several seconds.
4.05 Basic Welding Technique
General
Two different welding processes are covered in this section, with the intention of providing the very basic concepts in using the semi-
automatic mode of welding. In this mode, the welding gun is hand-held. The electrode (welding wire) is then fed into a weld puddle and
the arc is shielded by a gas or gas mixture.
Setting of the Power Supply
The settings of the Firepower FP 95 FC requires some practice by the operator in that the welding Power Supply has two control
settings that need to balance. These are the Wire Speed control and the Voltage Control switches. The welding current is determined
by the Wire Speed control (i.e., the current will increase with increased wire speed, resulting in a shorter arc). Slower wire speed will
reduce the current and lengthen the arc. Increasing the welding voltage hardly alters the welding current level, but lengthens the arc.
By decreasing the voltage, a shorter arc is obtained with little change in welding current.
When changing to a different electrode wire diameter, different control settings are required. A thinner electrode wire needs more wire
speed to achieve the same current level.
A satisfactory weld cannot be obtained if the wire speed and voltage switch settings are not adjusted to suit the electrode wire diam-
eter and dimensions of the work piece.
If the wire speed is too high for the welding voltage, “stubbing” will occur as the wire dips into the molten pool and does not melt.
Welding in these conditions normally produces a poor weld due to lack of fusion. If however, the welding voltage is too high, large drops
will form on the end of the electrode wire, causing spatter. The correct setting of voltage and wire speed can be seen in the shape of
the weld deposit and heard by a smooth regular arc sound.
Summary of Contents for FP 95
Page 14: ...FIREPOWER FP 95 FC INTRODUCTION Manual 0 5122 2 4 Introduction This Page Intentionally Blank...
Page 28: ...FIREPOWER FP 95 FC SERVICE Manual 0 5122 5 4 Service This Page Intentionally Blank...
Page 33: ...APPENDIX FIREPOWER FP 95 FC Appendix A 5 Manual 0 5122 This Page Intentionally Blank...
Page 35: ......