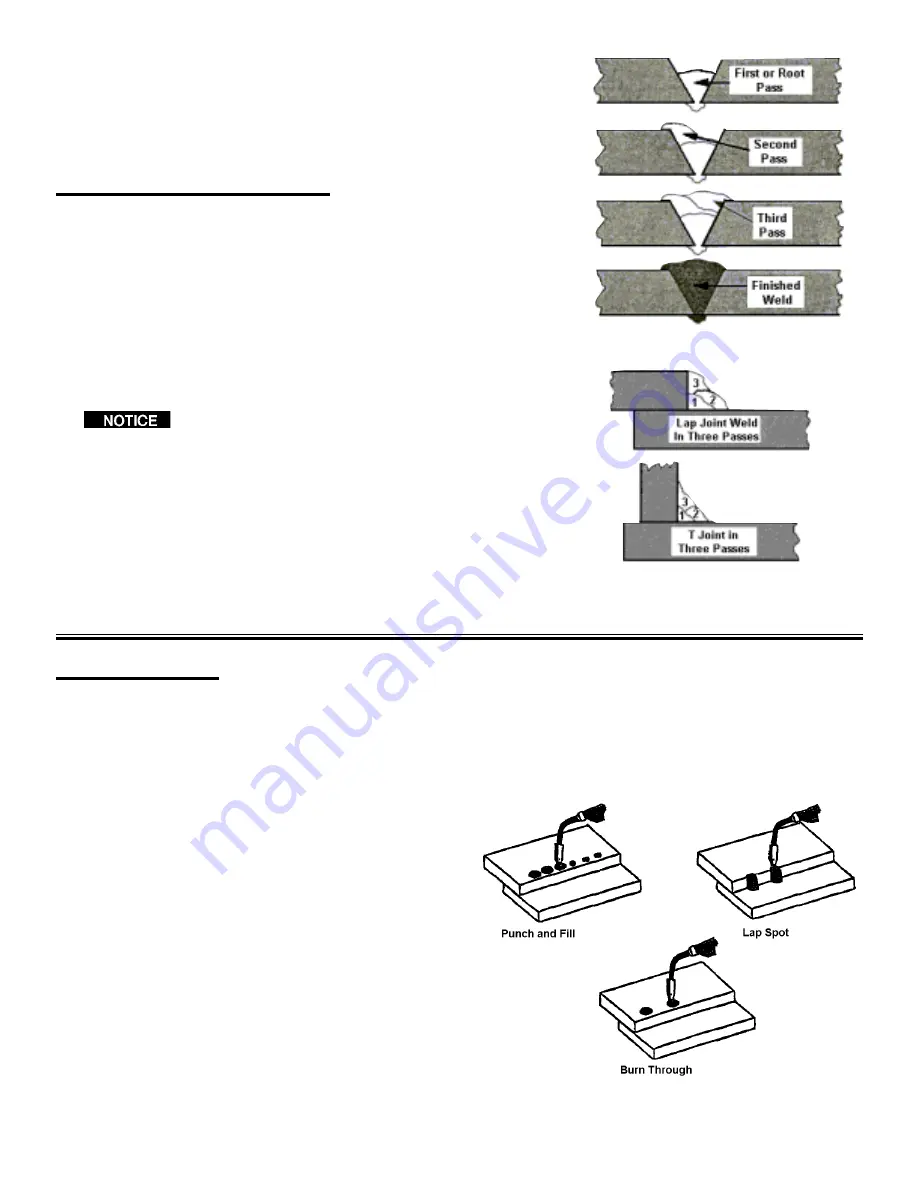
falling into the nozzle should it drip from the weld puddle. Hold
angle B at 0º so that the wire is aiming directly into the weld joint.
If the weld puddle drips excessively, select a lower heat setting.
Also, the weave bead tends to work better than the stringer bead
when welding overhead.
MULTIPLE PASS WELDING
1.
Butt weld joints
- In "Preparing the Workpiece," we discussed the
need for edge preparation on thicker materials by grinding a bevel
on the edge of one or both pieces of metal being joined. The bevel
creates a "V" between the two pieces of metal that must be welded
closed. More than one bead is often necessary to be laid into the
joint to close the "V". Laying more than one bead into the same
weld joint is known as a multiple-pass weld.
The illustrations in Figure 17 show the sequence for laying multiple
passes into a single Vbutt joint.
When using self-shielding flux-core wire, it is
VERY important to thoroughly chip and brush the slag off
each completed weld bead BEFORE making another pass.
Failure to do so results in a poor quality bead.
2.
Fillet weld joints
- Most fillet weld joints on metals of moderate to
heavy thickness require multiple pass welds for a strong joint. The
illustrations in Figure 18 show the sequence of laying multiple pass
beads into a T-fillet joint and a lap fillet joint.
SPECIAL WELDING METHODS
SPOT WELDING
Spot Welding joins pieces of metal together with a spot of weld instead of a continuous weld bead. There are
three methods of spot welding: burn-through, punch and fill, and lap (see Figure 19). Each method has advan-
tages and disadvantages depending on the specific application and personal preference.
1. The burn-through method welds two overlapped pieces
of metal together by burning through the top piece and
into the bottom piece. Larger wire diameters work bet-
ter for this method. Larger wire diameters have greater
current carrying capacities. This allows the arc to burn
through very quickly while leaving a minimal amount
of filler metal build up. Wire diameters that work best
with the burn-through method are 0.030 inch diameter
solid wire or 0.035 inch self-shielding flux-core wire.
DO NOT
use 0.024 inch diameter solid or 0.030 inch
self-shielding flux-core wires when using the burn-
through method unless the metal is
VERY
thin or
excessive filler metal build-up and minimal penetration
is acceptable.
ALWAYS
select the
HIGH
heat setting with the burn-
through method and tune-in the wire speed prior to
making a spot weld.
18
Figure 17: Triple Pass V Butt Joint
Figure 18: Triple Pass Lap and T Weld Joint
Figure 19: Spot Weld Methods
Summary of Contents for FP-90
Page 2: ......
Page 27: ...23 Figure 21 FP 90...
Page 29: ...25 Figure 22 FP 90 Wiring Diagram...
Page 30: ...26...