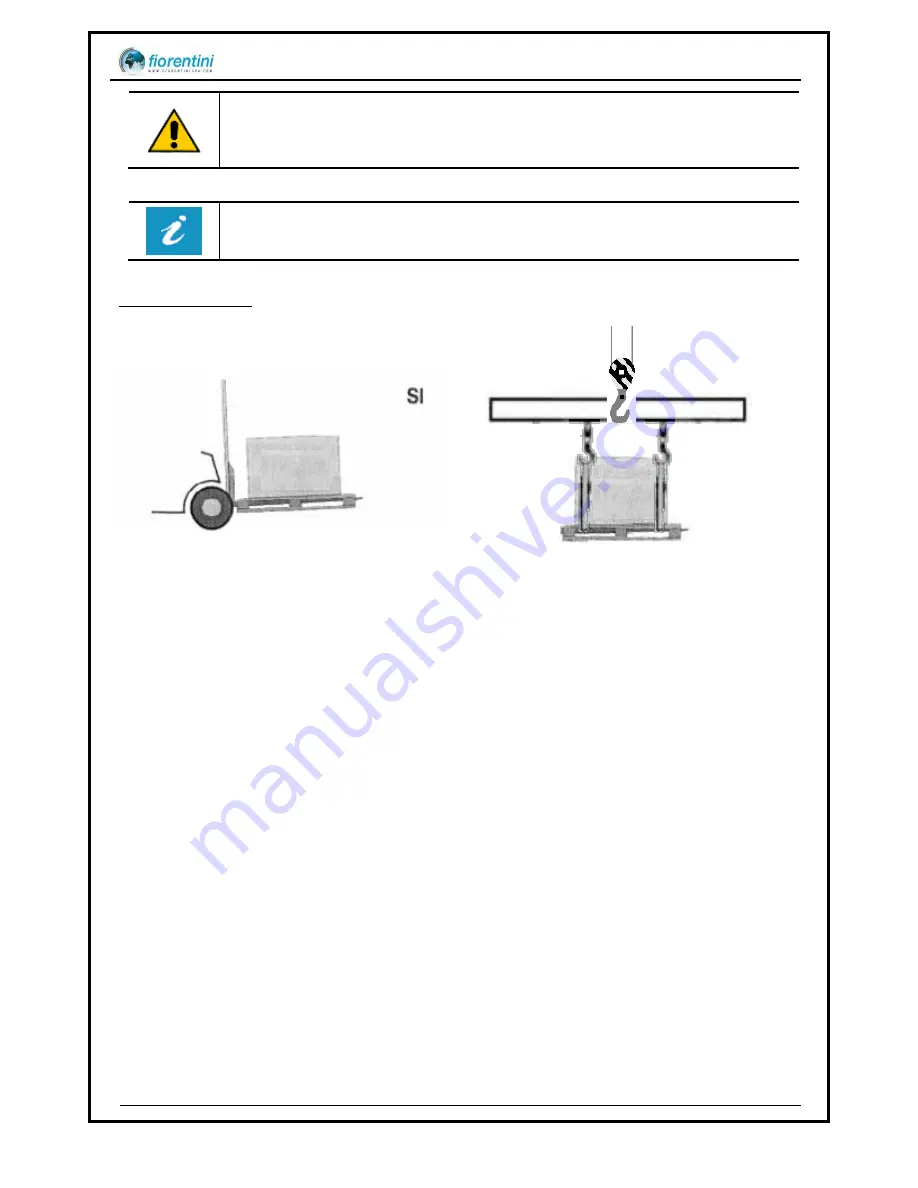
START-UP AND OPERATION INSTRUCTIONS
Ecosmall
Rev. 000
29/11/2017
19/41
The harness straps used must be suitable for the load to lift. All handling
operations should be carried out at very slow speed to prevent load swinging and
loss of stability. Any operation performed incorrectly may damage the machine and
expose operators to dangers.
Refer to point 2.3 for machine dimensions and weight. Machine handling should be
carried out by authorised personnel trained for lifting equipment use only.
LOADING DIAGRAM
4.2. STORAGE
If not immediately installed, the machine should be stored at a covered, dry location to ensure the perfect
efficiency of all its parts. Relative humidity must be below 80% and the storage temperature must be
between 3°C
and
+ 45 °C
.
4.3. MACHINE UNPACKING
Cut the straps bearing in mind that they might spring back
Remove the staples fixing the carton to the pallet
If the crate is made of plywood, remove the staples from each side and the base of each panel
Cut the straps that secure the machine
Place the machine on the floor
4.4 UNPACKED MACHINE HANDLING
Inspect the machine and install the batteries if not already installed
To prepare the machine for short distance handling after use, disconnect the battery cables and
remove the brushes and the squeegee; for longer-distance transport, the machine should be
repacked in its original packaging.
FIGURE N. 4.2
FIGURE N. 4.3