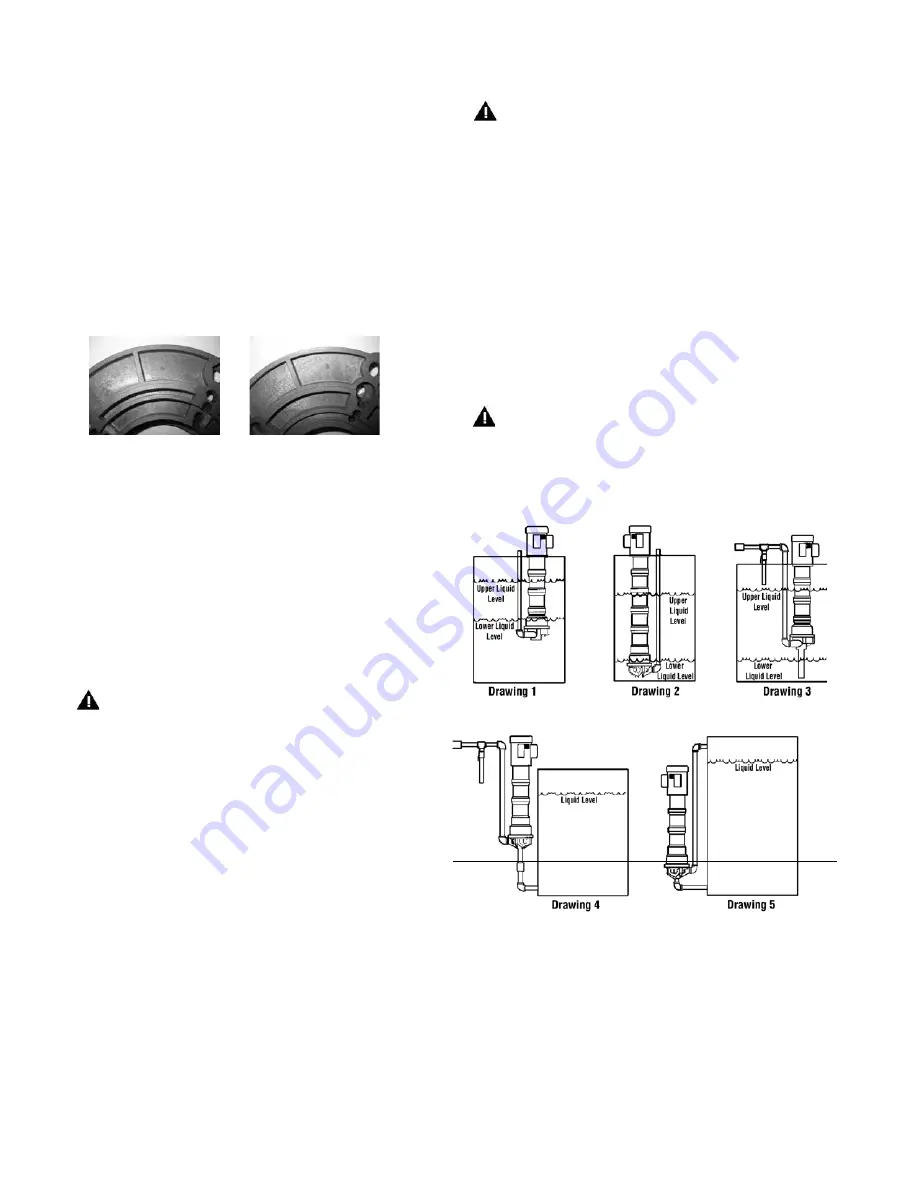
2
with side “A” facing up. The metric motor adapter must be positioned
so that the adapter seats onto the motor rabbett. See figures A and B
above.
CAUTION
: Improper positioning of the metric motor adapter can
cause premature coupling failure or cause the pump shaft to bottom
out before the pump is properly installed onto the motor adapter.
5. Install the flywheel (item 35 in figure 8) onto the flywheel adapter and
attach using four screws with lock washers (items 36 and 37 in figure
8). Tighten securely.
6. Insert the coupling insert (yellow internally splined plastic sleeve) into
the coupling half on the motor. Carefully slide the motor adapter end
(item 9 in figure 8) of the pump assembly over the motor shaft until
both coupling halves are completely seated in the coupling insert. Make
sure rabbet on the motor is firmly seated into the motor adapter.
7. Rotate the pump discharge and mounting plate if ordered to the desired
orientation. Align the boltholes on the mounting plate with the motor
adapter (item 9) and the metric motor adapter flange (item 2). Secure
with the hardware provided.
8. Make sure that the locking rings are securely snapped in place and
did not loosen during shipping or the assembly process.
CAUTION
: Pump assembly may be top heavy.
Install the pump into the system according to the installation instruc-
tions provided.
Drawing 1 shows drawing of pump mounted inside tank with suction off the bottom of the
tank and level fluctuating from near top of pump column to close to the bottom of the pump.
Drawing 2 shows drawing of pump suction near tank bottom and level fluctuating between
the top and bottom of the tank.
Drawing 3 shows drawing of pump with suction extension and the level fluctuating between
startup level and low level.
Drawing 4 shows drawing of pump mounted outside the tank.
Drawing 5 shows drawing of pump mounted outside the tank with the motor below the
liquid level.
Figure 1
Figure A
Figure B
correct hardware (items 3, 4, and 5 in figure 7), mount the adapter
with side B facing up. For 63 and 80 frame motors, using the correct
hardware (items 3, 4, and 5 in figure 7), mount the adapter with side
A facing up. See figures A and B.
5. Install the coupling insert (yellow internally splined plastic sleeve) onto
the coupling half on the motor shaft. Carefully slide the motor adapter
(item 9 in figure 7) onto the motor making sure the pump shaft coupling
matches up with the plastic insert and seats properly. Make sure rabbet
on the motor is firmly seated into the motor adapter.
6. Rotate the pump discharge and the mounting plate if ordered to the
desired orientation. Align the bolt holes on the mounting plate with the
motor adapter (item 9) and the metric motor adapter flange (item 2).
Secure with the hardware provided.
CAUTION
: Pump assembly may be top heavy.
7. Make sure that the locking rings are securely snapped in place and
did not loosen during shipping or the assembly process.
8. Install the pump into the system according to the installation instruc-
tions provided.
FOR 80 FRAME METRIC MOTOR ADAPTER WITH
FLYWHEEL (ITEM 35 IN FIGURE 8):
1. Unpack the pump parts and any supplied accessories and examine
for damage. If damage is detected, save the packaging and notify the
carrier immediately.
2. Prepare to assemble the pump onto the motor by placing the motor on
the fan cover on a suitable clean, level work surface.
3. Install the keyway into motor shaft key slot. Align the keyway slot in
flywheel adapter / coupling half combination (item 34 and metal half of
item 27 in figure 8) and install on motor shaft with splined side facing the
pump. Note: These items are preassembled at the factory. Set coupling
half flush with the end of the motor shaft and secure with coupling sup-
port washer, lock washer and bolt (items 38B, 39 & 40). Tighten both
setscrews in coupling half with 1/8” Allen wrench to 7.9 N-m.
4. Install the metric motor adapter (item 2 in figure 8) onto the motor. To
aid in correct installation, the letters “A” and “B” are molded on the
opposite sides of the metric motor adapter. For 80 frame motors using
the correct hardware (items 3,4 and 5 in figure 8) mount the adapter
FOR 63, 71 AND 80 METRIC FRAME ADAPTERS
WITHOUT FLYWHEELS (USE FIGURE 7)
1. Unpack the pump and any supplied accessories and examine for damage. If
damage is detected, save the packaging and notify the carrier immediately.
2. Prepare to assemble the pump onto the motor by placing the motor
on the fan cover on a suitable clean, level work surface.
3. Install the keyway into the motor shaft key slot. Align the keyway slot
in the coupling half, and slide the coupling half onto the motor shaft
with the splined side facing the pump. Set the coupling half with the
motor shaft recessed 11.1 mm. Tighten both setscrews with a 1/8”
Allen wrench to 7.9 N-m.
4. Install the metric motor adapter (item 2 in figure 7) onto the motor.
To aid in correct installation, the letters “A” and “B” are molded onto
opposite sides of the motor adapter. For 71 frame motors, using the