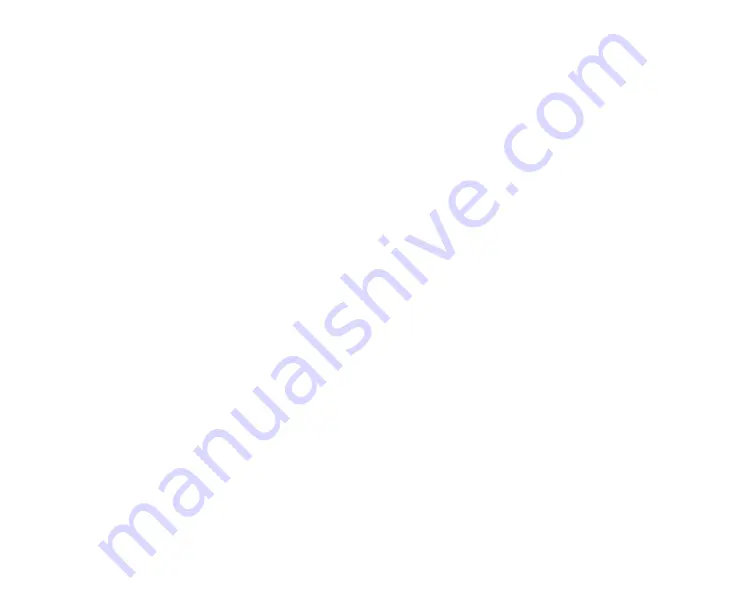
11
10
Safety Information
First Aid for Refrigerant Exposure
Inhaled: Move to fresh air immediately.
Eye:
Immediately flush eye with water. Seek medical attention.
Skin:
Immediately flush skin with water. Seek medical attention.
General
1. This is not a consumer machine. Only qualified personnel trained
in the recovery or pumping of refrigerant may operate this
machine.
2. Read and understand this operator’s manual in its entirety before
using MR45INT to prevent injury or damage to you or equipment.
Environmental
1. Use only within operating conditions (0°C to 43°C)
2. Ensure fan opening is clear of debris.
3. Explosion and fire risks:
Do not use near sewer lines.
Do not use in poorly ventilated enclosed areas.
Do not use near gasoline, acetylene, or other flammable gases.
Do not use to pump hydrocarbons.
Do not use near flames or sparks.
Assume all components are pressurized.
Personal Protection
1. Frostbite danger. Be careful using hoses.
2. Use personal protective equipment:
Wear safety goggles.
Wear earplugs if using for long durations.
Wear protective gloves.
3. Use a scale as the primary indicator of refrigerant cylinder fill
status. Overfill sensor protection should only be used as backup.
MR45INT Protection
1. Use only on approved list of refrigerants (page 8).
2. Do not use with hydrocarbons.
3. Ensure mesh screen filter is installed and clean (page 32).
4. Use a filter drier on the input port and change it often to protect
machine from contaminated refrigerants.
Setup
1. Ensure power switch is OFF before plugging into power.
2. Repair any damaged parts before using.
3. Disconnect power and allow fan to stop before opening or
servicing MR45INT.
4. Perform self test periodically (page 24).
5. Ensure power cord is not damaged.
6. Ensure power cord is fully connected to IEC port (page 17).
7. Ensure all equipment is grounded.
8. Extension cord options:
14 AWG or thicker, up to 15 meters (50 feet)
12 AWG or thicker, up to 30 meters (100 feet)
9. Ensure extension cord is grounded, 3 conductor grounded.
Operational
1. Use correct refrigerant hoses with ball valve shutoffs.
2. Keep track of the current amount of refrigerant in the cylinder.
Refrigerant scales are a good way to do this.
3. Overfilling a cylinder past 80% can cause an explosion and
violates DOT laws.
4. Close cylinder off from refrigerant if it reaches 80% of its capacity.
5. Use only DOT CFR 49 or UL-approved refrigerant cylinders for the
refrigerant being recovered.
6. Use recommended accessories.
7. Monitor pressures and temperatures.
8. Self purge MR45INT after each use. No refrigerant should remain
in the machine.