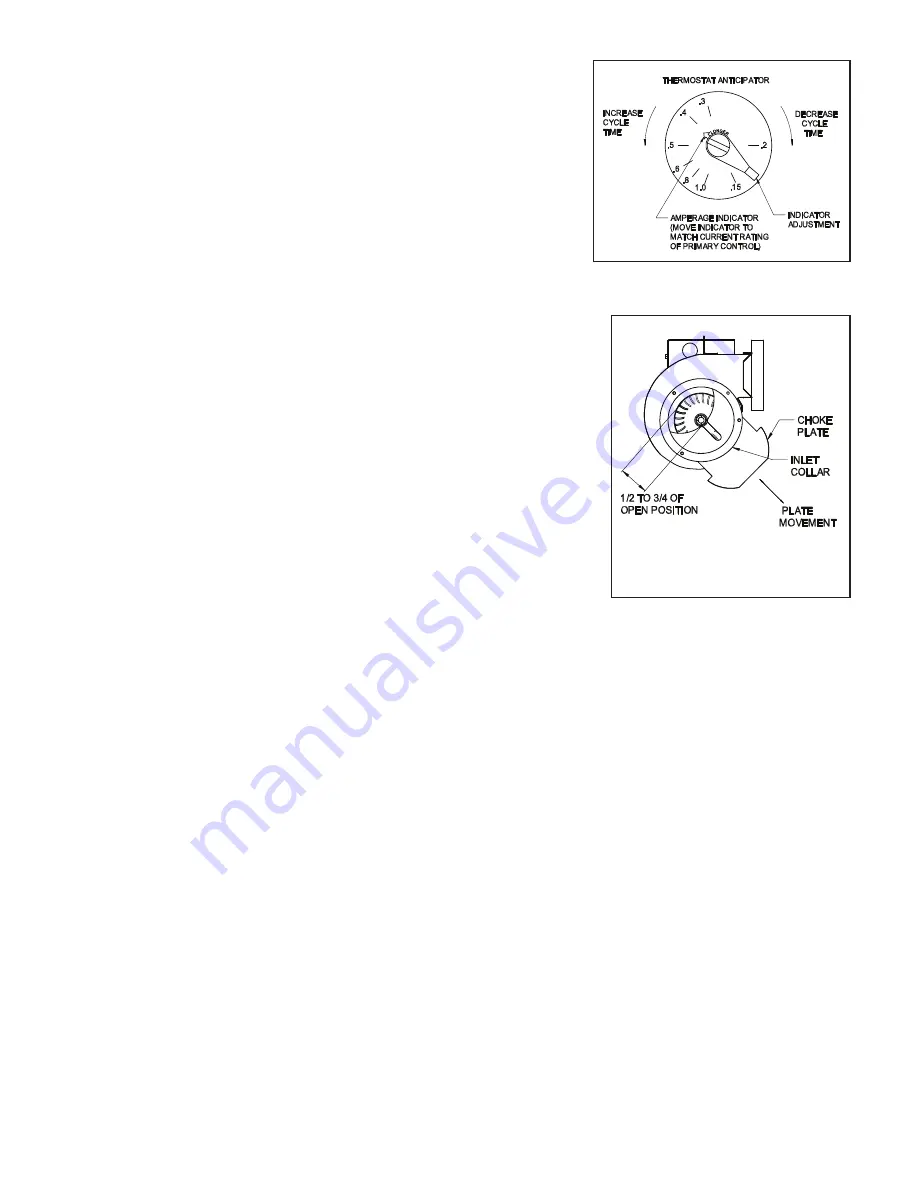
page 8 of 12
ADJUSTING THERMOSTAT ANTICIPATOR
If connecting the Power Venter system to a gas appliance with a thermostat
anticipator, refer to the following to make adjustments. Disconnect one
side of the thermostat circuit at the gas valve or burner control, and
connect an ampere meter into the circuit. With the system running, take
an amperage reading on the circuit. Check the nameplate or instructions
for the thermostat to obtain the proper amperage level. Adjust amperage
level by moving the anticipator lever. Reconnect the thermostat to the
gas valve and start the system operating. Time the burn cycles and
adjust as follows; To make the cycle time longer, increase the amount on
the anticipator (Example: .45 to .5 Amps); to decrease cycle time, reduce
the amount on the anticipator (Example: .45 to .3 Amps). (See Figure 8)
AIR FLOW ADJUSTMENTS
1. To properly adjust the venter air fl ow, loosen the inlet ring screws and
open the choke plate approximately
1
⁄
2
to
3
⁄
4
open. (See Figure 10) Start the
heating appliance following the manufacturer specifi ed procedure, and
set the thermostat to call for heat.
2. After the system has operated for several minutes to stabilize the exhaust
gas temperature, check for air fl ow at the draft hood or the heating
appliance outlet using a velocity meter, draft meter, or match test
procedure.
3. Adjust the venter choke plate inward or outward to obtain the minimum draft
necessary to maintain venting. Then increase the draft slightly (approximately
10% over minimum fl ow rate) to ensure proper venting during any variations
in venter performance, such as wind load or house depressurization.
4. Secure the choke plate into position by tightening the screws on the
inlet collar (See Figure 9)
GENERAL INSTALLATION INSPECTION
Follow recommended procedures for safety inspection of a heating appliance in accordance with the National Fuel
Gas Code ANSI Z223.1. The following procedure will help in evaluation of the venting system. It is intended as a
guide to aid in determining that the appliance is properly installed and is in a safe condition for continuous use.
This is a generalized procedure which cannot anticipate all situations. Accordingly, in some cases deviation from
this procedure may be necessary to determine safe operation of the equipment. If it is determined that a condition
which could result in unsafe operation exists, the appliance should be shut off and the owner advised of the unsafe
conditions. Corrections must be made prior to allowing continuous operation. The following steps should be taken
in making a safety inspection.
1. Visually inspect the venting system for proper size and determine that there is no blockage, restriction, leakage,
corrosion, or other defi ciencies which could cause unsafe operation.
2. To the extent possible, close all building doors, windows, and all doors to the room in which the heating
appliance is located. Turn on clothes dryers and any exhaust fans so that they operate at maximum speed. Do
not operate a summer exhaust fan. Also close all fi replace dampers. If after completing steps 3 through 7 it is
believed that suffi
cient combustion air is not available, refer to the National Fuel Gas Code ANSI Z223.1 or any
local codes for proper guidelines.
3. Place the appliance being inspected into operation. Follow the lighting instructions and adjust the thermostat
so that the heating appliance will operate continuously.
4. Determine that the burner is operating properly and that the main burner ignition functions satisfactorily, by
interrupting the electrical power of the appliance in any safely convenient manner. Test the burner safety device
to determine if it is operating properly by extinguishing the pilot or disconnecting the fl ame safety circuit.
Figure 8
Figure 9
P/N 46246300 Rev M 04/20