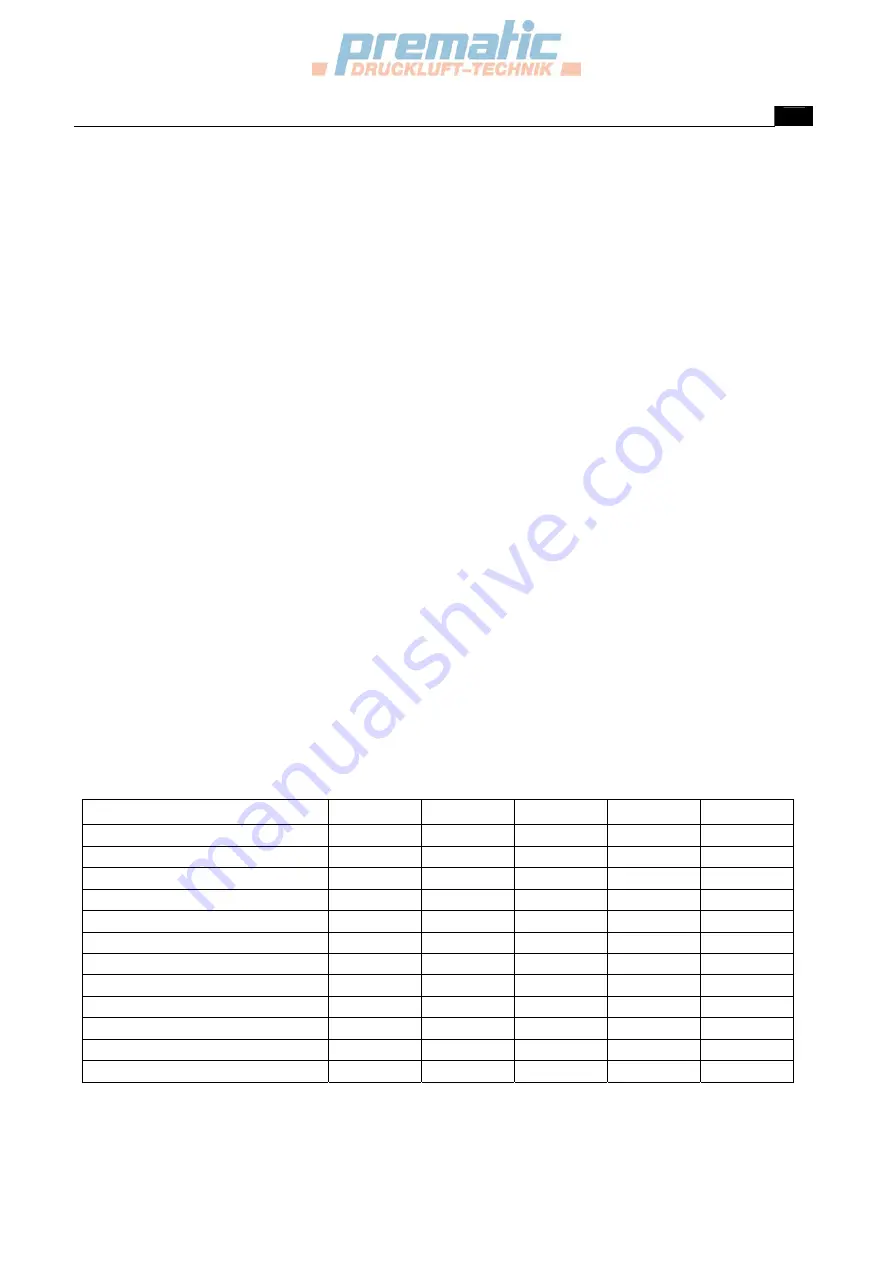
13
GB
NOTE:
The head/cylinder/delivery tube unit can reach high
temperatures. Take care when working near these parts,
and do not touch them to avoid possible burns (fig. 8).
WHAT TO DO IF SMALL MALFUNCTIONS OCCUR
Loss of air in check valve
This trouble depends on poor tightness of the check valve – take
the following action (fig. 11):
– Discharge all pressure from the tank
- Unscrew the hexagon-head of the valve (A)
- Carefully clean both the rubber disk (B) and its seat.
- Refit all parts accurately.
Air losses
These can be caused by poor tightness of a union – check all
unions, wetting them with soapy water.
Compressor turns but does not load
Coaxial compressors: (fig. 12)
-
this may be due to failure of the valves (C1 – C2) or of a seal
(B1 – B2): replace the damaged part.
Pulley drive compressors: (fig. 13)
-
this may be due to failure of the valves F1 and F2 or of a seal
(D1 – D2): replace the damaged part.
-
Check if there is too much condensate water inside the tank.
IMPORTANT
-
Do not on any account unscrew any connection while the tank
is pressurised – always check if the tank is pressure free.
-
Do not drill holes, weld or purposely deform the compressed air
tank.
-
Do not do any jobs on the compressor unless it is off.
-
Temperature in operating ambient: 0
°
C +35
°
C.
-
Do not aim jets of water or inflammable liquids on the
compressor.
-
Do not place inflammable objects near the compressor.
-
Never aim the air jet at people or animals
-
Do not transport the compressor while the tank is pressurised.
-
Be careful with regard to some parts of the compressor such as
the head and delivery tubes, as they can reach high
temperatures. Do not touch these parts to avoid burns.
-
Transport the compressor, lifting or pulling it with the
appropriate grips or handles.
-
Keep children and animals well away from the machine
operating area.
-
If using the compressor for painting:
a. Do not work in closed environments or near to naked flames
b. Make sure there is adequate exchange of air at the place of
work
c. Protect your nose and mouth with an appropriate mask. (fig.
14)
-
Do not put objects or your hands inside the protective grilles to
avoid injury to yourself or damaging the compressor.
-
Do not use the compressor as a blunt object toward things or
animals, to avoid serious damage.
-
When you have finished using the compressor,always switch it
off.
MAINTENANCE
WARNING: Remove the compressed air from the air tank
before performing the maintenance operations.
Allow the compressor to cool before performing
the maintenance operations. Always stop engine
and pull out the spark plug cap to prevent any
sudden start of the engine and remove this
compressed air from the air tank before
performing the maintenance operations.
Read the instruction manual before performing maintenance.
The following procedures must be performed when stopping the
compressor for maintenance or service.
A) Turn off the compressor.
B) Disconnect spark plug wire from engine.
C) Open all drains.
D) Wait for this compressor to cool down before starting service.
1. Cleaning the air intake filter
This filter is designed to clean air coming into the pump
(fig.9). To ensure the pump continually receives clean, cool,
dry air supply this filter must always be clean and ventilation
opening must always be free from obstructions.
WARNING: Never clean filtering element with a flammable
liquid or solvent.
CAUTION: Do not operate without the intake filter.
NOTE:
Replace the filter element when it becomes dirty.
2. Draining
tank:
Gradually open the drain valve, and drain out the air in the
tank. Close tightly when drained.
3. Oil change-oil topping off (fig.10).
4. Maintenance
chart.
MAINTENANCE CHART
PROCEDURE AFTER
USE
DAILY
WEEKLY MONTHLY
200
HOURS
Check pump oil level
X
Oil leak inspection
X
Drain condensation in air tank(s)
X
X
Inspect guards/covers
X
Check for unusual noise/vibration
X
Check for air leaks
X
Clean exterior of compressor
X
Inspect air filter
X
Check safety relief valve
X
Inspect bel tension
X
Change pump oil
X
Replace air filter
X
The pump oil must be changed after the first 50 hours of operation and every 200 hours or 3 months, whichever comes first. Open the pump
oil cock and replace pump oil. As regards the engine, follow instructions in the engine manual. Every 2 years, an Authorized Service
Technician should check the check valve, intake valves and delivery valves.
Prematic AG, Märwilerstrasse 43, 9556 Affeltrangen www.prematic.ch
Tel. 071 918 60 60, Mail: [email protected]