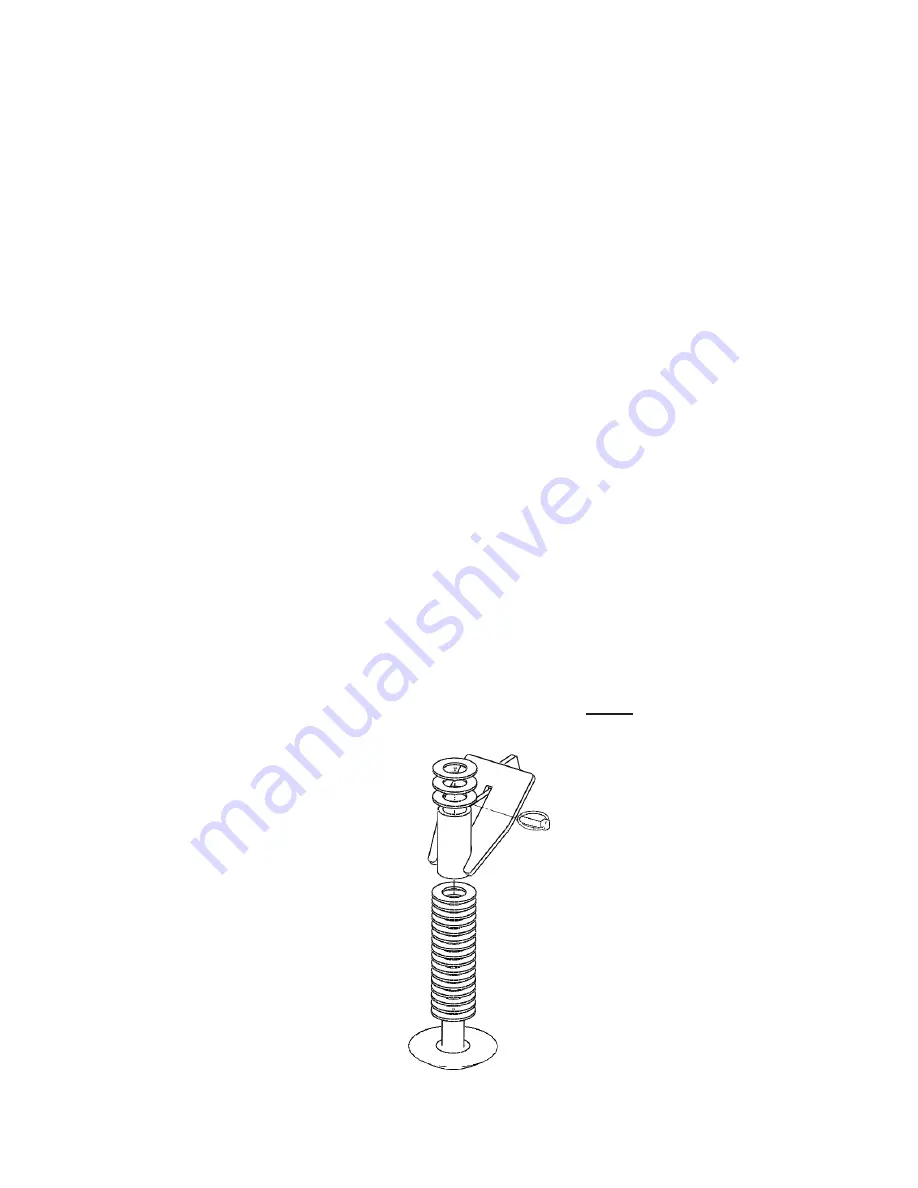
19
OPERATION
Skid Shoe Set-Up
Determine what type of surface is beneath the snow where your blade is being operated.
If the surface is hard and smooth, like concrete or asphalt, the skid shoe placement as shipped from the
factory is correct. (3 spacers on top, 16 on bottom)
If the surface is soft or uneven, then lower the shoe to the desired position (see directions and diagram
below).
Changing the position of the skid shoe :
1. Park the prime mover on a firm, level surface with blade properly attached
2. Lower the blades cutting edge onto a sturdy wood or metal blocking to safely hold the skid shoes 2.5 to
3 inches off the level surface.
3. Place prime mover in “Park” and engage parking brake.
4. Shut off the prime mover’s engine, remove the key and relieve all pressure from hydraulic lines.
5. Remove the lynch pin securing the skid shoe.
6. Adjust the positioning of the spacers to raise or lower the skid shoe.
7. Re-secure the lynch pin.
8. Repeat for the other skid shoe.
NOTICE!
WHEN ADJUSTING THE SKID SHOE, ALL SPACERS MUST BE USED.
Factory Settings
(3 on Top, 16 on Bottom)
Summary of Contents for V-Snow Blade
Page 2: ...2 Notes...
Page 17: ...17 OPERATION figure 2 figure 3 Level Scoop Position Shown...
Page 24: ...24 MAINTENANCE RECORD Date Maintenance Procedure Performed Performed by Comments...
Page 34: ...34 HYDRAULIC ELECTRIC MANIFOLD SCHEMATIC...
Page 35: ...35 HYDRAULIC MANIFOLD SCHEMATIC...
Page 36: ...36 MOLDBOARD ASSEMBLY...
Page 41: ...41 NOTES...