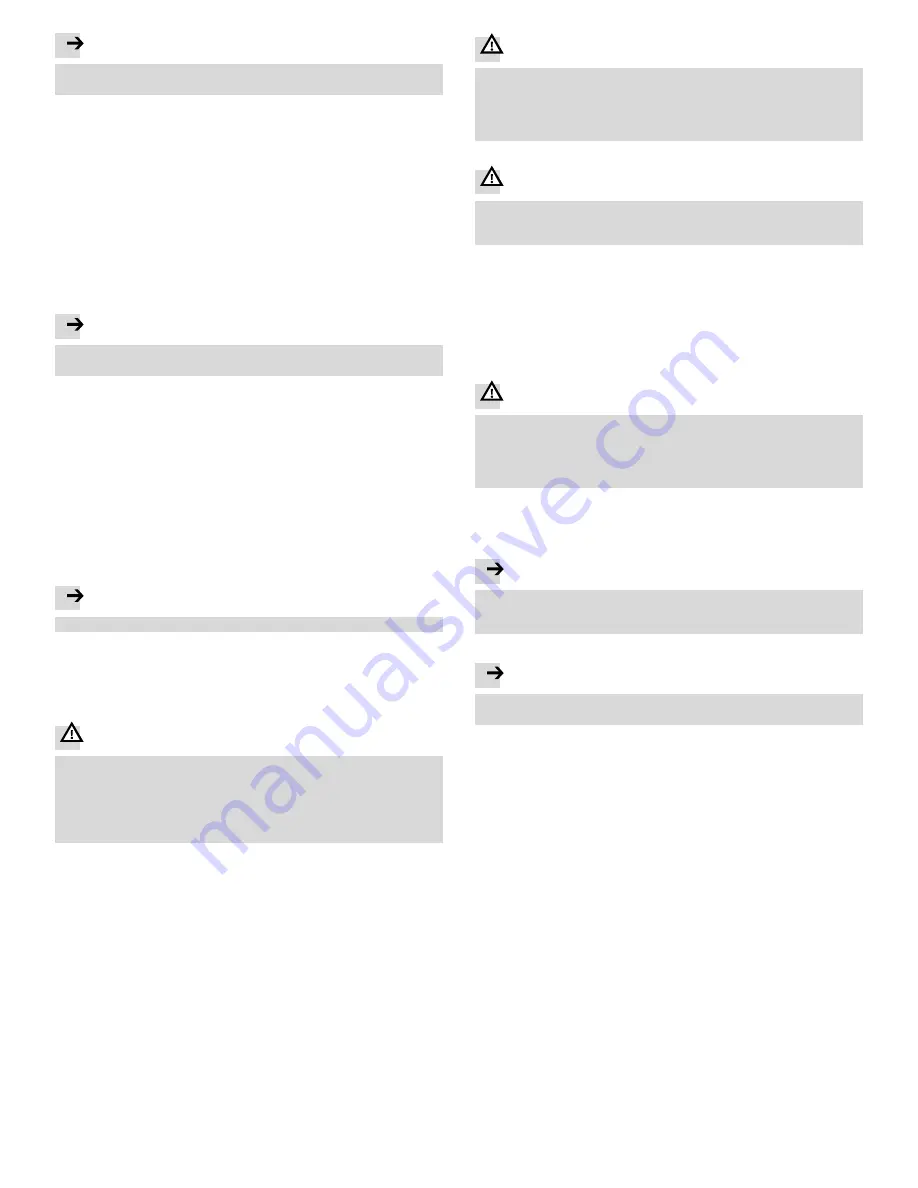
5
Installation
Note
Installation should only be conducted by qualified specialized personnel.
Do not reach into the opening of the valve.
Requirements
– The piping system is unpressurized, and no medium flows in it.
– The lines are clean.
– The lines ends are mounted.
– The system-provided safeguardings are installed (e.g. throttle valve or control
valve, non-return valve, pressure limitation valve).
Clean valve
Remove all transport packaging. The material used in the packaging has been
specifically chosen for its recyclability (exception: oil-impregnated paper = re
sidual waste).
Residues of grease may be evident on the product due to the production process
used.
Clean valve immediately before installation.
Connect medium lines
Note
To eliminate direct access to the valve opening during operation, connect a line
to both ports, even if the valve is located at the end of the piping.
Screw the valve connections to the line.
– Tightening torque 10 Nm.
Connect the line of the operating medium
1. Mount the fitting to the operating medium connection.
– Max. permissible screw-in depth: 3 mm.
2. Connect the line of the operating medium.
3. Make sure that the blanking screw is mounted to the exhaust port.
With ducted exhaust air:
4. Remove the blanking screw at the exhaust port.
5. Connect the piping for the ducted exhaust air to the exhaust port.
– Max. permissible screw-in depth: 3 mm.
6
Commissioning
Note
Commissioning should only be conducted by qualified personnel.
Requirements
– The system-provided safeguardings are installed (e.g. throttle valve or control
valve, non-return valve, pressure limitation valve).
– The valve is fully mounted and connected.
Check operating conditions
Warning
Risk of injury from hot media under pressure!
Dependent on the medium and the operating conditions, pressure peaks that
exceed the permissible pressure range can develop in the system. The valve can
open accidentally and medium can exit.
Do not exceed the maximum permissible medium pressure. In doing so, take
pressure peaks in the system into account.
Check operating conditions and limit values (
è
Technical data).
Check connection points for tightness.
Check compatibility of the devices in the system for maximum pressure (con
sider pressure peaks). If necessary, adjust the application parameters.
Placing valve in operation
1. Add medium.
2. Apply operating pressure to the valve.
è
The valve opens.
7
Operation
Warning
Risk of injury from hot media under pressure!
If the seal cartridge (shut-off element) leaks and the exhaust port is plugged (or
in the case of plugged ducted exhaust air or exhaust air in an equalising
volume), the flow medium can enter the operating medium.
Use only media that will not cause dangerous reactions if mixed.
Warning
Risk of injury due to hot surface!
The valve can become hot at high media temperature.
Do not touch the valve during operation or immediately afterward.
Observe the operating conditions.
Observe permissible limits.
Comply with maintenance conditions (
è
Maintenance and care).
Recommendation: Switch valve several times per day.
After longer standstills:
Actuate the valve several times and check for correct function.
8
Maintenance and care
Warning
Risk of injury from combustion and chemical burns.
The media in the piping system and the valve can be hot and under pressure.
Medium residues can be in the product and escape when open or dismantled.
Allow the valve and piping to cool and depressurize them.
Wear specified protective equipment.
Check and clean valve
Check product regularly from the outside for leakage and function.
Check blanking screw and ducted exhaust air for passage. Remove blockages.
Clean product regularly.
Note
Plan for ducted exhaust air when cleaning the outside. To do this, replace the
blanking screw with a threaded insert or connector (max. permissible screw-in
depth: 3 mm).
Check and replace seal cartridge
Note
Seal cartridge may only be changed by qualified personnel following the mount
ing instructions (
è
Mounting instructions for seal cartridge).
The seal cartridge is subjected to mechanical loads and ageing. A damaged or
worn seal cartridge results in leakage.
Check and replace seals and seal cartridge regularly (intervals dependent on the
medium).
Replace seal cartridge and seals if they are damaged. Use a seal cartridge with
the same specification.
Replacement interval of the seal cartridge: max. ½ million switching cycles.