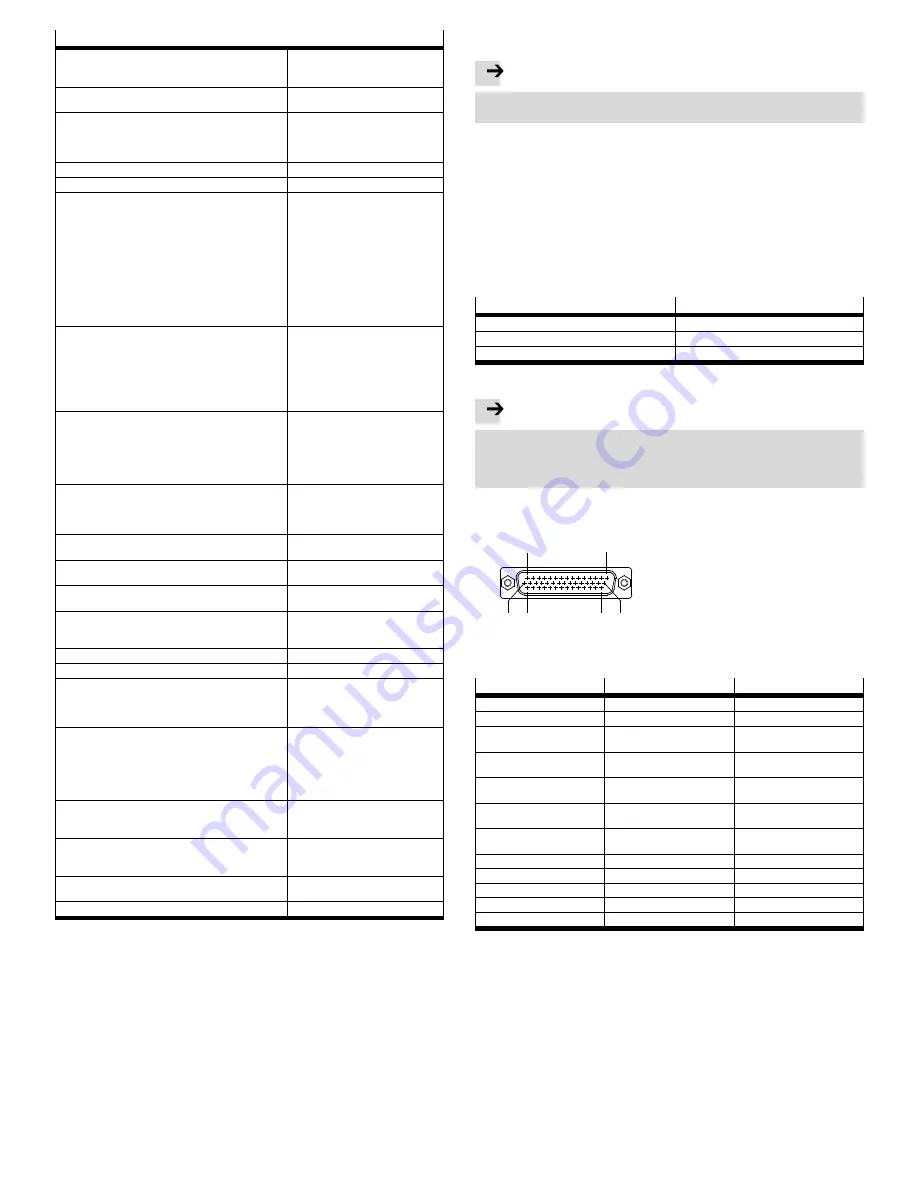
16
Technical data
VTUG-PT-L
Assembly position
– wall mounting
– H-rail mounting
any
horizontal
Ambient temperature
Storage temperature
– 5 … + 50 °C
– 20 … + 60 °C
Operating and pilot medium
Compressed air to ISO 8573-1-2010
[7:4:4]; operation with lubricated me-
dium possible (required during sub-
sequent operation)
Relative air humidity
93 % at 40 °C, non-condensing
Number of valve positions
4 … 24
Operation with external pilot air (IC = ident. code):
Operating pressure:
– 5/3-; 5/2-; 2x 3/2-; 3/2-way valves (IC: B, E, G; J, A, M,
P; VH, VK, VN, VX, VW)
– 2x 3/2-way valve (pneumatic spring) (IC:H, K, N)
-0.9 … 10 bar
1.5 … 10 bar
Pilot pressure
1) 2)
:
– 5/3-, 5/2-way valves (IC: B, E, G, A)
– 5/2-way valve (impulse) (IC: J)
– 5/2-; 3/2-way valve (IC: M, P, VX, VW)
– 2x 3/2-way valve (IC: VH, VK, VN)
– 2x 3/2-way valve with pneumatic spring (IC: H, K, N)
3 … 8 bar
1.5 … 8 bar
2.5 … 8 bar
2 … 8 bar
1.5 … 8 bar
Operation with internal pilot air:
Operating and pilot pressure
2)
:
– 5/3-, 5/2-way valves (IC: B, E, G, A)
– 5/2-way valves (impulse) (IC: J)
– 5/2-; 3/2-way valves (IC: M, P, VX, VW)
– 2x 3/2-way valve (IC: VH, VK, VN)
– 2x 3/2-way valve with pneumatic spring (IC: H, K, D)
3 … 8 bar
1.5 … 8 bar
2.5 … 8 bar
3.5 … 8 bar
1.5 … 8 bar
Tightening torque:
– CTEU.. on electrical interface VAEM-L1-S-...-PTK
– electrical interface
– valve on manifold rail
– blanking screw, blanking plug for pilot air supply
– earthing screw
1.0 Nm (± 10 %)
0.3 Nm (± 20 %)
0.3 Nm (+ 50 %)
1.5 Nm (-20 %)
1 Nm (± 20 %)
Power supply
3)
:
– load voltage (valves)
– load voltage interlock (valves)
– operating voltage (electronics)
reverse polarity protected
24 V DC (± 10 %)
24 V DC (± 10 %)
24 V DC (± 25 %)
Power consumption (load)
– per solenoid coil at nominal voltage
1.0 W 30 ms, then 0.4 W
Max. current consumption through I-port:
– valves / electronics
2.5 A / 0.5 A
Intrinsic current consumption through I-port:
– valves / electronics
40 mA / 30 mA
Current consumption per solenoid coil
– pull current (duration 30 ms)
– holding current
48 mA
16 mA
Mains buffering time (only operating voltage)
10 ms
Test pulse bypass time
š
1 ms (valve supply V
n
+)
I-port/IO-Link connecting cable
– wire cross section (length 0.1 … 5 m)
– wire cross section (length 5 … 20 m)
– max. length
min. 0.25 mm²
min. 1 mm²
20 m (unshielded)
IO-Link properties
– operating Mode
– revision
– data Out
– data In
COM 3 (230.4 kBit)
COM 2 (38.4 kBit)
1.0
6 bytes
4 bytes
Protection class through housing in accordance with
IEC/EN 60529, bus node mounted completely, plug con-
nector inserted or equipped with protective cap
IP40 with corresponding connecting
cable from the Festo range of ac-
cessories
Protection against electric shock (protection against
direct and indirect contact in accordance with
IEC/EN 60204-1)
through the use of PELV circuits
Electromagnetic compatibility
4)
– resistance to interference and emitted interference
Declaration of conformity
(www.festo.com)
Materials
AL, PA, POM, NBR, PU, PC
1)
If the VTUG-... is operated with external pilot air, the pressure of the pilot air must be at least 50 % of
the operating pressure
2)
Reduce your pilot pressure to max. 6 bar if there are more than 12 simultaneously switched valves.
3)
The operating voltage supply is provided via the CTEU bus node or IO-Link Master. The load voltage
supply is provided via the CTEU bus node or, for IO-Link, via a separate feed. Separate fuses are re-
quired for operating and load voltage.
4)
The VTUG... valve terminal is intended for use in an industrial environment. Outside of industrial envir-
onments, e.g. in commercial and mixed-residential areas, actions to suppress interference may have to
be taken
Fig. 8
17
Interlock
The first 16 solenoid coils can be supplied individually through the interlock Sub-D
plug connector. This permits the external release of these valves.
Note
Only mount or remove the interlock Sub-D socket when the power is switched
off.
The interlock can be switched on as follows:
– single-pin through external contacts
– double-pin through safe output terminals. In this case, check the compatibility
of the safe output terminals with the VTUG-PT-L.
All valves of the VTUG-PT-L are supplied with load voltage via the interlock Sub-D
plug connector, even if they are actuated via the bus node. The solenoid coils
17 … 32 and 33 … 48 cannot be supplied individually through the interlock Sub-D
plug connector (
table in section 17.3 and 17.4).
17.1 Sub-D socket
Festo recommends one of the following connecting cables (with sub-D socket)
from Festo for connecting the interlock.
Type
Length of the cable
NEBV-S1G44-K-2.5-N-LE44-S6
2.5 m
NEBV-S1G44-K-5-N-LE44-S6
5 m
NEBV-S1G44-K-10-N-LE44-S6
10 m
Fig. 9
Note
Please observe the following when using a sub-D socket from another manufac-
turer:
– the sub-D socket must not exceed a max. width of 16.5 mm
– connect the cable screening to the plug housing
17.2 Pin allocation of the interlock plug connector (sub-D 44 pin)
The subsequent figure shows the position of the pins in the interlock plug connect-
or on the VTUG-PT-L.
Pin 31
Pin 44
Pin 1
Pin 15
Pin 16
Pin 30
Fig. 10
For controlling the valves, each solenoid coil (referred to as coil or SP in the tables)
is assigned to two specific pins of the interlock Sub-D plug connector:
Pin
1)
Coil
Signal
2)
1 … 3
—
24 V
VAL/OUT
4 … 6
1 … 48
0 V
VAL/OUT
7
8
1
1
V
1
+
V
1
–
9
10
2
2
V
2
+
V
2
–
11
12
3
3
V
3
+
V
3
–
13 … 36
…
V
n
+
V
n
–
37
38
16
16
V
16
+
V
16
–
39
17 … 32
V
17…32
+
40
33 … 48
V
33…48
+
41 … 43
1 … 48
0 V
VAL /OUT
44
—
not connected
Housing
FE
FE
1)
Pins 7 … 38 provide individual control of the solenoid coils 1 … 16 of the interlock
2)
Do not use V1…16– and Vn– with single-pin interlock interface
Fig. 11