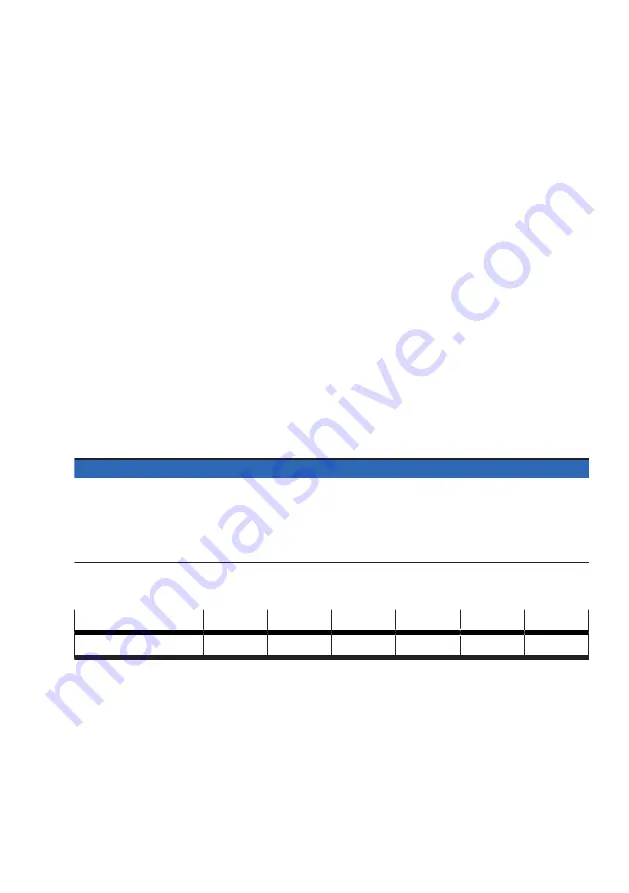
Festo — PDAD — 2022-02i
Installation
21
6
Installation
6.1
Pneumatic installation
Connecting the dryer
Use only compressed air lines that are resistant to the diffusion of moisture from the environment,
e.g. stainless steel tubing or hose type PEN, PLN or PFAN.
Requirements:
–
The dryer is fully assembled and set up in compliance with the operating conditions.
–
The micro filter MS6-LFM is mounted.
–
The multi-way distributor is mounted with the input and output at the desired position.
1. Screw the connection fitting or piping into the threaded connection of the micro filter.
–
Maximum screw-in depth for thread in accordance with ISO 228: 12.0 mm
–
Maximum screw-in depth for NPT thread: 10.3 mm
2. Only for PDAD-...-N:
Screw the included NPT adapter with sealing ring into the output of the dryer.
–
Tightening torque for NPT 3/8: maximum 15 Nm
–
Tightening torque for NPT 1/2: maximum 18 Nm
3. Screw the connection fitting of the piping into the output of the dryer.
6.2
Power supply connection
The device can be operated with alternating current (AC) or direct current (DC). A separate, marked
connection is available for both types of current. Only one power source may be connected.
NOTICE
Destruction of internal electronics
A supply voltage connected to the wrong connection can destroy the internal electronics.
• Connect the supply voltage to the specified connection only.
• Use only the correspondingly marked power supply socket from the scope of delivery.
• Cover the unused connection with the cover.
The device does not have an integrated fuse at the power input. An external fuse is required at the
power connection of the device.
Supply voltage
12 V DC
24 V DC
100 V AC
115 V AC
230 V AC
240 V AC
Current consumption
0.8 A
0.4 A
0.16 A
0.14 A
0.07 A
0.067 A
Tab. 12: Current consumption depends on the supply voltage
•
Protect the power supply with a suitable external fuse depending on the supply voltage and the
current consumption of the device.
A suitable main switch or safety switch must be installed near the adsorption dryer. The switch must
be easily accessible. The switch must be marked for the adsorption dryer and the on/off position must
be stated. The cables must meet the requirements of EN 61010-1 for reinforced insulation.
A special power supply socket is supplied for each type of current. The power supply sockets have a
different number of contacts for mechanical coding.