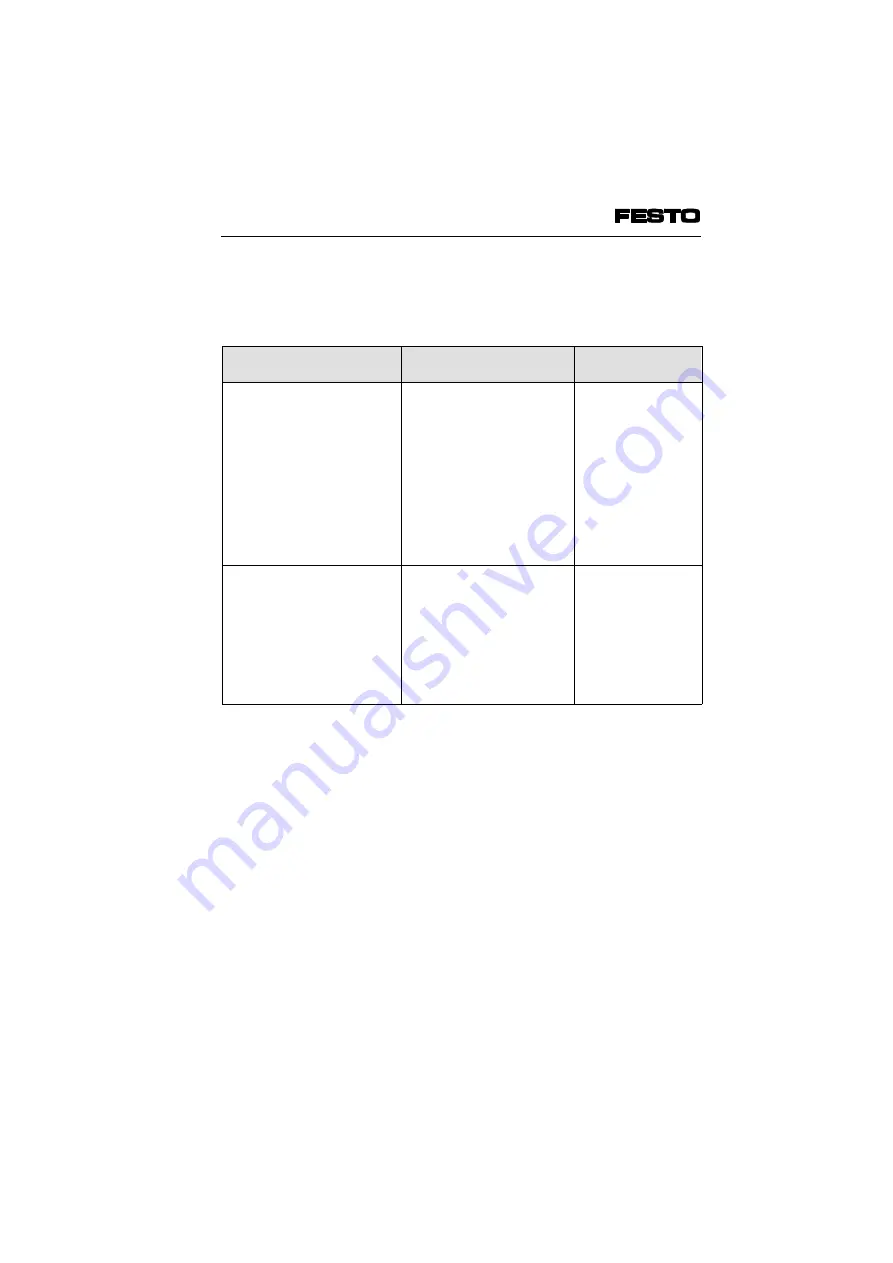
The specifications on configuration depend on
the size of the valve terminal used. This is
shown in the following table:
Fieldbus slave
Meaning
Number of
assigned I/Os
Valve terminal
●
with 4 valve locations
●
with 6 and 8 valve
locations
●
with 10 and 12 valve
locations
●
with 14 and 16 valve
locations
Module with 8 digital
outputs
Module with 16 digital
outputs
Module with 24 digital
outputs
Module with 32 digital
outputs
1 output
2 output bytes
3 output bytes
4 output bytes
Valve sensor terminal
●
with 4 and 6 valve
locations
●
with 8 and 10 valve
locations
●
with 12 and 14 valve
locations
Module with 14 digital
inputs/outputs
Module with 22 digital
inputs/outputs
Module with 30 digital
inputs/outputs
2 Input/output
bytes
3 Input/output
bytes
4 Input/output
bytes
Fig. 5/1: Number of assigned I/Os
VIFB11 - 02 5. Commissioning
5-8
9902d
Summary of Contents for IIFB11-02 Series
Page 2: ......
Page 4: ...Order no 164590 Title MANUAL Designation P BE VIFB11 02 GB VIFB11 02 II 0503f ...
Page 6: ...VIFB11 02 IV 0503f ...
Page 7: ...1 USER INSTRUCTIONS VIFB11 02 1 User instructions 9902d 1 1 ...
Page 15: ...2 SYSTEM STRUCTURE VIFB11 02 2 System structure 9902d 2 1 ...
Page 23: ...3 TECHNICAL DESCRIPTION VIFB11 02 3 Technical description 0503f 3 1 ...
Page 41: ...4 1 FITTING THE VALVE TERMINAL VALVE SENSOR TERMINAL VIFB11 02 4 Installation 9902d 4 1 ...
Page 45: ...4 2 INSTALLING THE PNEUMATIC COMPONENTS VIFB11 02 4 Installation 9902d 4 5 ...
Page 61: ...4 3 INSTALLING THE ELECTRONIC COMPONENTS VIFB11 02 4 Installation 0503f 4 21 ...
Page 96: ...VIFB11 02 4 Installation 4 56 9902d ...
Page 97: ...5 COMMISSIONING VIFB11 02 5 Commissioning 9902d 5 1 ...
Page 100: ...VIFB11 02 5 Commissioning 5 4 9902d ...
Page 159: ...6 DIAGNOSIS AND ERROR TREATMENT VIFB11 02 6 Diagnosis and error treatment 9902d 6 1 ...
Page 173: ...APPENDIX A DEVICENET SPECIFICATIONS VIFB11 02 A DeviceNet Specifications 9902d A 1 ...
Page 189: ...APPENDIX B ACCESSORIES DEVICENET COMPATIBILITY VIFB11 02 Appendix B 9911e B 1 ...
Page 202: ...VIFB11 02 Appendix B B 14 9911e ...
Page 203: ...APPENDIX C INDEX VIFB11 02 Appendix C 9902d C 1 ...
Page 204: ...VIFB11 02 Appendix C C 2 9902d ...
Page 210: ...VIFB11 02 Appendix C C 8 9902d ...