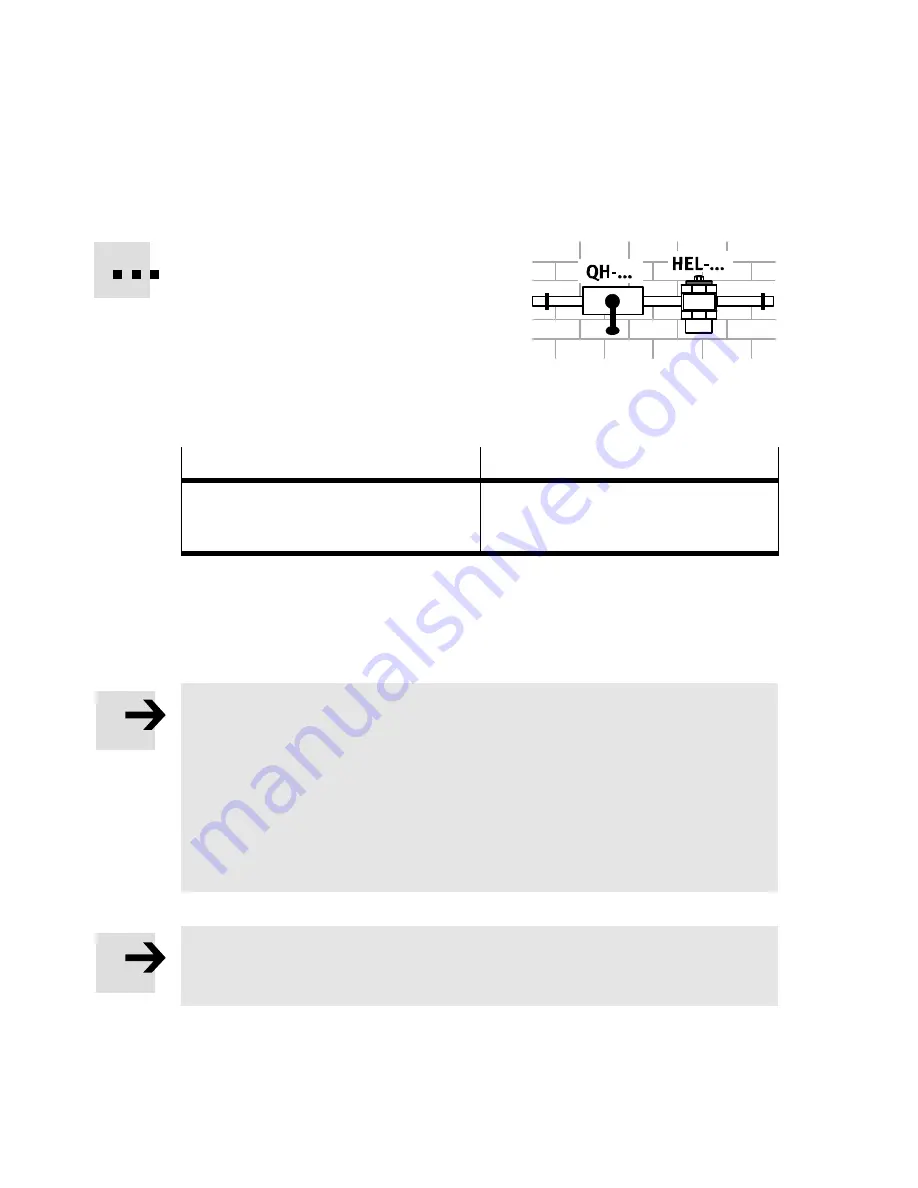
HSP-...-AP/A S
Festo HSP-...-AP/AS 2017-10b English
8
S
Slowly pressurize the complete system.
To do this use start-up valve type HEL-... /
HEM-....
S
Check to see if the following are
necessary:
a compensation reservoir type VZS-...
a non-return valve type HGL-...
This will reduce fluctuations in the
pressure.
In this way you can prevent the work load
from sliding down if there is a sudden drop
in pressure.
6
Fitting
Please note
Note especially the following when fitting all the components:
‒ Screw connections must be fitted free of offset and mechanical tension.
‒ Screws must be fitted accurately (otherwise threads will be damaged).
‒ The specified torques must be observed.
‒ Contact surfaces must be clean (avoid leakage and contact faults).
Observe also the installation instructions supplied with modules and compo
nents ordered at a later stage.
Please note
For the type HSP-...-...WR/WL: Please observe the warnings and instructions in
the operating instruction for the BWR-/BWL-HSP-...
Fig. 6