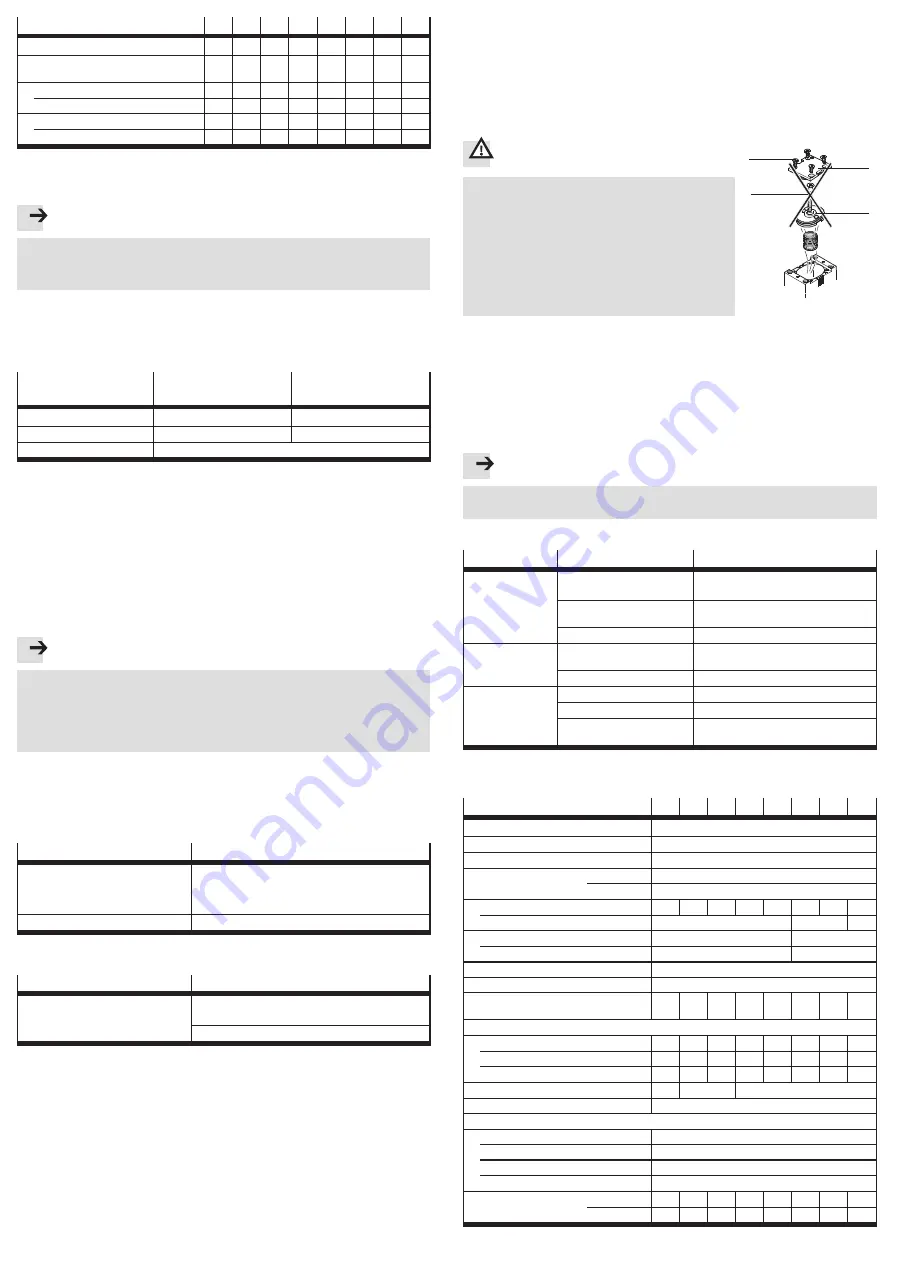
Size
16
20
25
35
40
50
63
80
Fitting hole
∅
[H8] centring pin
[mm]
2
3
4
4
5
6
6
8
Fitting hole
∅
[H8] centring
sleeve
aB
[mm]
5
5
7
7
9
12
12
12
Screw for mounting from above
aA
M2.5 M3
M4
M4
M5
M6
M6
M8
Tightening torque
[Nm]
0.8
1.2
3
3
6
10
10
24
Screw for mounting from below
aC
M3
M4
M5
M5
M6
M8
M8
M10
Tightening torque
[Nm]
1.2
3
6
6
10
24
24
47
Fig. 6
4
Installing the pneumatic system
Note
Dirt in the connections can impair functioning.
• Make sure that the connections and tubing are free from dirt particles and
foreign matter.
• Check whether an HGL non-return valve is required. In this way you can prevent
the work load from sliding down if there is a sudden drop in pressure.
• Connect the tubing of the HGPD to the compressed air connections
(
11 Technical Data).
Gripping type
(working load)
External gripping
Internal gripping
Connection
6
(Fig. 1)
Open
Close
Connection
5
(Fig. 1)
Close
Open
Connection
4
(Fig. 1)
Sealing air (max. 0.5 bar)
Fig. 7
If using long and heavy gripper fingers:
• Use a one-way flow control valve GRLA directly at the compressed air supply
ports. These determine the opening and closing time (and therefore the bearing
loading) of the gripper fingers.
If short and light gripper fingers are used, the restrictors built into the gripper
eliminate the need for an additional, external restrictor. (
Catalogue specifica-
tions under www.festo.com/catalogue).
5
Commissioning
Note
• Observe the permitted values (
catalogue specifications) for:
– the maximum gripping force (dependent on the holding force and holding
point)
– the permissible weight force of the gripper fingers depending on the opening and
closing time. The weight force of the gripper fingers should be calculated.
Setting the opening/closing time for long and heavy gripper fingers:
• First tighten the restrictor screws of the up-stream GRLA:
– completely,
– then loosen one turn.
• Start a test run using the specified sequence:
Test run
Tests
Without load
– Correct assignment of the compressed air connec-
tions
– Permitted gripper speed
– Secure function of the proximity sensors
With load
– Load is gripped firmly
Fig. 8
1. Listen to the knocking of the piston:
Piston stop: Soft
Piston stop: Hard
Continue test run with steps 2 and 3
Unscrew the resistors one turn.
The maximum gripping speed is reached.
Finish the test run
Fig. 9
2. Unscrew the restrictor screws of the up-stream GRLA one turn.
3. Repeat steps 1 and 2 until the desired gripper speed has been reached.
4. Finish the test run.
5. Exhaust the gripper.
6
Operation
• Avoid the HGPD coming into contact with the following:
– contaminated media
– grinding dust
– glowing sparks or chips.
These will damage the HGPD.
7
Service and maintenance
• Grease the HGPD after 5 million switching cycles at the lubrication nipple.
Permitted grease is Molycote BR2 plus (if necessary, twist the supplied
lubrication nipple into the port
4
).
• If the product is dirty, clean the exterior with a soft cloth.
The permitted cleaning agent is soap suds, max. +60 °C.
8
Disassembly and repair
Warning
(U)
(R)
(T)
Fig. 10
(S)
Danger of injury from parts flying through the air!
Preloaded springs inside the HGPD-…-G… may
release suddenly during dismounting.
• Please ensure that the piston/cap is preloaded to
1400 N.
• Secure the end cap (T) with a holding device when
loosening the screws (U) [HGPD-…-G1].
• Secure the piston (R) with a holding device when
loosening the screw (S) [HGPD-…-G2].
• For disassembly, exhaust the system and the product.
• Recommendation: Send the product to our repair service.
This ensures that special attention will be paid to the necessary fine adjust-
ments and inspections.
• Information on spare parts and aids can be found under:
www.festo.com/spareparts
9
Accessories
Note
• Please select the appropriate accessories from our catalogue
www.festo.com/catalogue
10
Eliminating malfunctions
Malfunction
Possible cause
Remedy
Gripper cannot hold
load firmly
Supply pressure too low
Increase supply pressure (up to max.
permitted value)
Centre of pressure of gripper
finger too far outwards
Shift centre of pressure inwards
Mass too large
Select larger gripper
Proximity sensor
does not
show gripper status
Proximity sensor not adjusted
Check position and calibration of
proximity sensor
Wire break
Replace proximity sensor
Gripper does not
open/close
No compressed air
Checking the compressed air supply ports
Gripper defective
Return HGPD to Festo
Too much grease in the
gripper
Briefly open hole
4
and clock the
gripper once
Fig. 11
11
Technical data
Size
16
20
25
35
40
50
63
80
Mode of operation
Double-acting parallel grippers
Operating medium
Filtered compressed air, lubricated or unlubricated
Mounting position
Any
Operating pressure
–
[bar]
3 … 8
G…
[bar]
4 … 8
Pneumatic connection (lateral)
5
/
6
M5
M5
M5
M5
M5
G
Á
G
Á
G¼
Tightening torque
[Nm]
1.5
10
15
Pneumatic connection (underneath)
1
M3
M5
Tightening torque
[Nm]
0.7
1.5
Ambient temperature
[°C]
+5 … +60
Storage temperature
[°C]
–20 … +80
Maximum force on the gripper jaw
Fz stat.
[N]
150
250
500
750
1200 2000 3000 6000
Maximum torque on gripper jaw, static
Mx
[Nm]
8
12
30
40
70
90
120
170
My
[Nm]
4
7
25
30
45
60
80
130
Mz
[Nm]
3
6
15
25
35
50
65
110
Repetition accuracy
[mm]
.
0.03
.
0.04
.
0.05
Max. interchangeability
[mm]
.
0.2
Information on materials
Housing, cover
Aluminium, anodised
Screws, end cap
Stainless steel
Gripper jaw
Hardened steel
O-ring, piston seals
Nitrile rubber
Product weight
–
[kg]
0.1
0.16
0.33
0.57
1.04
1.77
3.37
6.25
G…
[kg]
0.12
0.18
0.36
0.68
1.22
2.15
4.00
7.48
Fig. 12