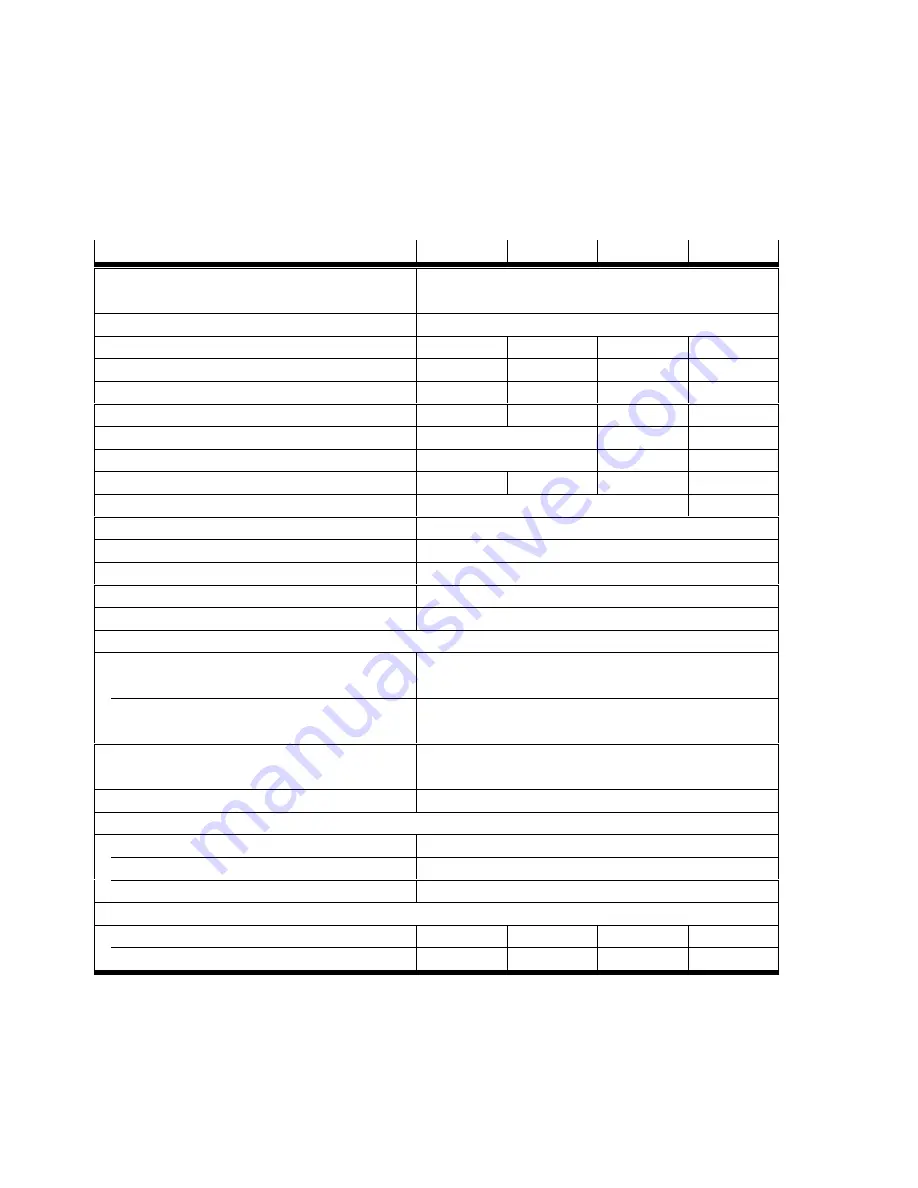
ERMO
14
Festo – ERMO – 2017-11a English
12
Technical data
12.1
Mechanical data
Size
1)
12
16
25
32
Design
Electromechanical rotary drive with stepper motor
and integrated gear unit
Mounting position
Any
Max. axial force
[N]
180
290
350
450
Max. radial force
[N]
200
300
450
550
Nominal torque
2)
[Nm]
0.15
0.8
2.5
5
Holding torque
[Nm]
0.33
0.8
4
7
Nominal rotary speed
[rpm]
100
66
50
Max. speed
[rpm]
200
150
100
Permissible mass moment of inertia
[kgcm
2
]
3
13
65
164
Repetition accuracy
[°]
±0.05
±0.1
Torsional backlash (new)
[°]
0.2
Ambient temperature
[°C]
0 … +50
Storage temperature
[°C]
–20 … +60
Relative air humidity
[%]
0 … 85 (non-condensing)
Degree of protection
IP40
Vibration and shock resistance
Vibration
in accordance with IEC 60068-2-6:2007-12
0.15 mm, 10 ... 58 Hz
20 m/s
2
, 58 … 150 Hz
Shock
in accordance with IEC 60068-2-27:2008-02
150 m/s
2
, 11 ms
Continuous shock
in accordance with IEC 60068-2-27:2008-02
150 m/s
2
, 6 ms
Note on materials
Contains paint-wetting impairment substances
Materials
Housing, clamping ring, rotary table
Anodised aluminium
Sealing ring
NBR
Ball bearing, screws
Steel
Product weight
Without brake
[kg]
0.475
0.90
1.35
2.20
With brake
[kg]
–
0.96
1.50
2.38
1)
The PositioningDrives engineering software is available for sizing (
è
www.festo.com/sp).
2)
Theoretical torque at nominal rotary speed
Tab. 8