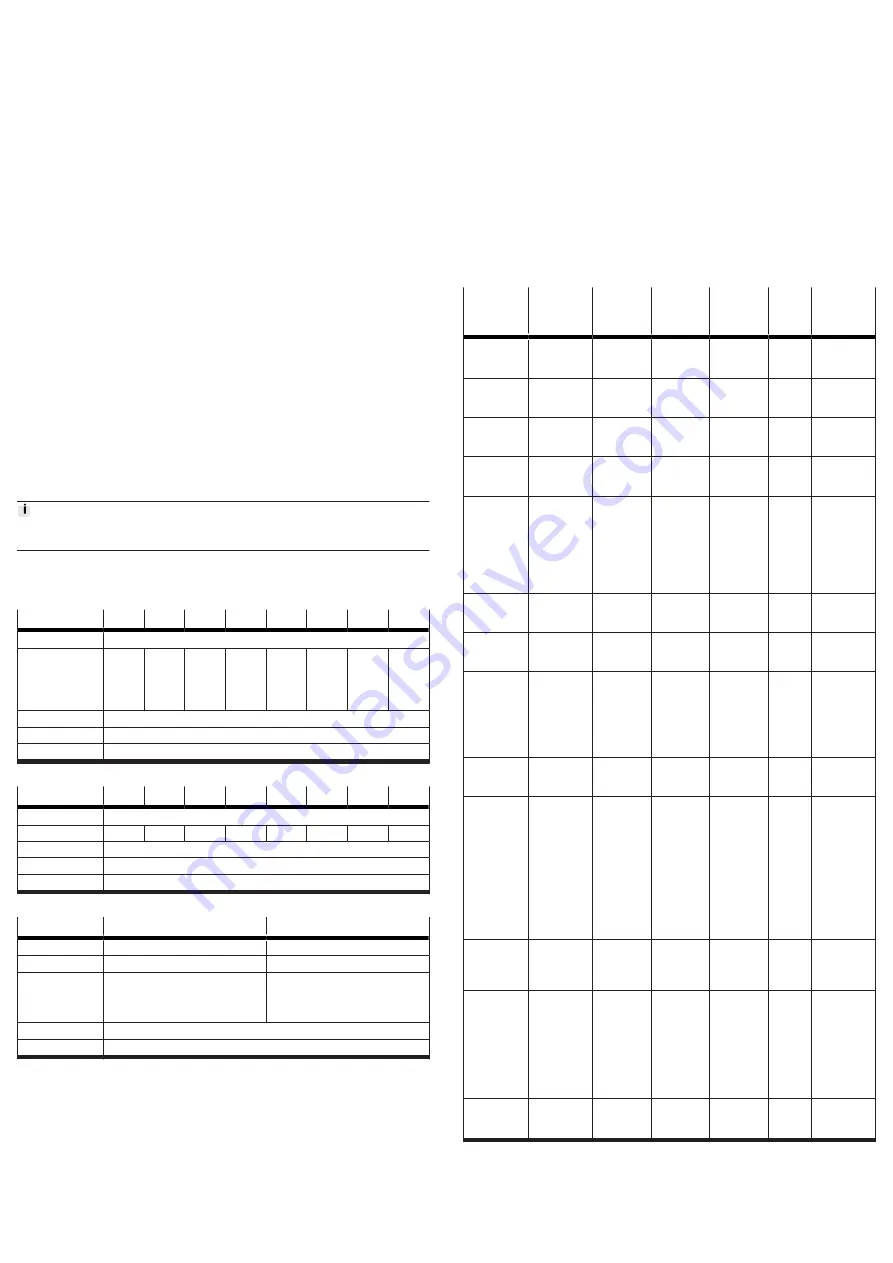
‘ResetDirectionFlag’ (bit 50)
The gripper stores the last travelled direction. After the ‘Close’ command, the
‘Open’ command must follow and vice versa. If, for example, it is necessary to
move the jaws in the same direction when changing a workpiece, the direction
flag ‘DirectionOpenFlag’ or ‘DirectionCloseFlag’ can be reset via the ‘ResetDirec-
tionFlag’ command. Then a movement in the previous direction is possible again.
‘TeachGrippingPosition’ (bit 51)
–
‘WorkpieceNo = 0’
This command is not possible for the ‘WorkpieceSet= 0’.
–
‘WorkpieceNo
>
0’
The stored parameter‘GrippingPosition’ in the ‘WorkpieceSet’ can be written
by this command. The ‘ActualPosition’ value on execution of ‘TeachGrippingPo-
sition’ is transferred to the ‘GrippingPosition’ parameter of the selected ‘Work-
pieceSet’.
Reaching of this gripping position can be checked in the ‘StatusWord’ with the
‘GrippedPositionFlag’ marker.
‘FindNewEndPositions’ (bit 55)
If required (for example in the case of reduced installation space), the end posi-
tions can be redefined with this command so that the desired layers are returned
with the ‘ClosedPositionFlag’ and ‘OpenedPositionFlag’ flags in the ‘StatusWord’.
This command ‘FindNewEndPositions’ moves the gripper open-close and open
again. From the open position, the gripper moves exclusively closed-open. The
minimum and maximum values approached in this way are transferred to the
internal memory as new end positions.
The positions are reset by executing the command again, whereby the gripper can
again move its maximum stroke without a previous stop.
‘Open’ (bit 56)
With this command, the gripper moves the jaws to the outer position (opening).
‘Close’ (bit 57)
With this command, the gripper moves the jaws to the inner position (closing).
‘ResetError’ (bit 63)
With this command, safety-relevant errors can be acknowledged and the gripper
can be switched back to operational status.
Individual errors cannot be reset by the user. The reset is performed automatically
as soon as the specified operating conditions are met again.
10.7
Process Data IN
The gripper transmits data cyclically. This allows the gripping process to be moni-
tored.
Bit
47
46
45
44
43
42
41
40
Process data
‘StatusWord’
Data content
‘Error’
‘Direc-
tionClo-
seFlag’
‘Direc-
tionO-
pen-
Flag’
‘Latch-
DataOk
’
‘Unde-
fined-
Posi-
tionFla
g’
‘Close-
dPosi-
tion-
Flag’
‘Grip-
pedPo-
sition-
Flag’
‘Open-
edPosi-
tion-
Flag’
Value range
0 … 65535
Index
0x0028
Data type
UIntegerT16
Tab. 12: Process data IN
Bit
39
38
37
36
35
34
33
32
Process data
‘StatusWord’
Data content
–
‘Ready’
–
–
–
–
–
–
Value range
0 … 65535
Index
0x0028
Data type
UIntegerT16
Tab. 13: Process data IN
Bit
31 … 16
15 … 0
Meaning
MSB … LSB
MSB … LSB
Process data
‘ErrorNumber’
‘ActualPosition’
Value range
0 … 65535
0 … max. jaw stroke
–
EHPS-16: 0 … 2150
–
EHPS-20: 0 … 2750
–
EHPS-25: 0 … 3350
Index
0x0028
Data type
UIntegerT16
Tab. 14: Process data IN
10.7.1
Description ‘StatusWord’
‘Ready’ (bit 38)
Active as soon as the gripper is raised. It can also be used to check a byte swap.
‘OpenedPositionFlag’ (bit 40)
Active when the open position is reached. In the case of a previous redefinition of
the end position, the bit always becomes active when the gripper has reached this
stored position or is further opened.
‘GrippedPositionFlag’ (bit 41)
Active, if the gripper is in the taught-in or predefined gripper position, taking into
account the predefined tolerances.
‘ClosedPositionFlag’ (bit 42)
Active when the gripper has reached the closed position. In the case of a previous
redefinition of the end position, the bit always becomes active when the gripper
has reached this stored position or is further closed.
‘UndefinedPositionFlag’ (bit 43)
Active if the gripper is in an undefined position.
‘LatchDataOk’ (bit 44)
Active as soon as the transmitted data has been transferred from the gripper.
‘DirectionOpenFlag’ (bit 45)
This bit is a direction flag and becomes active if the last run command was from
the ‘Open’ master.
‘DirectionCloseFlag’ (bit 46)
This bit is a direction flag and becomes active if the last run command was from
the ‘Close’ master.
‘Error’ (bit 47)
Active if there is an error. The present errors can be viewed in the ‘ErrorNumber’
and ‘ErrorMessage’ parameters.
10.8
Device-specific parameters
Index
Subindex
Name
Descrip-
tion
Value
(example
)
Lengt
h
[byte]
Format
0x0018
‘Applica-
tionSpeci-
ficTag’
Text to be
defined by
the user
***
32
StringT
0x0040
‘Status-
Word’
1)
0x0041
‘Error-
Number’
1)
0x0042
‘Cycle-
Counter’
Counter for
gripping
cycles
0 … 429496
7295
4
UIntegerT32
0x0043
‘Tempera-
ture’
Gripper
tempera-
ture in °C
If the
gripper
<
tempera-
ture is 0 °C,
0 is output.
0 … 65535
2
UIntegerT16
0x0044
‘Control-
Word’
1)
0x0045
‘ErrorMes-
sage’
Outputs an
error
description.
64
StringT
0x0046
‘ErrorCount’ Counter of
error mes-
sages
2
UIntegerT16
0x0100
‘ActualPosi-
tion’
1)
0x0101
‘Gripping-
Position’
2)
Gripper
position
e.g. for
checking
the work-
piece
dimensions
0 … nominal
stroke (+tol-
erance)
–
EHPS-16:
0 … 215
0
–
EHPS-20:
0 … 275
0
–
EHPS-25:
0 … 335
0
2
UIntegerT16
0x0102
‘Workpie-
ceNo’
1)
Workpiece
number of a
workpiece
set
0 … 32
1
UIntegerT8
0x0103
‘Gripping-
Mode’
2)
Driving
mode
–
Invalid: 0
–
Universal:
100
–
External
gripping:
60
–
Internal
gripping:
70
1
UIntegerT8
0x0104
‘Gripping-
Tolerance’
2)
Tolerance of
‘Gripping-
Position’
0 … 255
1
UIntegerT8