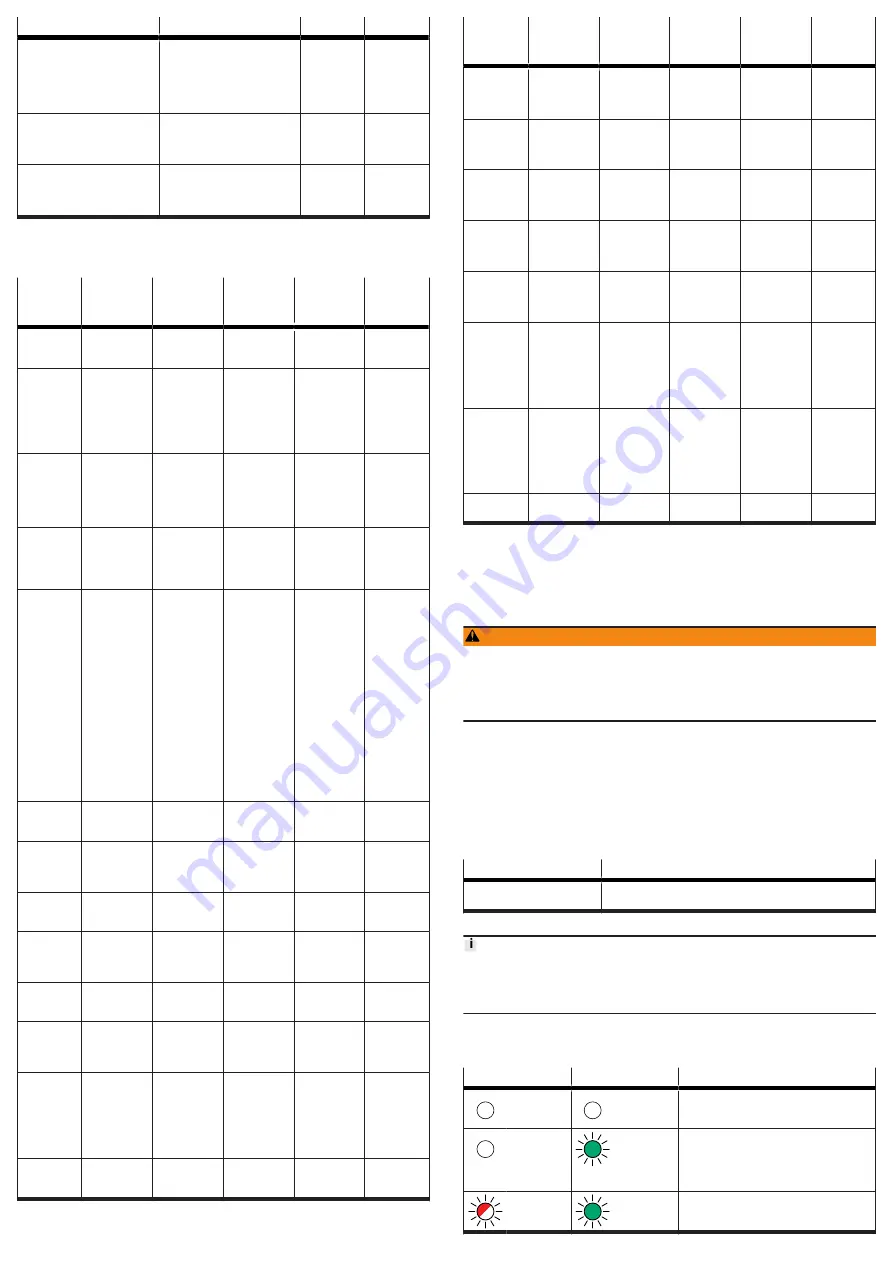
Name
Description
Index
Value
[Enable Gripper]
Activation of system commands
for easy triggering of movement
commands. A standard configu-
ration is thus loaded into the
parameters and the movement
commands are released.
0x0002
160
[Close Gripper]
With previous release, this com-
mand can initiate a movement of
the gripper jaws in the direction
of "closing".
0x0002
161
[Open Gripper]
With previous release, this com-
mand can initiate a movement of
the gripper jaws in the direction
of "opening".
0x0002
162
Tab. 23: System Commands
10.12
Fault clearance IO-Link
Parameter ‘ErrorNumber’
Diagnostic
message
Hex (Dec)
Device
status
Error
Possible
cause
Remedy
‘Error-
Count’
1)
0x0 (0)
‘Status ok,
device is
ready’
No
0x100 (256)
Outside the
specification
‘Power supply
error’
–
Actuator
supply not
connected
–
Cable break
–
Actuator
supply not
sufficient
Testing the
actuator
supply voltage
Yes
0x101 (257)
Outside of
specification
(drive can no
longer be
moved)
‘Temperature
too high’
–
Ambient
tempera-
ture too
high
–
Gripper has
overload
Ensure ade-
quate pressuri-
sation/
cooling/
connection
Yes
0x102 (258)
Outside of
specification
(drive can no
longer be
moved)
‘Temperature
too low’
Ambient tem-
perature too
low
Ensure suffi-
cient operating
temperature
Yes
0x010A
(266)
)
Outside the
specification
‘Actuator
under voltage
during move-
ment’
–
Actuator
supply
unstable
–
Line resist-
ance
increased
(faulty
supply
cable)
–
Power
supply not
sufficiently
designed
for peak
loads,
faulty
supply
cables
–
Check grip-
ping force,
check
power
supply and
peak load
–
Manual
acknowl-
edgement
of error
message
necessary
No
0x300 (768)
Outside the
specification
‘ControlWord
not plausible’
Incorrect value
in ‘Control-
Word’
Checking the
value in the
‘ControlWord’
No
0x301 (769)
Outside the
specification
‘GrippingPosi-
tion not plau-
sible’
Incorrect value
in parameter
‘GrippingPosi-
tion’
Check the
parameter
‘GrippingPosi-
tion’
No
0x302 (770)
Outside the
specification
‘GrippingForce
not plausible’
Incorrect value
in parameter
‘GrippingForce’
Check the
parameter
‘GrippingForce’
No
0x304 (772)
Outside the
specification
‘GrippingToler-
ance not plau-
sible’
Incorrect value
in parameter
‘GrippingToler-
ance’
Check the
parameter
‘GrippingToler-
ance’
No
0x305 (773)
2)
Failure
‘Reference
position error’
Gripper has no
reference posi-
tion
Service Festo
SE & Co. KG
Yes
0x306 (774)
Outside the
specification
‘GrippingMode
not plausible’
Incorrect value
in parameter
‘Gripping-
Mode’
Check the
parameter
‘Gripping-
Mode’
No
0x307 (775)
Motion task
cannot be exe-
cuted
‘Drive com-
mand cannot
be executed’
Multiple travel
commands in
the same
direction
Reset ‘Reset-
DirectionFlag’
direction flag
or send move-
ment com-
mand in the
other direction
No
0x308 (776)
Outside the
specification
‘WorkpieceNo
not plausible’
Incorrect value
in parameter
‘WorkpieceNo’
Check the
parameter
‘WorkpieceNo’
No
Diagnostic
message
Hex (Dec)
Device
status
Error
Possible
cause
Remedy
‘Error-
Count’
1)
0x309 (777)
Outside the
specification
‘GrippingPosi-
tion not
latched’
Process data
sent by the
master have
been changed
Transfer of the
changed
parameters by
‘LatchData.’
No
0x30D (781)
Outside the
specification
‘GrippingForce
not latched’
Process data
sent by the
master have
been changed
Transfer of the
changed
parameters by
‘LatchData.’
No
0x30F (783)
Outside the
specification
‘GrippingToler-
ance not
latched’
Process data
sent by the
master have
been changed
Transfer of the
changed
parameters by
‘LatchData.’
No
0x310 (784)
Outside the
specification
‘GrippingMode
not latched’
Process data
sent by the
master have
been changed
Transfer of the
changed
parameters by
‘LatchData.’
No
0x311 (785)
Outside the
specification
‘WorkpieceNo
not latched’
Process data
sent by the
master have
been changed
Transfer of the
changed
parameters by
‘LatchData.’
No
0x312 (786)
Outside the
specification
‘Initial hand-
shake missing’
After a cold
start, a single
data migration
by ‘LatchData’
(‘ControlWord’
= 1) is
required.
Transfer of the
changed
parameters by
‘LatchData.’
No
0x400
(1024)
3)
Failure
‘Gripper
blocked’
–
Gripper is
difficult to
move
–
The travel
path of the
grab is
impaired
–
Restore the
free move-
ment of the
gripper
–
Service
Festo
SE & Co. KG
Yes
0x406 (1030) Failure
‘System error /
internal error’
Internal
system error
Service Festo
SE & Co. KG
Yes
1) Incrementing the "ErrorCount" parameter for these messages
2) No homing required
3) Acknowledge error with "ResetError"
Tab. 24: "ErrorNumber" parameter
11
Maintenance
11.1
Safety
WARNING
Danger of crushing due to unexpectedly fast-moving loads and unintentional
movements.
• Remove the payload.
• Switch off power to the product.
• Safeguard the power supply from being switched on again unintentionally.
11.2
Cleaning
Clean the product with a soft cloth. Do not use aggressive cleaning agents.
For use with reduced particle emission:
–
Remove abrasion and contamination from the product on the following
schedule:
–
Prior to initial commissioning.
–
Regularly during operation.
11.3
Lubrication
Interval
Maintenance work
After 5 million switching cycles
Grease the guide of the gripper jaws. Permissible lubricating
grease
Tab. 25
Cut the lubrication interval by half if one of the following applies:
• High thermal stress
• Heavy contamination
• Proximity of grease-dissolving liquids or vapours
12
Malfunctions
12.1
Diagnostics
LED red ‘Error’
LED green ‘Ready’
Meaning
off
off
–
IO-Link Supply voltage is not connected
è
IO-LinkCommunication not active.
off
green light
Actuator ready for operation (Fallback, SIO
Mode)
–
IO-Link Supply voltage: connected
–
IO-Link Communication: not active
–
Actuator supply voltage: connected
flashing red
green light
–
IO-Link Supply voltage: connected
–
IO-Link Communication: not active
–
Actuator supply voltage: not connected