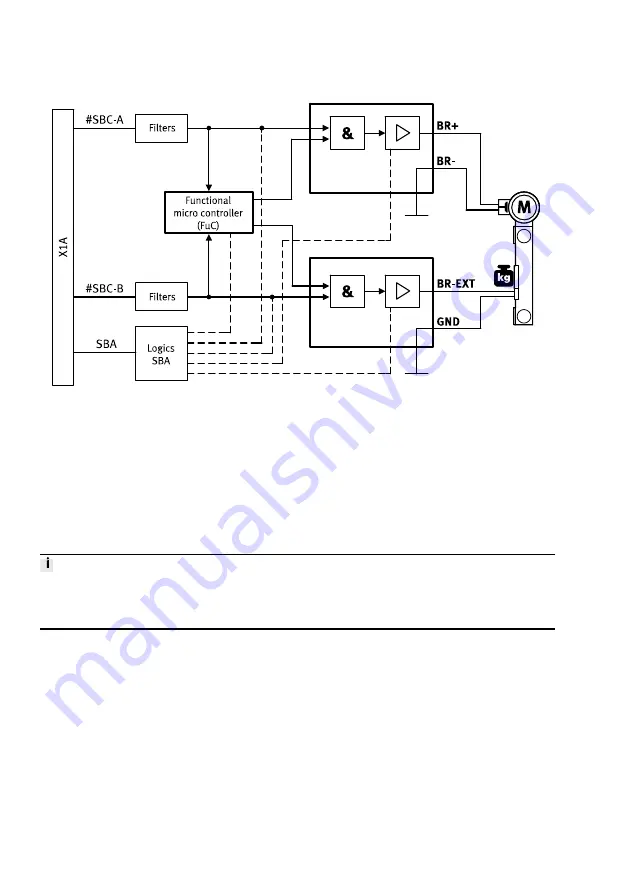
Fig. 6 Functional principle SBC
SBC request
The SBC safety function is requested over 2 channels by switching off the control voltage at both con-
trol ports #SBC-A and #SBC-B:
–
The #SBC-A request switches off the power to the signals BR+/BR-.
–
The #SBC-B request switches off the power to the signal BR-EXT.
If there is a power failure in the logic voltage supply of the servo drive, power is also cut off to the
brake outputs.
After a request of SBC and subsequent cancellation, the safe brake control is only energised when the
functional microcontroller enables the holding brake. This ensures that z-axles with a suspended load
can be restarted without the load dropping.
SBC feedback through SBA diagnostic contact
The 2-channel switching of the brake is displayed over the SBA output. Through SBA, the status of the
SBC safety function is reported for diagnosis, such as to an external safety relay unit.
The SBA diagnostic output displays whether the safe status has been reached for the SBC safety func-
tion. It is set if the following two conditions are fulfilled:
–
Switching off of both brake outputs is requested (#SBC-A = #SBC-B = low level)
–
The internal diagnostic functions have determined that there is no internal error and both brake
outputs are de-energised (switched off).
At the same time, test impulses occurring at SBC-A and SBC-B are not filtered. The diagnostic output
SBA therefore supplies high level for the duration of these low test impulses.
Check of the SBC safety function
Product overview
12
Festo — CMMT-AS-...-S1 — 2018-02