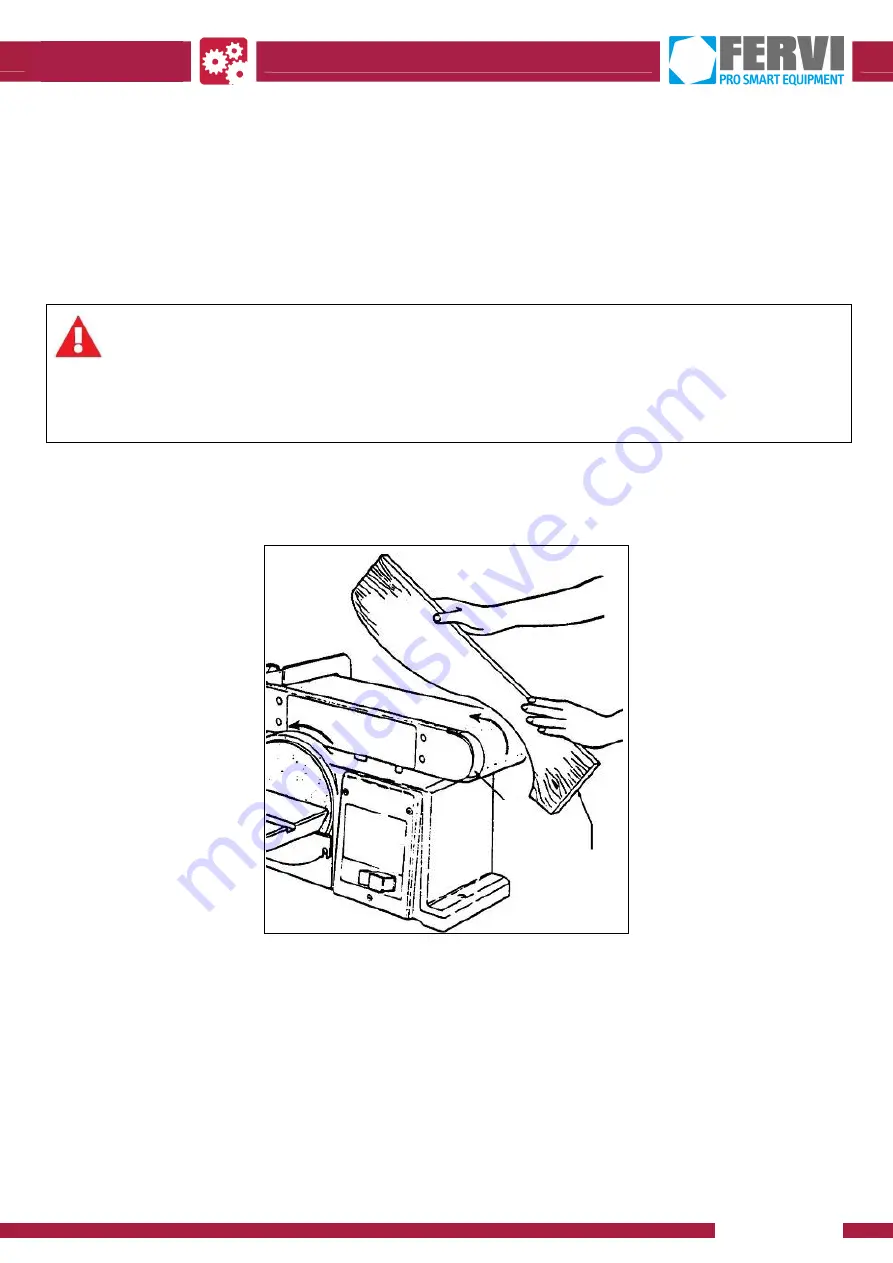
MACHINES AND
ACCESSORIES
Page 31 of 41
10.5Sanding of curved surfaces
To perform the sanding of curved surfaces, with the horizontal belt proceed as follows:
1. Press the green button to start (Figure 15).
2. Support the workpiece to be sanded on the edge of the abrasive belt, at the part with
the idle roller (Figure 20).
3. Slightly move the workpiece during sanding, taking great care not to touch the disc
with your fingers or hands.
4. After processing, turn off the machine by pressing the red stop button (see Figure 16).
Figure 19 – Sanding of curved surfaces.
Risk of knocks and accidents
Do not sand the end of the piece by resting it on the idle roller.
This could cause the ejection of the piece upwards, with the consequent risk of injury.
Workpiece
Drive roller
fervi.com