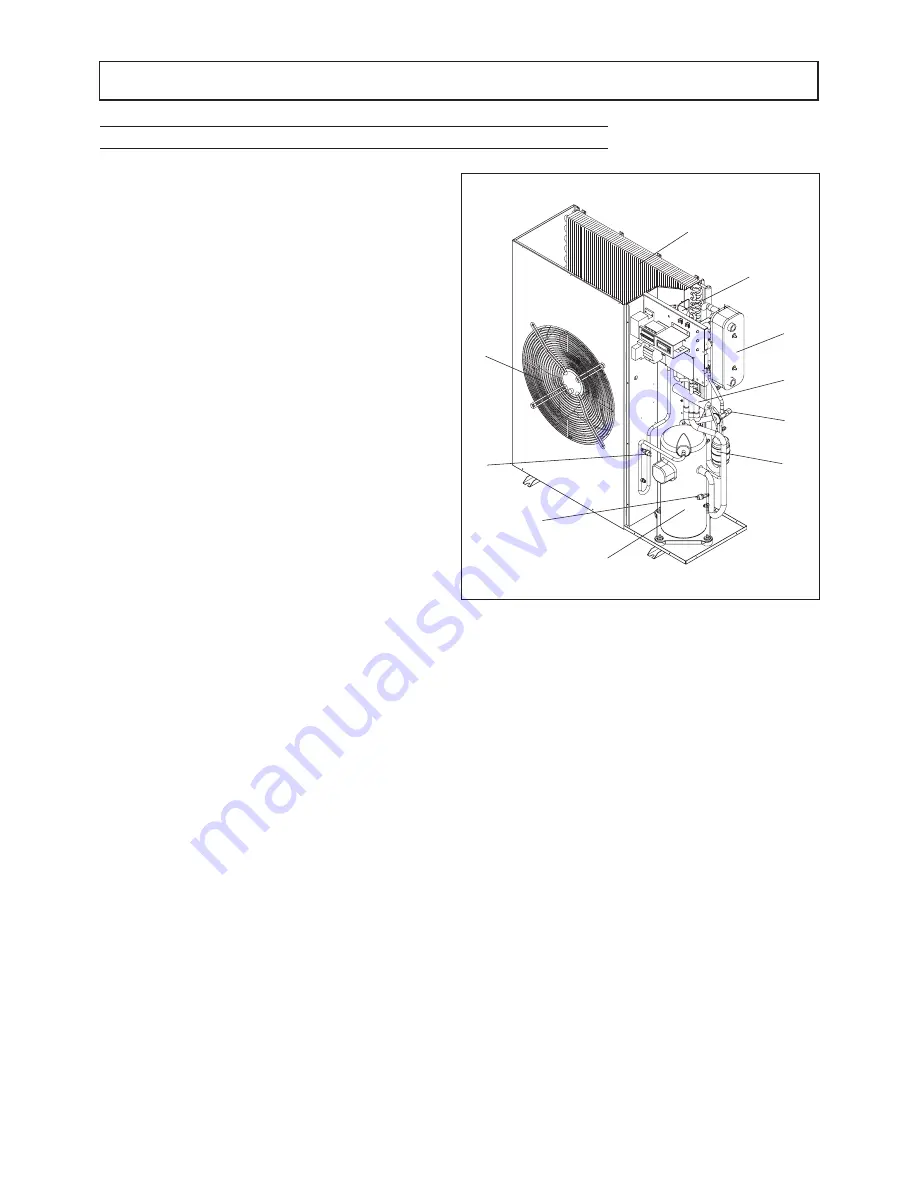
6
GENERAL FEATURES
Description of parts
The
supporting structure (1)
, base and external panelling are
made from hot galvanised steel sheet, painted with epoxy
powers (colour RAL 7035) to ensure good resistance to
atmospheric agents.
The axial-type fans with curved profile blades
(2)
are housed in
a sheet casing and are complete with safety grille. Fan speed
is controlled in a continuous way by a phase cut device that
allows the condensing pressure (in cooling) and evaporation
pressure (in heating) to be controlled according to the value
read by the temperature probe on the liquid line.
The rotary type hermetic
compressor (3)
(models 6 or 7) or
scroll (models 9, 11, 14 and 17) is complete with
overtemperature and overcurrent protection. It is fixed to the
base by means of rubber vibration dampers and placed in a
compartment separate from the air flow to facilitate
maintenance and control operations. To prevent reverse
compressor rotation on all the units with three-phase power
supply, a device that controls the presence and correct
sequence of the power phases is fitted. Units in heat pump
version have a heating element that is activated when the
compressor switches off, to keep the compressor crankcase oil
temperature high enough to prevent migration of the refrigerant
during winter stops and to evaporate any liquid present in the
crankcase, in order to prevent possible liquid rushes on
starting.
The braze-welded stainless steel plate-type exchanger
on the
user side (4)
is adequately insulated to prevent the formation
of condensate and to limit heat loss to the outside. It is protected against the risk of ice forming by an antifreeze heating element
activated according to the water temperature and by a differential pressure switch that detects a possible lack of water flow.
The
external side exchanger (5)
comprises a finned coil with grooved copper pipes arranged in an equilateral shape and
aluminium fins with notched profile to increase the heat exchange coefficient. A tray is obtained in the base for collecting the
condensate produced during heating operation.
The lamination part
comprises a thermostatic valve
(6)
with external equaliser that allows the unit to adjust to the various
operation conditions, keeping the set level of overheating constant.
The refrigerant circuit of each unit is also complete with :
-
hermetic dehydrator filter
with solid cartridge
(7)
: it catches residuals of impurities and any traces of moisture in the circuit;
-
high pressure switch (8)
: with fixed setting and manual reset;
-
low pressure switch (9)
: with fixed setting and automatic reset (it becomes manual only in case of frequent activations);
-
4-way reverse cycle valve (10)
: it allows the switching of operation mode, reversing the refrigerant flow (for units in heat pump
version only);
-
liquid receiver (11)
: it compensates the variation in refrigerant charge required with the change of operation mode (for units in
heat pump version only);
-
pressure test points (12)
SAE 5/16” (UNF 1/2” - 20) complete with pin, seal and blind union, as required for the use of
refrigerant R410A. They enable a complete check of the refrigerant circuit : compressor inlet pressure, compressor delivery
pressure, pressure upstream of the thermostatic valve and pressure losses on the dehydrator filter.
1
2
3
10
9
5
4
6
7
8
Summary of Contents for RXA
Page 1: ...RXA AIR WATER CHILLERS AND HEAT PUMPS WITH AXIAL FANS TECHNICAL MANUAL...
Page 2: ...2...
Page 4: ...4...
Page 20: ...Cod 3QE23691...