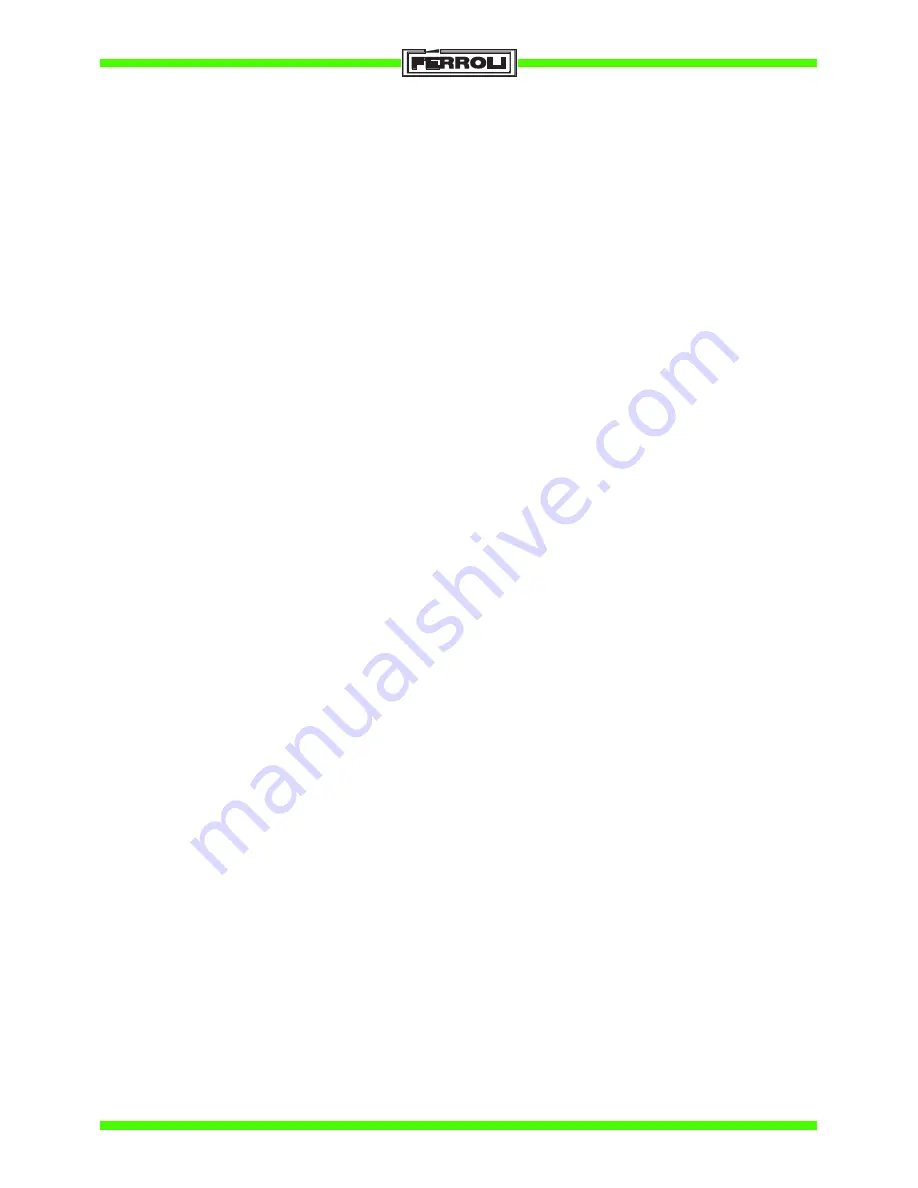
11
S.p.A.
4.05 Temporary shut-down
To temporarily shut down the boiler, just position the main switch 6 on the “0” position.All the
electrical part remain not energized and only the pilot burner remain alight.
4.06 Prolonged shut-down
Push the button 4 (fig 6), turn clockwise the knob 1 (fig 7a) or turn the knob 1 in the position “C” (Fig.
7b). By measn this operations the gas connection to main burner and pilot is cut out. Close the gas
cock upstream from the boiler and turn off the electricity supply to the boiler.
Note: If the boiler is not used for long periods in the winter, to avoid frost damage, either add antifreeze
to the system or drain completely.
4.07 Post ignition checks and controls
On igniting the boiler for the first time:
Check there are no gas or water leaks.
Check that pilot flame is well regulated eventually it can be adjusted by means of adjustment screw
on the gas valve (fig 6 ,7a, 7b).
Check the boiler ignites properly by using the regulating thermostat to ignite and shut down the
boiler.
Check flue efficiency during boiler operation.
Check that the fuel consumption indicated on the meter corresponds to the value indicated in the
table.
Check that water circulates correctly between the boiler and system.
Check that flue connection between boiler and chimney is properly sealed.
IMPORTANT:
The pilot burner inspection hatch must remain closed during normal boiler operation.
4.08 Gas consumption
The rated gas flow is shown on the technical-table at pag. 6. To get the rated gas-flow the gas pressure
has to be adjusted according the technical data sheet. Gas pressure calibration can be carried out by-
means of proper screw (fig 6,7a,7b) After the gas adjustment the consumption can be verified by
means of gas-meter after at least 5 min. operation at full output. Further small adjustment can be
carried on the gas adjustment screw (fig 6,7a,7b).
5. Gas conversion
The following adjustment and conversion operations must be carried out by qualified personnel
only. s sAs standard the boilers are calibrated for N.G.
5.01 From N.G. to L.P.G.
To convert from N.G. to L.P.G., replace the main and pilot burner nozzles then adjust main burner
pressure to ensure that nozzle pressure is as indicated for L.P.G.
Note: Nozzle diameters and main burner pressures are given in technical data tables.
Summary of Contents for Rendimax 16 CE
Page 19: ...19 S p A...