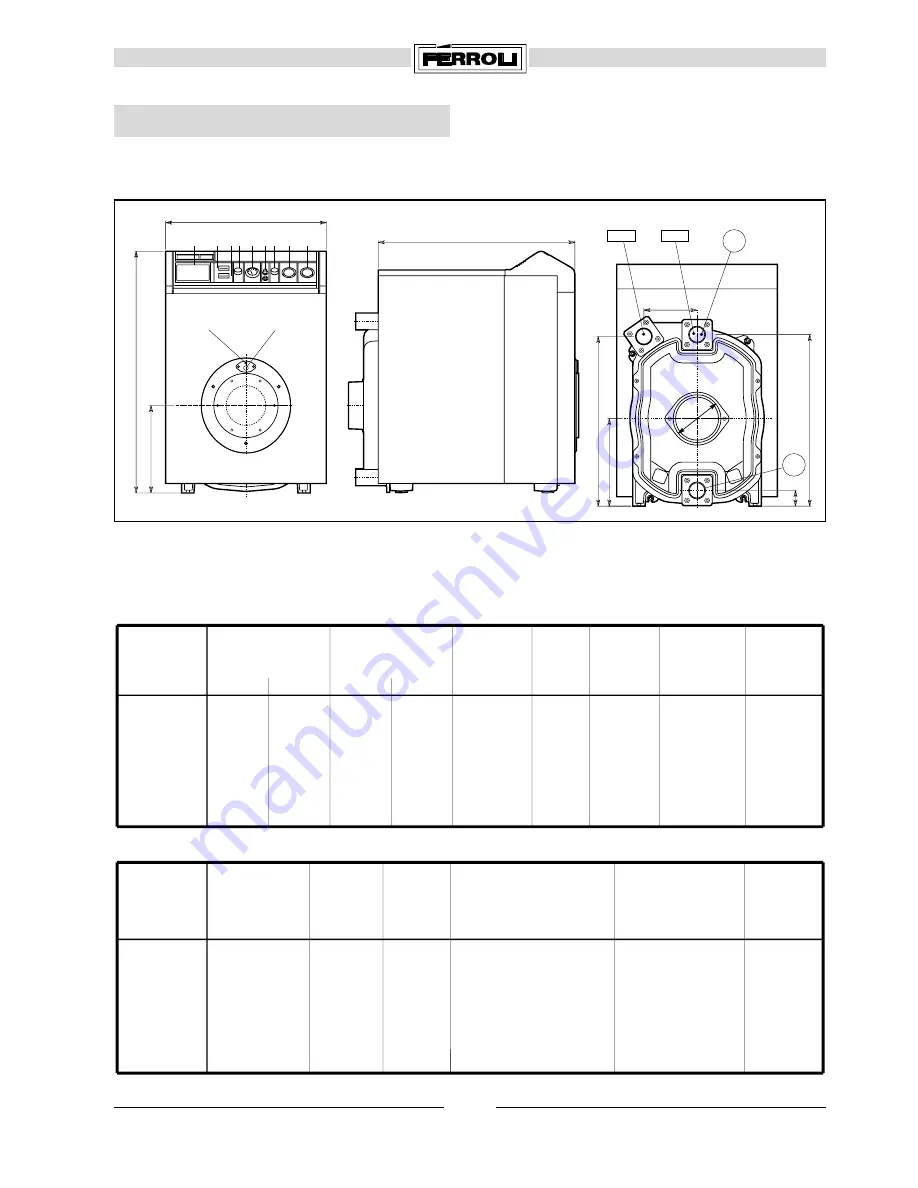
5
GN4
CHARACTERISTICS
Technical specifications (ill. 3)
fig. 3
Key
1. Electronic control unit (optional)
2. Burner 1st stage operation hour meter
3. Burner 2nd stage operation hour meter
4. Burner lock warning light
5. Boiler thermometer
6. Safety thermostat
1
7
A2
2
3 4
5
6
8
9
11
10
A1
B2
B1
850
A
463
1279
898
908
83
463
281.5
Ø D
7
8
9
10
11
12
13
14
N
°
elements
217
270
324
388
452
516
600
695
Max.
200
250
300
360
420
480
560
650
Max.
heat output
kW
Delivered heat output
kW
4
4
4
4
4
4
4
4
Operating
pressure
bar
1040
1170
1300
1430
1560
1690
1820
1950
A
mm
840
950
1060
1170
1280
1390
1500
1610
Body
weight
kg.
Combustion chamber
pressure drop
∆
p mbar
0,5
0,8
0,7
1,0
1,4
1,7
2,6
3,5
120
150
180
215
250
290
330
390
Min.
128
160
192
229
266
309
352
416
Min.
Model
GN4.07/200
GN4.08/250
GN4.09/300
GN4.10/360
GN4.11/420
GN4.12/480
GN4.13/560
GN4.14/650
180
180
250
250
250
250
250
250
D
Ø
Water
pressure drop
∆
p mbar
∆
t 20
°
20
30
42
54
65
77
88
100
Model
GN4.07/200
GN4.08/250
GN4.09/300
GN4.10/360
GN4.11/420
GN4.12/480
GN4.13/560
GN4.14/650
143
163
183
203
223
243
263
283
Water
content
dm
3
880
1010
1140
1270
1400
1530
1660
1790
Length of
combustion
chamber
L mm
500
500
500
500
500
500
500
500
Dimensions of
combustion
chamber
Ø mm
172
198
220
250
270
300
325
350
Combustion
chamber
volume
Ø mm
7. Burner switch and indicator light
8. Burner 2nd stage regulation thermostat
9. Burner 1st stage regulation thermostat
10. Pressure inlet fitting in combustion chamber
11. Inspection window for flame control
A1. Central heating flow outlet DN 80 - 3" gas
A2. Central heating return inlet DN 80 - 3" gas
B1. Low temperature central heating flow outlet DN 80 - 3" gas
B2. Low temperature central heating
return inlet DN 80 - 3" gas
Summary of Contents for GN4 N
Page 2: ...2 GN4 ...
Page 27: ...27 GN4 ...