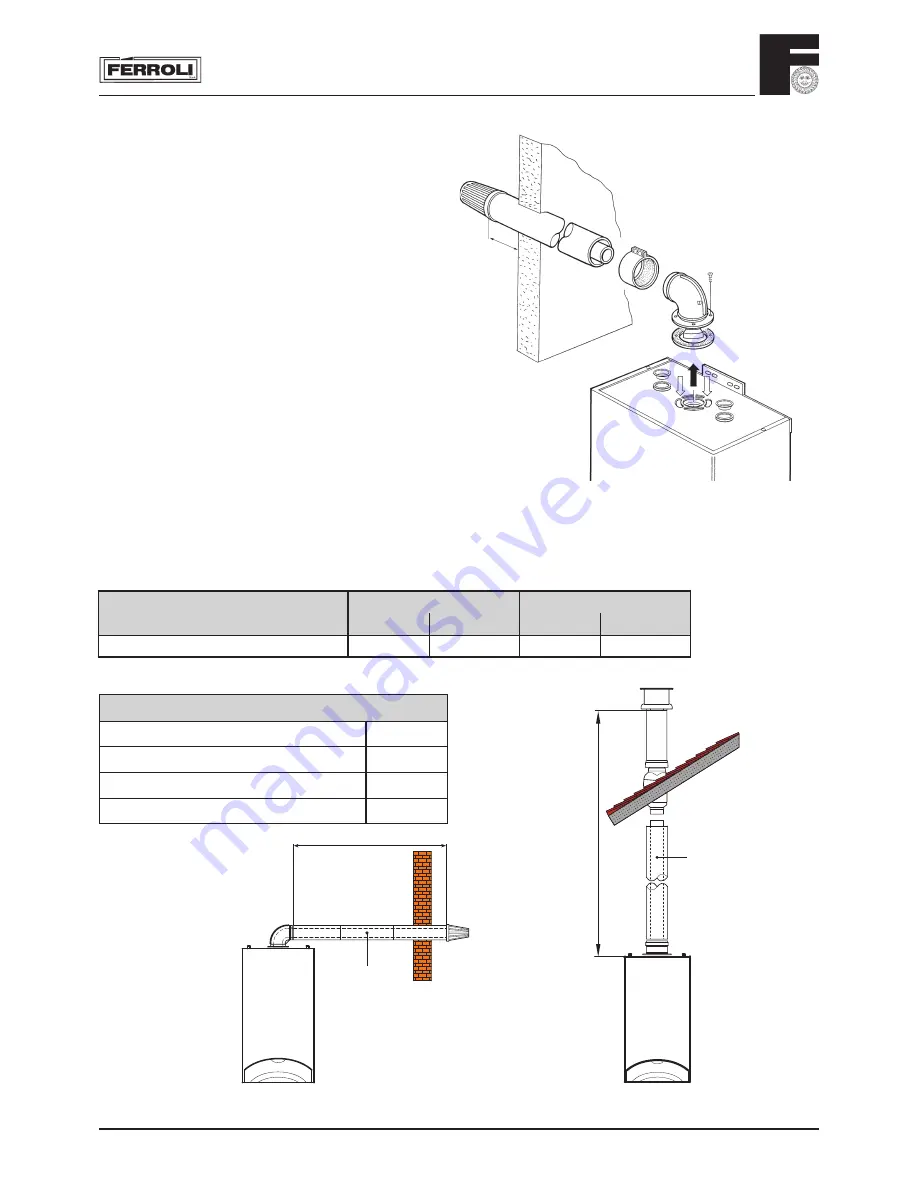
DOMINA 80 E
29
Fig. 21
Notes on concentric horizontal installation
To locate the centre of the hole for passing
the pipes through the wall, refer to fig. 15.
Bear in mind that the two concentric pipes
must slope downwards away from the boiler
at a rate of about 3 mm/m to avoid rainwater
entering the boiler. The concentric pipes
making up the air - flue gas duct must be
sealed with the gasket where they join the
boiler (fig. 21). Outside, the pipes should
protrude from the wall between 10 and 60
mm (fig. 21).
Between
10-60mm
3.07.3 Maximum concentric flue length
First table below shows the maximum flue lengths available for boilers with concentric systems.
For correct calculation remember to include the reduction for bend and flue terminals listed on second
table. Please refer to 3.06 for use of restrictor
e
l
b
i
s
s
i
m
r
e
p
t
h
g
n
e
l
e
u
l
f
m
u
m
i
x
a
M
c
i
r
t
n
e
c
n
o
c
m
m
0
0
1
c
i
r
t
n
e
c
n
o
c
m
m
5
2
1
l
a
c
i
t
r
e
V
*
l
a
t
n
o
z
i
r
o
H
l
a
c
i
t
r
e
V
*
l
a
t
n
o
z
i
r
o
H
E
0
8
a
n
i
m
o
D
m
4
m
3
m
5
m
5
s
l
a
n
i
m
r
e
t
f
o
o
r
d
n
a
d
n
e
b
r
o
f
n
o
i
t
c
u
d
e
R
°
0
9
d
n
e
b
c
i
r
t
n
e
c
n
o
c
m
m
0
0
1
m
1
°
5
4
d
n
e
b
c
i
r
t
n
e
c
n
o
c
m
m
0
0
1
m
5
,
0
°
0
9
d
n
e
b
c
i
r
t
n
e
c
n
o
c
m
m
5
2
1
m
5
,
0
°
5
4
d
n
e
b
c
i
r
t
n
e
c
n
o
c
5
2
1
m
5
2
,
0
*For horizontal Flueing the reduction for appliance bend or turret are already included.
max. 3 m
concentric
100/60
max. 4 m
concentric
100/60
Fig. 22a
Fig. 22b