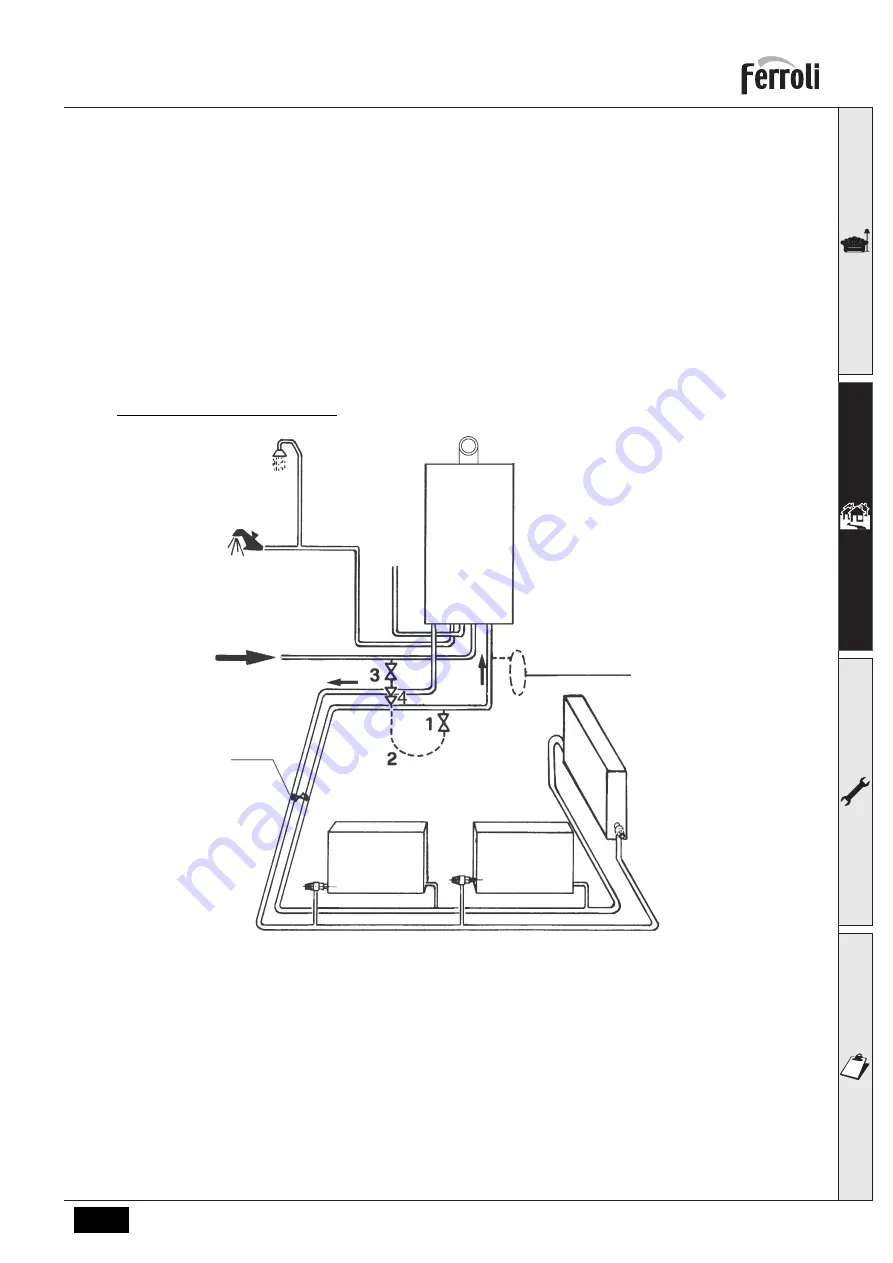
BlueHelix HiTech RRT C
19
EN
cod. 3541V691 - Rev. 00 - 04/2022
Before installation, carefully flush all the heating system pipes to remove any residuals or impurities that could affect
proper operation of the unit (as required by BS 7593 Building regs Doc L).
Carry out the connections to the unit as indicated in .
B
The safety valve discharge must be connected to a 15 mm diameter copper pipe
descending from the boiler to run off system water in case of overpressure in the
heating circuit. Otherwise, the boiler manufacturer cannot be held liable if the dis-
charge valve operates and floods the room. The discharge must be run to the out-
side of the building to prevent the risk of damage or injury caused by discharged
hot water in case of overpressure in the system.
Connections to the boiler are to be made in such a way as to ensure that its internal pipes and fittings are free of stress.
If a non-return valve is installed also on the DHW circuit (if provided for), it is necessary to install a safety valve between
the boiler and circuit (with non-return valve at least 3 metres from the boiler) or an expansion tank for domestic use.
Typical System By-pass layout
fig. 28
The automatic by-pass must be installed a least 3 metres from the boiler & set to allow a minimum of 6 ltr/min through
the valve when all TRV's are closed.
Gas
Hot water
Additional expansion
vessel C.H. (if required)
Filling
point C.H.
Automatic
Bypass
Cold water mains
Summary of Contents for 47-267-74
Page 42: ...BlueHelix HiTech RRT C 42 EN cod 3541V691 Rev 00 04 2022 fig 51 fig 52 fig 53 5 6 6 ...
Page 61: ......
Page 62: ......
Page 63: ......